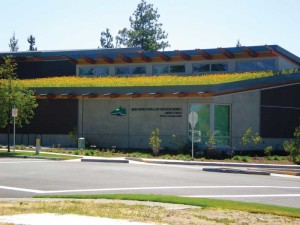
Roofing considerations
Similar to conventional OSB-sheathed roofs, SIP panels should be dry before the roofing underlayment is installed. In cases where moisture remains in the OSB, an alternative to 15# or 30# roofing felts is a synthetic, breathable roofing underlayment. Such underlayments have permeance ratings substantially greater than 1 perm to allow water vapor to pass through them, yet restrict bulk water movement back toward the SIP panels’ OSB. It is important to check with the underlayment manufacturer for any compatibility issues with the planned roof covering material.
In commercial applications, SIPs can be specified for low-sloped roofs. Such roof assemblies typically include a single-ply, builtup roof (BUR) or modified bitumen (mod-bit) system. Methods to secure the roof membrane include ballasted, adhered, and mechanical attachment. SIP manufacturers usually recommend the specifications include a divorcement material placed over the panels before the roof membrane. This can be a slip sheet on ballasted systems, a nailed base sheet on BUR systems, or a cover board (such as gypsum or wood fiber) with adhered systems. The divorcement materials protect the SIP panels.
Beyond protecting SIP roof assemblies from water intrusion, specifications should address code requirements for Class A, B, or C fire-ratings for roofing placed on a combustible deck—based on ASTM E108 or UL 790 Standard Test Methods for Fire Tests of Roof Coverings. For a Class A rating, one of the easiest methods is to include a layer of gypsum board over the SIPs. As with other aspects of wall and roof assembly design and construction, one must confirm requirements with the SIP manufacturer and local codes.
Conclusion
Construction with structural insulated panels is not unique in requiring attention to air and moisture management details. The techniques are straightforward and similar to those required with other wall and roof systems. When SIPs are installed according to best practice, with proper air seals and flashed penetrations, the system is durable in all climates.
One practical demonstration of this point is the successful application of SIPs in vegetated roofs in northern climates, such as the Parks and Recreation District administration building in Bend, Oregon. In such assemblies, the panels support the weight of soil and plantings, and incorporate systems that serve to protect against water intrusion despite the wetted soil. (For additional information on working with SIPs, a good reference is Joseph Lstiburek’s book Builder’s Guide to Structural Insulated Panels for all Climates. Structural Insulated Panel Association [SIPA] and manufacturers can also provide resources and guidance on appropriate design and construction methods for SIP buildings.)
Joe Pasma, PE, is the technical manager for Premier SIPS by Insulfoam. The company is a North American manufacturer of high-performance, energy-efficient structural insulated panels (SIPs). A licensed structural engineer, Pasma has worked with SIPs for almost two decades. He can be reached via e-mail at jpasma@premiersips.com.