
by Tony Schoenecker, PE
Keeping costs down while maintaining the highest standard of safety and meeting building requirements is a goal for any project. In most cases, this is easier said than done, but following best practices in fire protection engineering can provide oft-overlooked ways to achieve this goal.
Neglecting to consider the big picture when making specifying decisions is a common oversight; minor points can quickly add up. This practice often leads to choices that benefit a specific area without taking into account other disciplines (i.e. building classification, fire alarm, passive fire protection, etc.). This may result in increases in capital or maintenance expenses. For example, to reduce cost of a fully sprinklered boiler room enclosure, the smoke partition exception may be provided instead of a one-hour fire barrier. However, this may now require smoke dampers to be installed in the air transfer grilles that were previously not required, in addition to smoke detection for initiation.
Two of the most effective ways to employ a consolidated life safety and asset protection method are merging systems and eliminating unnecessary ones. Incorporating fire-resistive construction, using the building code and its exceptions tothe specific project’s benefit, and employing proper design techniques also present opportunities to implement a holistic approach. Given there are multiple fire protection systems in place, it is vital to have a coordinated and cohesive plan.
Simplicity through multi-disciplinary coordination
Harmonizing multi-disciplinary systems—such as egress, public address, fire alarm, and storage—presents an opportunity to simplify maintenance and design while also lowering project costs. Since fire protection is a multi-disciplinary practice (i.e. architects for egress and fire barriers, mechanical engineers for sprinkler assemblies, and electrical engineers for fire alarm systems), the synchronization of these systems is often overlooked.
By coordinating and understanding a building’s classification and egress system early on in the design phase, projects are more likely to stay on schedule and see increased interdisciplinary coordination. If changes in the building classification or modifications to the floor plan to address egress issues (e.g. number of exits, dead-end corridors, common paths of travel, or maximum travel distances) happen after the fact, the design budget and project schedule can be considerably hampered. It is always best to solidify these early in the project and long before the permit review set is issued.
When it comes to building systems, more is not always better—this is certainly true for public address and fire alarm systems. Some buildings have separate public address and fire alarm systems, but integrating them into one, such as a fire alarm voice evacuation and paging system, is an efficient and effective way to control project costs.
Merged systems can sometimes provide all the same functions as two separate ones as well; fire alarm voice evacuation systems can be zoned and programmed to take audio input from a phone paging system, or provide background music, just like a public address system.
Human behavior studies have also demonstrated building’s occupants respond more quickly and effectively during an emergency when given voice instructions. It is consequently critical to ensure the performance criteria for intelligibility and sound power are clearly noted in the voice evacuation system’s specification, so it meets not only the building’s life safety requirements, but also the paging needs.
Just as with fire alarm and public address systems, synchronization is critical when planning storage and sprinkler systems. Coordinating the two make for a more effective process and offer simpler maintenance. An inefficient storage system can drive up water fire demand for the sprinkler systems, even to the point where a fire pump becomes required. By harmonizing these two systems in the design phase, including limiting the product storage height, providing open shelving, employing wood instead of plastic pallets, increasing the aisle width between racks, or providing single- versus double-row rack systems—all strategies that can reduce fire water demand.
Using the code and the exceptions within
Knowing and using the building code and its exceptions to the specific project’s benefit can pay dividends. This all begins with planning that happens before converting the schematic design into a building.
Constructing a building with the most restrictive occupancy requirements in mind can reduce passive fire protection such as fire walls, fire barriers, and fire partitions. As an example, when designing for a building with both business and assembly occupancies, one may be able to eliminate the fire barrier around assembly areas. If the whole building can be constructed within the allowable area of the most restrictive occupancy—in this case, the assembly occupancy—the building can then be classified as a mixed-use, non-separated, and assembly/business occupancy. This removes the need for this fire-rated barrier.
Being aware of the ‘10 percent rule’ to reduce fire-rated construction will also help a project team take advantage of the building code and its exceptions. With this rule, when the limiting occupancy is less than a tenth of the overall building area, it can be considered an accessory to the main occupancy, removing the requirements for fire-resistive construction between the occupancies. It is important to remember this is the aggregate of all accessory occupancies involved.
For example, if a factory has a lunch room (assembly) and offices (business), and the sum of the assembly and business occupancies exceed 10 percent of the total floor area, the code will not allow both to be considered accessory to the factory. Given these circumstances, it is most advantageous to consider the assembly occupancy as the accessory occupancy, which is then pulled from the equation and is no longer a restricting factor of the maximum allowable building area.
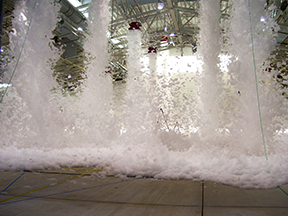
Having only the factory and business occupancies left offers a larger total building area and may give the option of calling the building a ‘mixed-use, non-separated, factory/business occupancy.’ This classification not only eliminates the fire-resistive construction around the lunch room, but around the office area as well. It is important to remember both of these options do not eliminate the need to apply the more stringent egress requirements—howev
er, they do help reduce the need for walls with fire-resistive construction, in addition to any Underwriters Laboratories (UL)-listed opening protection at building system penetrations.
