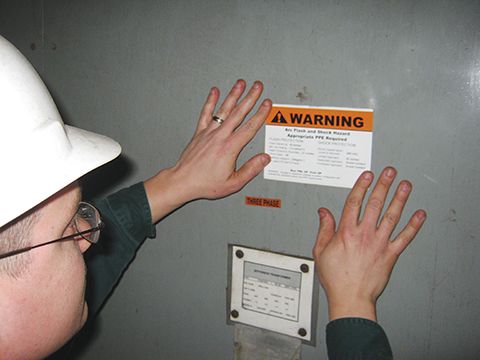
Provide proper training
In addition to preparing the study and labeling all equipment, there is a third, critical piece to administrating the electrical system—training.
Personnel need to be thoroughly educated on how to safely use all electrical equipment. Simply labeling everything is not enough if staff members do not know what the labels mean or how those labels should inform the electrical maintenance process.
Most electrical work performed in buildings should be performed on de-energized equipment, but that is not always possible in facilities related to healthcare, research, or industry, or any building where managing interaction with electrical equipment is not rigidly controlled. Even when working on de-energized equipment, personnel must remove the equipment cover first, which can put the user in danger until he or she has confirmed the panel board is indeed de-energized. It is imperative personnel are trained to properly remove equipment covers and test the system.
Personnel also need to be trained to understand when they should not touch equipment. For example, many buildings obtain their electrical power from secondary services supplied by local power companies. Arc flash studies indicate incoming switchboards served by transformers 500KVA or larger, and especially those with a 208-volt incoming service, will most likely be labeled as ‘dangerous.’ In those cases, an outage by the power company is required before any work can be done on the switchboard—even for something as simple as resetting the breaker.
At a minimum, all personnel should learn how to interpret each label, identify the proper PPE to wear in various scenarios, safely de-energize equipment, and navigate the best practices of typical electrical work.
While equipment labeling may seem nonessential, it is worth the effort in the long run as it can prevent serious injury and save lives. Should a worker be injured on the job due to improperly labeled electrical equipment, the building owner could be found at fault and be required to compensate the worker. Some injured workers have received millions of dollars because of facility negligence. Additionally, the Occupational Safety & Health Administration (OSHA) has fined companies tens of thousands of dollars for not having the appropriate procedures in place for workers who interact with electrical equipment on a regular basis.1
Costs
Arc flash labeling can be accomplished by a small increase in cost on new construction and can be a specified requirement as part of the contract documents. On existing buildings, the cost to prepare an arc flash study depends on the size and age of the building, and on good documentation. Bundling as many existing buildings as possible into one contract is a great way to make the process more cost effective. It is important to remember when working with or counseling building owners who need to prioritize costs, the cost of not bringing an electrical system into code compliance and experiencing a hazardous incident is much greater than the expense to actually take these precautionary measures.
All three steps—the arc flash study, equipment labeling, and training—along with properly maintaining the system on an ongoing basis, will minimize the likelihood of a hazardous event and a lawsuit against the building owner.
There is an array of services available when preparing a specification or proposal for solicitation of an arc flash study. This author has seen a facility where every panelboard was labeled ‘dangerous,’ which protected the owner but made maintaining the system much more cumbersome. This is because each piece of equipment had to be de-energized, meaning portions of the building were without power, when a ‘Category 1’ labeling and PPE would possibly have sufficed.
When soliciting for an arc flash study, the proposal should:
- be prepared by a licensed engineer with experience in similar studies (and references);
- utilize a recognized software system such as SKM, Easy Power, or ETAP;
- be comprehensive, from service entrance equipment to disconnects on motors;
- include remedial adjustments of existing equipment to obtain the lowest PPE category possible without impacting system reliability on existing systems;
- provide equipment layout recommendations in order to take advantage of a device’s incident energy reduction capability for new systems in the design phase;
- give special consideration to arc-flash reduction techniques in areas where system interaction will be necessary;
- include a complete single line diagram of the electrical system for posting at the service-entrance of equipment; and
- perform to meet the requirements of compliance with NFPA 70E, consistent with Institute of Electrical and Electronics Engineers (IEEE) 1584.1-2013, Guide for the Specification of Scope and Deliverable Requirements for Arc-flash Hazard Calculation Study.
As with all specification writing, the more detailed the requirements, (i.e. clear, concise, correct, and complete) the better the quality of the product.
Stephen Devon is an electrical engineer with more than 30 years of experience in program planning, feasibility studies, and project management of multi-discipline projects and associated staff. He remains informed of the latest technologies of not only his discipline, but also of others to ensure the right approaches and systems are being implemented. Devon works to bring together the in-house disciplines and other consultants and takes into consideration construction issues to ensure a successful project. He can be reached at steve.devon@rmf.com.