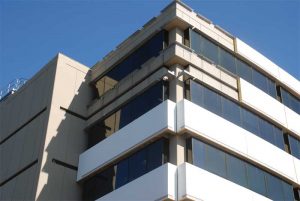
Delivering greater certainty
With site-built exterior walls, certainty is fleeting due to the many unknowns at play. Prefabrication changes the conversation. It produces better scheduling options, increased safety for work crews, and fewer workers on site. This, in turn, delivers the potential for cost savings and faster turnaround times.
Consider the construction of a new hospital. The doctors, nurses, other professionals are ready to start working, and medical supplies are in stock. Patients have scheduled appointments with their providers. Delays in the ultimate completion of the hospital can push back medical treatment for patients who need it. A delayed completion scenario also represents a financial loss for the hospital, which relies on revenue from patient procedures to meet payroll and maintain operations, not to mention potential liquidated damages to the contractor if they are part of the contract. Prefabricated exterior walls as a construction system can create a more predictable completion timeline and add to the probability of the hospital opening on time.
In a controlled manufacturing environment, fabrication crews achieve the benefit of full-time jobs making a product for their own installation teams. They are invested in developing their skills and committed to the mission of repeat business by ensuring that they generate quality results. This contributes to the creation of a higher quality product.
Although prefabrication requires more upfront money for engineering and manufacturing, greater schedule certainty can produce savings in the long run, for example on projects that have a hard completion date. While weather is often a factor in field-built construction, wall panels prefabricated in a climate-controlled facility are not subject to weather-related work stoppages and can be delivered to the site on time, minimizing the risk of delay. Fast install time means the building enclosure is no longer on the project critical path. Moreover, since fewer people are needed to complete a panel assembly and solve constructability challenges, prefabrication can lower the cost of the overall project.
Fully finished exterior wall assemblies are prefabricated at waist height, significantly reducing the risk of injuries. Crews do not perform their jobs at great heights on a high-rise commercial building as they would if they were installing product on site, so there is no need for scaffolding. Since complete wall panels are delivered to the jobsite, management of most packaging and other building material waste takes place offsite. As such, the potential for environmental contamination is greatly reduced.
With significant safety improvements, few or no weather delays and rapid exterior wall installation, speed to market improves. Buildings can be dried in days or weeks rather than months. On average, a 5574.2-m2 (60,000-sf) exterior can be dried-in within a month. For example, prior to installation of the exterior enclosure, the Hyatt House project in Nashville, Tennessee had been delayed by four months. The panels were manufactured offsite in advance of installation and he completed panels were quickly and efficiently installed onsite, making up a total of five months and putting the job a full month ahead of schedule.