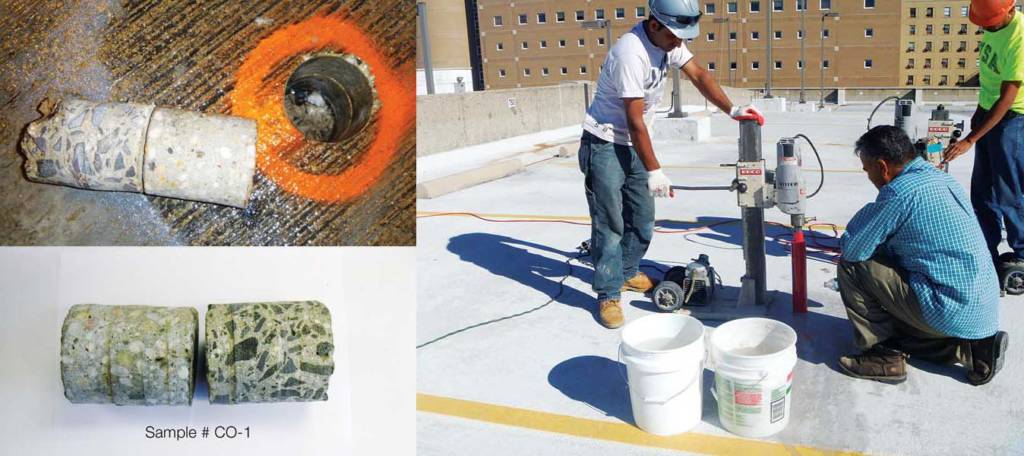
Advanced corrosion results in spalls, or large chunks of concrete falling away from the structure. At this stage, deterioration is hard to ignore. Much earlier, though, the prudent building owner or manager can look for signs to identify incipient problems. Rust-colored stains at the surface of concrete can indicate corrosion below. Hairline cracks and fissures that develop over time might also be indicative of expansive stress, as an increasing volume of rust exerts pressure on the surrounding concrete. Standing water and leaks, as well as accumulated de-icing chemicals on deck surfaces, may be early warning signs of conditions conducive to corrosion.
Once corrosion has progressed to concrete delamination and exposed rebar, the cost of rehabilitation can be high. Reinforcing bar with mild corrosion may be salvaged and treated, but severely corroded steel may need to be cut out and replaced, and the concrete recast. Entire areas of the deck could require complete reconstruction, at great expense and with extensive downtime. Therefore, protecting parking decks against corrosion and treating symptoms early should be a priority.
Why rebar corrodes
High levels of calcium hydroxide in concrete make it a highly alkaline material, with a pH typically above 12.5. Values for pH ordinarily range from 0 to 14, with 0 being most acidic, 14 most basic/alkaline, and 7 being neutral. (For comparison, household bleach has a similar pH to that of concrete, while lemon juice has a pH of around 2.2.) This alkaline environment protects the embedded reinforcement by creating a passivating film around the steel. Since the electrochemical reaction of corrosion can only take place in a neutral or acidic setting, the alkaline concrete prevents steel oxidation and guards against deterioration.

Carbonation is the process by which this protective environment degrades, subjecting the reinforcement to corrosive forces. When rainwater combines with carbon dioxide in the air, it forms carbonic acid, which combines with the concrete’s calcium hydroxide to form calcium carbonate. As the concentration of calcium carbonate in the concrete increases, the pH decreases, reducing the concrete alkalinity and compromising the passivating film around the embedded steel. While not a direct cause of corrosion in itself, carbonation fosters an environment that hastens the process.
Where concrete deterioration is observed, chemical analysis of the damaged concrete may be performed to measure the extent of carbonation. Water-repellent coatings or elastomeric waterproofing membranes may be applied to mitigate ongoing carbonation by preventing migration of carbonic acid into the concrete.
Moisture is essential to the corrosion process, both as an electrolyte solution and as a reagent. Water is also the vehicle by means of which acids, sulfates, or chlorides are transported into the concrete, creating an acidic environment that accelerates corrosion of embedded steel. As concrete cures, excessive mixing water not used in the hydration process can leave capillary voids in the finished product. This leads to freeze/thaw damage, where the concrete cracks and crumbles due to expansion forces of freezing water in these voids. This damage then provides a direct path for corrosive elements to reach the embedded steel.
Chloride contamination hastens corrosion by conducting electrical currents via chloride ions and accelerating the oxidation of iron atoms. Chloride intrusion also reduces the pH of concrete and destroys the passivating film around steel reinforcement. The most common source of chlorides is de-icing salt used for snow and ice removal, but those organic compounds are also present in acid rain and in the accelerators used in some older concrete structures to offset delays in strength gain and setting caused by placing concrete in cold weather.
Rebar in concrete that has undergone carbonation and de-passivation has lost the protective layer around the reinforcing steel. Therefore, it is susceptible to accelerated corrosion from even low concentrations of chlorides. Laboratory tests can measure the extent of chloride contamination as part of an investigation and repair project. (Chloride contamination above 300 ppm is generally considered the threshold that sustains active corrosion of embed unprotected reinforcing steel.)
Galvanic coupling contributes to corrosion through electrolytic contact between dissimilar metals. When metals with different electrical potentials come in contact in the presence of an electrolyte (e.g. water), metallic ions migrate from one metal (i.e. the anode) to the other (i.e. the cathode). The result is corrosion of the anode metal—in this case, the reinforcing steel. Electrically insulating dissimilar metals prevents galvanic corrosion, as do water-repellent coatings that prevent contact with an electrolyte. Use of sacrificial anodes of a metal more active than the reinforcing steel (e.g. zinc, magnesium, or aluminum) is another means of preventing corrosion due to galvanic coupling.