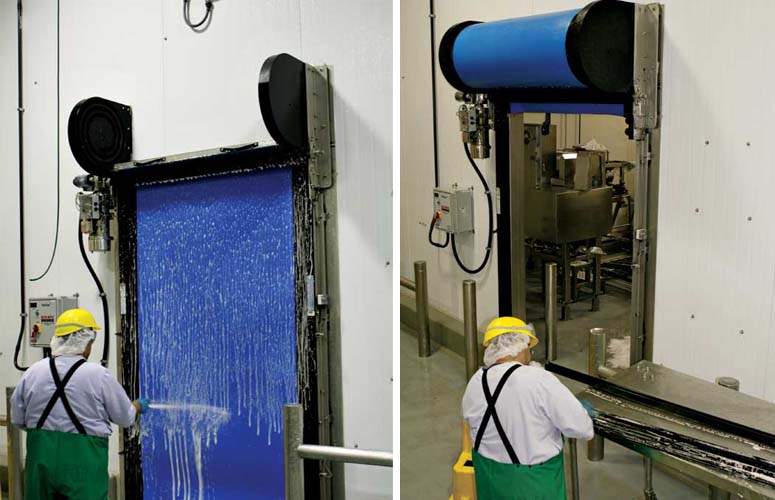
Specifying high-speed roll-up doors
Bi-parting doors of stainless steel or fiberglass are widely used in pharmaceutical manufacturing facilities. However, many companies also use fabric roll-up doors to meet the needs of specific applications where the bi-parting doors will not fit, due to limited wall space in many plants.
A roll-up door uses little wall space because it is an upward-acting unit. In other words, the curtain of the door collects in a head assembly at the top of the door when it is opened. By comparison, depending on the configuration of adjacent walls, a rigid-panel door that opens from the center may require considerable wall space on each side of the door in order to function. As an example, a door spanning a 1.8-m (6-ft) wide opening may require approximately 0.9 m (3 ft) of wall space on each side of the opening so each panel has a place to travel when opened.
A new generation of roll-up doors has come on the market in recent years featuring anti-microbial materials and other upgrades for clean room applications. These new features—along with their ability to operate at high cycle speeds and provide tight sealing capability—are the major reasons they are catching on with pharmaceutical and food manufacturers.
How to choose a clean room door
The U.S. Food and Drug Administration (FDA) publish clean room standards, both required and recommended, for manufacturers of pharmaceuticals and medical devices. The starting point is to look for doors that are compliant with Current Good Manufacturing Practices (cGMP), U.S. Food and Drug Administration (FDA), and United States Department of Agriculture (USDA) requirements.
Regardless of the door’s configuration, ease of cleaning and durability are key considerations. In all cases, these doors must be able to stand up to repeated cleaning with chemical solvents and have a smooth, hard, non-porous surface resistant to microbial and fungal growth. Doors should also have a tapered surface and edges that all but eliminate ‘harborage’ of dust or other contaminants—this also reduces sharp angles that can harbor microbes. Additionally, they should:
- be corrosion-resistant (often a problem with older door systems);
- use stainless steel side frames and shrouds; and
- incorporate a lubrication-free design, since lubricants can attract particulates.
It is also advisable to avoid doors with exposed fasteners and coils, as they will take longer to clean and could harbor contaminants.
The ability of clean room doors to accommodate site-specific needs is another consideration for industrial designers. These could include features such as vision panels, push plates, or other activation devices, as well as magnetic locks and (perhaps most importantly) interlocking systems. Commonly known as ‘airlocks,’ these systems are found in entrances and exits, gowning and de-gowning areas, and material transfer locations. In all these areas, it is important to keep two doors from being open simultaneously, thus preventing air infiltration from one space to the other.
The best door systems allow for wireless interlocking of air locks. ‘Breakaway capability’ is another recent advancement in clean room doors, allowing employees to push through the curtain in the event of a power failure. While this feature is not needed on a daily or even monthly basis, it will be greatly appreciated on the rare occasion it is needed. Finally, low-voltage remote controls should be specified when possible as they provide a cleaner look and are easier to install.