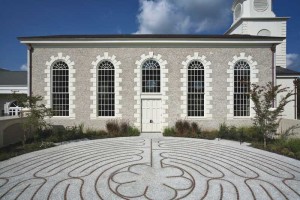
Photos courtesy Tilt-Up Concrete Association
Due to the slim margin for error and extremely tight tolerances, all panel edges were over-poured and cut to size. This process not only ensured the dimensional accuracy of the panels and a crisp clean edge, but it also reduced the time needed to polish the burdensome edges and returns. Additionally, by cutting the edges after the face of the panels had been polished, the polishing process could be taken to the edge without fear of chipping. The concrete mix design for the panels consists of various unique elements, including:
- Meramec Gravel, a natural river stone that comes from Missouri;
- glacial sand;
- black pigment; and
- Dresser Trap Rock, known as one of North America’s hardest rocks.
The process for getting these panels to this point took some hard work, a great deal of ingenuity, and skilled craft.
Julie Bauer, the lead design architect for David Chipperfield Architects on the project, was amazed at the level of craft being accomplished on these panels. She said one of the most interesting aspects of the process was the construction crew was seemingly inventing tools and methods on the spot for troubleshooting areas and getting the panels to a state of which they could be proud. Every square inch of each panel was cared for and worked to perfection.
The director of the museum elaborated on the concept of going with these relatively enormous handcrafted panels over, say, granite tile. He said instead of being made up of small panels, the project was to be made up of massive, monumental panels appropriate to a public building that will be here for a century more.
Not only possible, but practical
More and more designers and contractors are discovering complex forms and rich textures are not only possible with tilt-up, they are actually practical. Located in a small beach community just a short drive from Charleston, North Carolina’s historic district is a simple church with a unique finish. The contractor said site-built tilt-up panels was chosen as the delivery method for a substantial addition because it was the only accessible way to produce the desired results in an economically feasible manner. The goal was to replicate a tabby or tabby stucco finish.
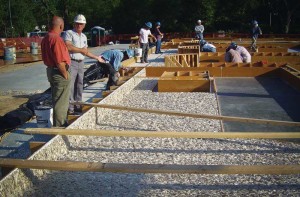
The term ‘tabby’ refers to a centuries-old, southern U.S. coastal building material composed of equal parts of homemade lime, sand, oyster shells, and water. Once dried, they would then place a surface layer of stucco over the wall to protect the finished product. Over time, the recipe has been modified to include portland cement. This variation exposes the shell and foregoes the stucco, which is not an entirely accurate recreation (which is common), but a weathered take on the historic material.
To adopt the technique for tilt-up, the team brainstormed and tested mockup panels. The solution consisted of hand-stacking the oyster shells in a 9.5-mm (3⁄8-in.) thick sand-bed and using white cement to bond the shells in a textured layer, and then constructing the structural layer. The best part of all of this is the congregation was invited to participate in the placing of the shells. Since each hand had its unique way of setting a shell, the entire group of workers shifted and traded positions at timed intervals throughout the process to avoid large areas looking different from others. The result is a uniquely beautiful texture.