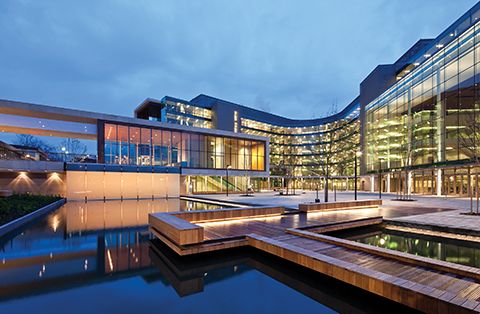
by Steve Marino
Insulating glass (IG) units—or IGUs—have come a long way in the past 70 years. Originally mass-produced in the early 1940s to decrease noise and increase passenger comfort in Pullman railroad cars, the technology has transcended that mobile application and become integral to a business much more stationary in nature—the building industry.
Driven by the principles of sustainable design, IG units are being designed with increasing sophistication. They are incorporating multiple cavities, coatings, and tints, and are being combined with laminated glass, acid-etched patterns, spandrels, interlayers, and other finishes to boost glass performance while achieving stunning visual effects.
Adding to that complexity is growing demand for large IG units—in other words, those that are 4.5 m2 (50 sf) or larger. Improvements in glass manufacturing and the performance of solar-control, low-emissivity (low-e) coatings, together with building information modeling (BIM) and advanced design software, are making curtain walls and large IG units that were once difficult to conceive easier to integrate into building designs.
Unfortunately, such progress has done little to make large IG units easier to engineer, fabricate, deliver, and install. There are still plenty of logistical challenges to overcome, particularly considering the customized nature of most large IG unit designs. With those factors in mind, this article examines seven issues that need to be addressed with glass fabricators and glazing contractors when designing or specifying large IG units for a building envelope:
1. Weight
The sheer heft of large IG units make them difficult to handle and, therefore, more vulnerable to damage during fabrication, shipping, and installation. A standard 25-mm (1-in.) IG unit with two lites of 6-mm (¼-in.) glass and a 12-mm (½-in.) air space weighs about 29.5 kg (65 lb) per 1 m2 (10 sf).
Figure 1 shows the calculated weight of a variety of standard 25-mm (1-in.) IG units. Due to the specialized challenges working with oversized IG units, architects are best-served to collaborate with glass fabricators and glazing contractors who have the demonstrated capabilities, equipment, and experience to handle them. Possible solutions include:
- special heavy-duty lift assists;
- heavy-duty oversize conveyors;
- oversized furnace-tempering capability;
- oversized IG unit assembly capability; and
- oversized lamination capability.
All fabricating equipment can handle larger sizes of glass with a heavier weight limit that is not typical in the industry.
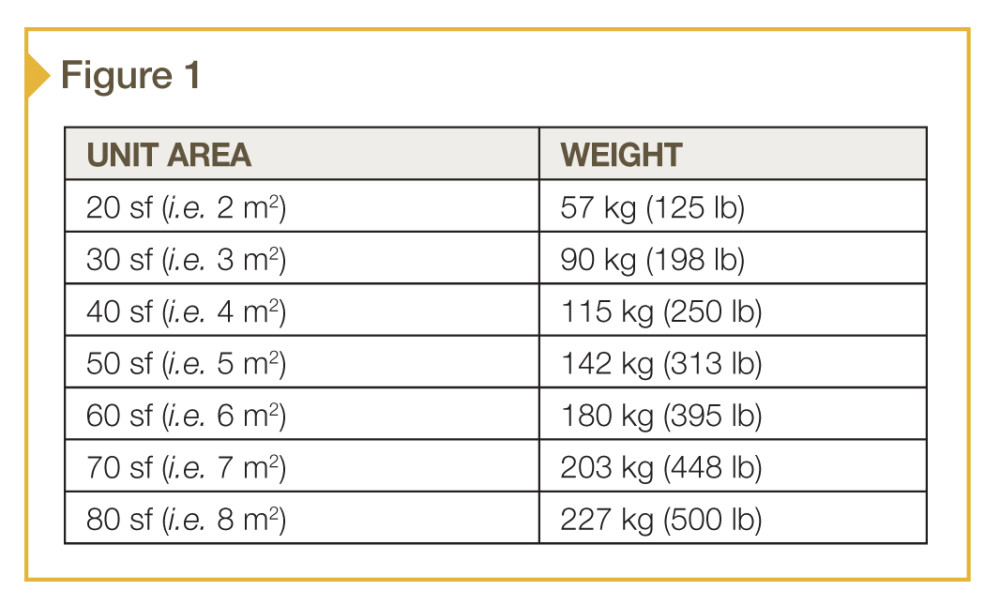
2. Heat-treating
Large IG units have expansive surface areas that make them vulnerable to wind loads and thermal stress caused by extreme temperature variation from the center-of-glass to edge-of-glass.
As a consequence, fully tempering or heat-strengthening glass is recommended for large IG units to enhance their resistance to these threats. Unfortunately, the trade-off for greater strength is increased potential for visual distortion in large IG units caused by bowing or warpage that is inherent to the heat-treatment process.
Most glass fabricators who work with large IG units know how to accommodate the increased potential for bowing and warping. Nevertheless, architects should work with glass suppliers to establish acceptable tolerances for these variables as part of the bid and specification processes.