Transforming Chicago’s riverfront
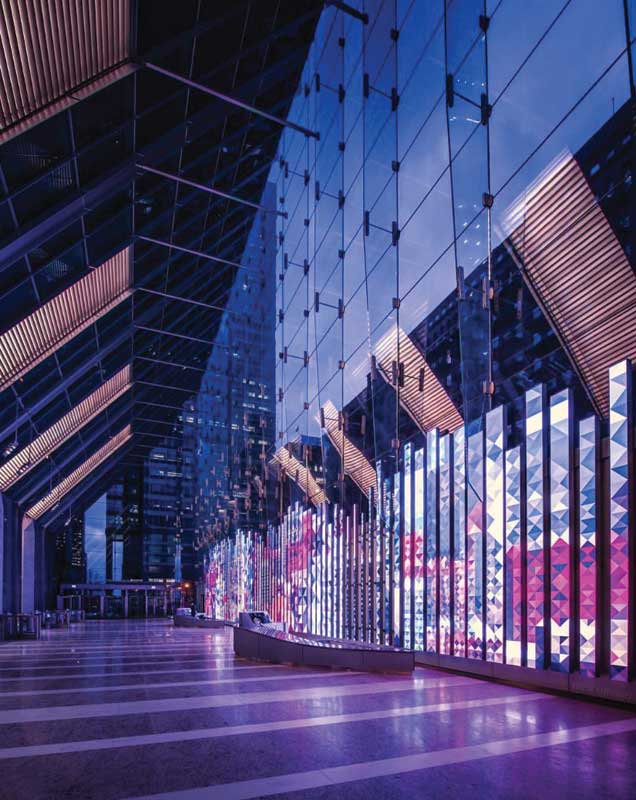
Utilizing the river
Once the foundation was complete, the team turned their focus to erecting steel and placing concrete, including enclosing the active rail lines to create a public plaza. The team used 9-m (30-ft) tall, cast-in-place concrete walls and precast concrete bulb tees to cover the tracks. The site was too crowded to support a land-based crane with a reasonable reach, as there was limited site access, buildings, and elevated roadways nearby. A tower crane also could not lift the bulb tees, requiring as much as 58,059 kg (128,000 lb) of lifting capacity. With no space for a crane onsite, the project team turned the adjacent Chicago River from a challenge to an asset and designed a floating platform system to employ the use of a massive barge-mounted crane.
All this river-related activity required cooperation from the city, the Coast Guard, the U.S. Army Corps of Engineers (USACE), and the Metropolitan Water Reclamation District.
With a maximum 91 m (300 ft) of boom and 598,742 kg (660 tons) of lifting capacity, the 907,184-kg (2 million-lb) crane setup distributed groundbearing pressure evenly across the barge’s 31 interlocking sections. Anchored by four spuds driven into the riverbed, the barge allowed the team to pick up the bulb tees over the rising building core and set them up to 6 m (20 ft) away on the site’s west side, without taking up space on the jobsite. The project team used the crane to install nearly 200 bulb-tee girders, weighing as much as 40,823 kg (90,000 lb), to support the tower’s new pedestrian plaza. To top out the superstructure, the team poured 42,050 m3 (55,000 cy) of concrete, placed 10.8 million kg (12,000 tons) of rebar, and erected 9 million kg (10,000 tons) of steel.
Engineering
After the foundation was completed, the project team utilized some of the world’s highest-strength steel and largest-rolled shaped steel—W36x925—to bring the building to life and achieve the necessary strength and stiffness in the structure. In addition to using 482-MPa (70-ksi) rolled shapes for the first time in the United States, the fabricators pre-fitted the steel for the transfer truss in the shop itself to confirm every single bolt hole aligned, with no welding or reaming of bolt holes on the entire transfer system. The team preplanned every step to prevent any issues in the steel truss and concrete core connection for constructing level floors.
To connect everything properly, the project team sequenced the work in a very particular fashion. The biggest sequencing component was the building’s signature lobby, which features a 25-m (85-ft) tall glass wall hung from the tip of the transfer truss at Level 8.
The team ran two independent schedule paths from the project to ensure the tower and plaza construction met at the correct point in time and the tower’s structure did not get in the way of the crown.
Managing drifts
To meet drift and acceleration standards, Magnusson Klemencic Associates, a structural engineering firm, introduced tuned mass dampers, housing some 757,082 L (200,000 gal) of water in 12 concrete tanks stacked in two layers of six, at the building’s top. The inertia of the water in the tank creates a balancing liquid force against the structure in order to keep the narrow building from drifting.
While tanks have been used to manage accelerations in the past, this is one of the world’s first cases in which tanks manage drifts to keep the cladding joints from overstressing from story drift. The water tanks also serve as city-approved fire protection water.