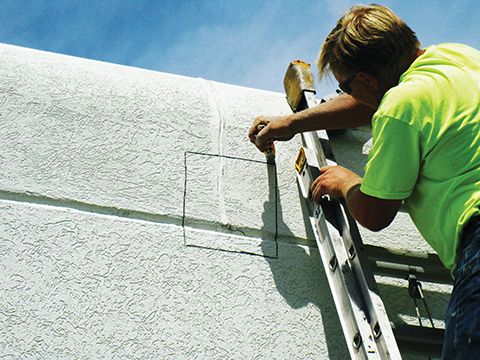
Code compliance
Widespread incidences of failure have prompted code restrictions on the use of EIFS. The architect or engineer should check local building codes to ensure compliance before installation.
Fire rating
In January 2008, the Monte Carlo Hotel in Las Vegas, Nevada caught fire, prompting concerns about flame propagation and EIFS safety. A follow-up investigation found the cladding
in the area of the fire had non-code-compliant lamina that was significantly thinner than required, as well as large decorative elements exceeding maximum allowable EPS thickness. Manufacturers test EIFS systems for fire resistance; however, substituting untested coatings, insulation, or substrates for approved EIFS materials have been shown to increase flammability. The system installed should be identical to the one that has been fire-tested and approved.
Energy code
Mounting energy concerns have driven the International Energy Conservation Code (IECC) and other relevant codes, such as American Society of Heating, Refrigerating, and Air-Conditioning Engineers (ASHRAE) 90.1, Energy Standard for Buildings Except Low-rise Residential Buildings, to ever more stringent requirements. Since 2006, the IECC has required both stud cavity insulation and continuous exterior insulation. Continuous insulation is integral to EIFS and retrofitting an existing building with EIFS can be a simple and inexpensive way to comply with increasingly rigorous energy codes.
Wind load
Compared with mechanical attachment, adhesive attachment of EIFS board insulation has been demonstrated to provide superior wind load resistance. To achieve full design performance, the supporting construction must be free from damage, defects, and contamination before insulation is adhered. Sheathing must be capable of independently resisting anticipated wind loads.
Building codes
The 2009 edition of the International Building Code (IBC) was the first to include a section on EIFS and the guidelines, which remain unchanged in the 2012 edition of the model code, and incorporate information on both traditional EIFS and EIFS with drainage. However, the section is brief and directs users to refer to manufacturers’ guidelines.
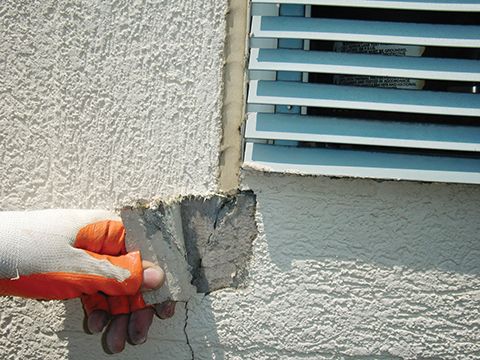
Field verification and quality control
With construction underway, the design professional should verify the proper materials have been ordered and delivered, and that materials have been shipped and stored at appropriate temperatures and conditions. Before EIFS application, the architect or engineer should check the substrate for correct surface preparation, cleanliness, and proper tolerances. To confirm construction complies with drawings, specifications, and manufacturer’s recommendations, the design professional may conduct periodic field evaluations of the EIFS installation progress. He or she should confirm the correct installation of critical related elements, including flashing, sealant, windows, and doors.
EIFS are proprietary systems. Each manufacturer conducts its own research and development for compatibility and performance of their independent EIFS product. Therefore, it is important to specify an entire system from a single-source manufacturer to avoid compatibility issues. Part of the field verification process should include confirmation that the entire assembly functions as one integral system. Many manufactures and industry organizations provide online inspection manuals and verification checklists that can be used to guide independent quality control evaluations.
Maintenance and repair
To keep EIFS looking and performing their best, building owners should implement inspection and maintenance practices to address incipient problems promptly.
Cleaning
EIFS finishes and sealants should be inspected for damage or wear at least twice a year. EIFS should be cleaned thoroughly every five years—locations prone to algae and fungal growth may require more frequent cleaning. Options for EIFS cleaning include commercial detergent, pressure washing, or a trisodium phosphate (TSP) solution. Washing with cold water is recommended, as hot water can cause acrylic finishes to soften. Difficult stains—such as those from wood, tar, asphalt, efflorescence, graffiti, or rust—may require sealing and re-coating.
I didn’t know there were so many different types of insulation. I like having different choices so this is great for me! Insulation is a crucial part of building an efficient structure so this will be really helpful.
Great explanation of the different types of insulation available. I had no idea there were so many different kinds so this is really helpful.
I had no idea there was a difference between stucco and exterior insulation and finish systems. I assumed that stucco was the same thing as the insulation board and exterior coating that you are discussing in your article! I’ll be sure to look at my options more carefully when I need some exterior waterproofing done!
The article has a beneficiary content, which has helped me a lot in understanding. It is a very informative blog which everyone should read to know.