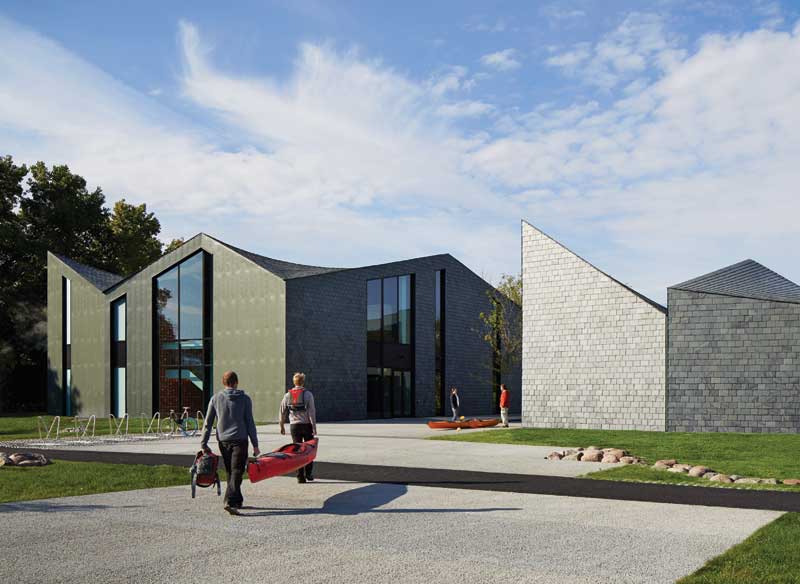
by Ben Kweton, CSI-EP
With natural roof and façade metal materials that have been in use for centuries, importance should be placed on specifying a material not solely for its longevity, but also with an understanding of its long-term aesthetic potential (and pitfalls). Just as we do not plant saplings without the idea of them one day growing into trees, zinc cannot be specified without an appreciation for the patina and aging process. The material is long-lasting, lends itself to unique detailing, and is amazingly versatile, but an understanding of the maturation process manages client expectations and allows a specification to leave a legacy long after the project is complete.
Architectural zinc has enjoyed a successful history of European application for almost three centuries and increasing popularity in North America since the early ’90s. As an alloy primarily comprising of zinc with additional controlled amounts of titanium and copper, the material provides a unique, low-maintenance aesthetic at an extremely low amortized lifetime cost.
Freshly produced natural ‘bright-rolled’ zinc will have a shiny silver appearance and a smooth finish. Without any applied protective organic coatings, it will also be the surface condition that begins the patina process the fastest. Bright-rolled zinc is the material on which most other ‘weathered’ products are based. Without the head start of a secondary patination process, natural zinc can be expected to slowly weather to a matte-gray patina. The duration of this process depends on environmental and building conditions, with the greatest predictor of final appearance being the observation of local in-situ projects that have been through several years of exposure.
Common surface patina is achieved through the formation of first zinc hydroxide or Zn(OH)2, then zinc carbonate (ZnCO3). Both of these compounds not only add to the aesthetic appearance of the product, but also protect the material and increase its longevity.
In marine environments, zinc, combined with salt in the air, will form zinc oxychloride (Zn2OCl2) on the surface. In an age where most people lack the patience and foresight to enjoy the natural process of patination, there are several methods of producing zinc with a more aged appearance. The three main sources for these enhanced surface conditions are phosphating, pigmentation, and a natural pickling process.
The phosphating process deposits a phosphate-crystal coating onto the natural zinc alloy. The duration of the phosphate process and thickness of the coating determine the finished color range and luminance. Thus, this method produces a zinc coating rather than a head start on the natural patina process. Any scratching or scuffing will reveal the underlying alloy and start to weather naturally, potentially causing aesthetic concerns. Through the life of a phosphate product, the alloy is expected to eventually develop its natural patina compounds and force the phosphate coating to give way.
Tinted products can be produced in a multitude of colors and are typically applied over natural bright-rolled or phosphate zinc. The initial appearance usually preserves the initial random and natural texture of zinc and these coatings. Just as with the phosphate surface aspect, the pigments can be expected to fade and the natural patina of zinc to overtake the initial appearance. Exposure, slope, environment, and wetting and drying cycles all play a part in determining how long this process will take.
Lastly, a weathered look can be achieved through a pickling process, where the alloy is etched in an acid bath to achieve either a natural blue-gray or graphite-gray appearance. It is important to note in the case of pickling, the process is actually bringing out the natural patina formation, and two separate alloys are responsible for the different shades (blue-gray and graphite-gray).
After long-term weathering, the materials will remain lighter and darker by comparison. The initial appearance of these surfaces tends to have a subtle directional grain running lengthwise through the material, though this grain will dissipate as the patina develops. Should either of these surfaces be scuffed or scratched, the self-healing properties of the alloy will restore the surface through repatination, eventually matching the surrounding metal and becoming unnoticeable. The healing process is a distinct advantage over phosphate and tinted products that use a single alloy.