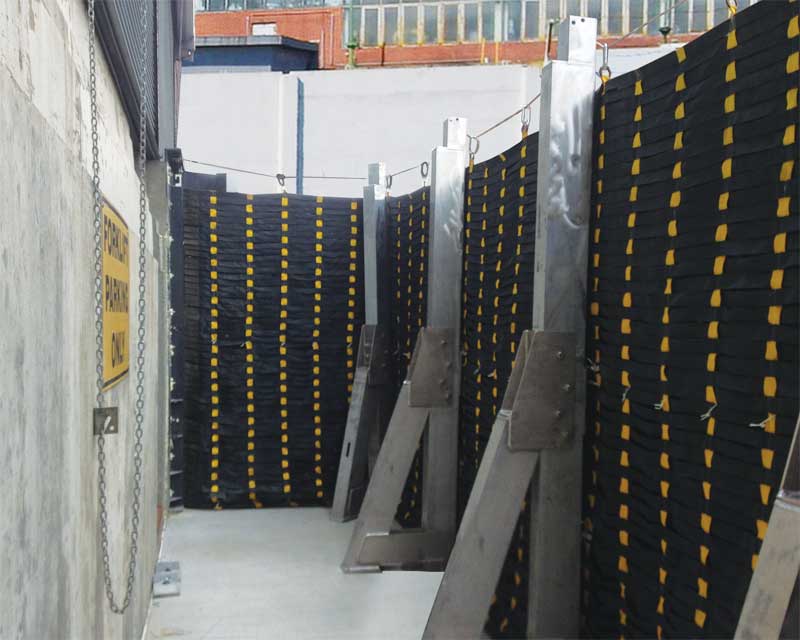
Building standards
Building standards established in Chapter 16 of IBC and in ASCE 24-14 reflect and support the minimum floodproofing and construction criteria established by FEMA’s regulations and Technical Bulletins. In many cases, they go above and beyond those requirements to establish higher standards that have proven to be needed.
Addressing use of specific materials and construction methods, IBC provides a model code and minimum standards for building materials, building structure, safeguarding of public health, safety, and general welfare of occupants. Of most relevance to the current topics are Chapter 16, “Structural Design” (particularly structural loads, including from flooding) and Appendix G, “Flood-resistant Construction.” Under the former, Section 1612, “Flood Loads:”
- requires communities to adopt maps of flood hazard areas (which, incidentally, provide public notice of where regulations apply and support municipal floodplain management decisions);
- recommends implementation of design flood elevations to raise lowest floors above base flood elevations;
- establishes ASCE 24 as one of the primary standard documents for design and construction within the SFHA; and
- mandates registered design professionals provide flood hazard documentation (e.g. elevation of lowest floor and certifications regarding floodproofing and construction design).
Floodproofing
Generally, floodproofing is the implementation of structural and nonstructural methods to reduce flood damage to a structure, its contents, and related utilities and equipment. The object is to minimize both hydrodynamic and hydrostatic pressures of floodwaters against the walls of a structure—‘hydrodynamic’ referring to the force of moving water and ‘hydrostatic’ to the weight and pressure of still water.
FEMA TB 3, Nonresidential Floodproofing–Requirements and Certification for Buildings Located in Special Flood Hazard Areas, identifies some of the minimum engineering considerations of dry floodproofing. These include a requirement to make the building watertight to the floodproof design elevation, being at least 0.3 m (1 ft) beyond BFE. (The additional 0.3 m of freeboard is critical for NFIP flood insurance rating purposes.)
A dry-floodproofed building’s structural components must be able to resist hydrostatic and hydrodynamic flood forces, buoyancy, and debris impact forces. Another great resource for understanding the requirements as they pertain to existing structures is FEMA P-936, Floodproofing Nonresidential Buildings.
Dry floodproofing can include passive measures such as waterproof sealants and coatings on walls and floors, along with automatic backflow prevention valves and sump pumps. However, it may also involve active measures—such as flood barriers, gates, shields, or doors—that must be manually activated when high water is expected. The designer has to account for important planning considerations by knowing answers to the following questions:
- How much warning time is likely to be available?
- How will people enter and exit the building?
- What is the flood frequency in the area?
- What are the expected floodwater velocities, flood depths, and debris impact?
Features of dry floodproofing systems include:
- sealants, coatings, and membranes to reduce seepage of floodwater through walls and their penetrations;
- flood barriers, shields, and panels for openings (e.g. doors and windows) attached to the structure’s façade;
- reinforcement of walls to withstand floodwater and floating debris;
- anchoring of the building to resist flotation, collapse, and lateral movement;
- pumps to control interior water levels due to seepage;
- check valves to prevent the entrance of floodwater or sewage flows through utilities;
- location of electrical, mechanical, utility, and other valuable damageable equipment and contents above the expected flood level or DFE; and
- a minimum of one ingress/egress door or other approved opening above the established DFE.
Dry floodproofing requires emergency operation planning, some of which is related to site selection. As some approaches include placing barriers over openings, advance disaster planning is crucial to ensure all individuals are out before sealing and locking those barriers. Engineering considerations for dry floodproofing include a regular inspection and maintenance plan to ensure all components operate properly under all conditions, including power failure. Mechanical equipment, generators, flood barriers or logs, and flood shields (including gaskets) should be inspected and repaired annually (at minimum). Further, foundation walls, levees, and berms must be inspected and repaired to ensure there are no cracks.