When considering other areas to simplify building maintenance, implementing smoke barriers and sprinkler systems only when absolutely necessary present two opportunities to do just that. It is not uncommon to see smoke barriers provided where not required. Smoke barriers are only required in a limited number of conditions:
- creating smoke compartments in underground buildings, in Group I-3 and I-2 buildings, and ambulatory care buildings;
- some elevator lobbies; and
- for areas of refuge.
Although sprinklers provide distinct advantages, such as eliminating fire-rated corridors and removing fire ratings around incidental rooms (e.g. furnace, boiler, an
d laundry rooms), they are often not required in smaller buildings. Consequently, a quick cost-benefit analysis should be done to determine whether adding a sprinkler system is the most advantageous approach for the facility in question.
It is important to note, however, that when removing fire barriers around incidental areas with the sprinkler system exception, smoke partitions are still required. Utilizing smoke partitions rather than fire barriers in these instances is often a more economical approach. Smoke partitions are only obligated to limit the passage of smoke (not restrict it) and, therefore, have more relaxed construction requirements.
Utilizing fire-resistive construction
While subtracting fire systems such as sprinklers can help increase project savings, adding fire-resistive construction can also yield the same outcome. For example, if the building has a hazardous area that is increasing the water demand for the sprinkler system, it may be beneficial to enclose this single room in fire-resistive construction equal to the duration of the demand, allowing the sprinkler designer to use the room design method to reduce the fire-water demand for the building. Sometimes, these hazardous areas can drive the need for a costly fire pump, but adding fire-rated construction eliminates that necessity.
Fire-resistive construction can also be used to divide hazardous materials (e.g. flammable or combustible liquids) into several control areas, which keeps them under the maximum allowable quantities and prevents having to classify any portion of the building as a ‘hazardous occupancy.’ Once a building is classified as such, other systems such as sprinklers, fire alarm, and additional or limiting restrictions on egress routes are required. By subdividing the hazardous areas into individual control areas, the building can remain under the limitations of the primary occupancy.
While many buildings require fire resistance to be added, some may already have that feature inherently built in, negating the need to strategically classify areas. For example, if occupancy separation is required between floors, one should consider checking the second floor slab construction on the underside of a deck before specifying fireproofing spray to gain the required fire-rated separation. This is because the deck’s 76 to 102-mm (3 to 4-in.) concrete floor may inherently provide the required fire resistance. Concrete systems using composite metal deck will require protection of the steel, since the steel deck provides some of the structural support. A steel form deck (non-composite deck) may not require protection if the concrete is thick enough, since the metal deck is not a structural component of the floor system and is there only to support the concrete while it cures. It is also important to ensure the primary and secondary supporting structural members are also protected.
Design for low-maintenance costs
There are several fire protection practices that have lived on due to inertia. Some are simply overlooked, while others still are mislabeled or mishandled, causing unneeded stress and headaches. For a project to run smoothly, it is important to address these issues head-on and ensure they are done right the first time. Better yet, these practices should be designed from the get-go.
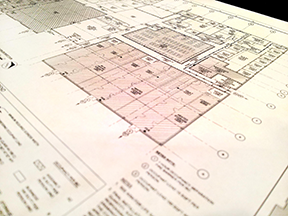
One of the most common mistakes in fire protection is adding smoke detectors to areas where codes do not require them. Break rooms, corridors, electrical rooms, and server rooms—these are all common locations for non-required smoke detectors. An overabundance of smoke detectors is not only found in these rooms, however. Duct smoke detectors are often provided in air-handling systems that do not require them, or on both the supply and return when only one is required. An added benefit of installing only code-required smoke detectors is a reduction in the number of nuisance alarms.
Additional smoke detectors are a relatively minor problem compared to the potential long-term maintenance issues presented by mismanaging sprinkler drains and test connections, which are notorious for creating problems in a fire protection system. Since the rusty water discharge can stain sidewalks, erode the landscape, or create icy conditions on walking surfaces, it is important to ensure the water is discharged to a safe area. Although this not always the most convenient or aesthetically pleasing choice, it can prevent future headaches or safety issues.
Commissioning is another commonly overlooked aspect of fire protection systems. Although acceptance testing is the bare minimum when it comes to commissioning, it is normal for a building owner to receive the acceptance testing certificate and then assume the building system is good to go.
In addition to the acceptance testing, one should consider employing third-party commissioning, which ensures each device is physically tested in accordance with the requirements of the applicable codes and standards. This process may include testing every sprinkler system valve and alarm device, verifying operation of all detectors and correct reporting to the fire alarm system, and validating the integrity of all the fire alarm circuits.
Commissioning also confirms the correct materials were installed in accordance with the approved drawings—not just the code minimum—and looks at field conditions that may not have been apparent during shop drawing review. Most importantly, third-party commissioning agents ensure there are no surprises during acceptance testing, allowing the owner to occupy the building without delays.
Mislabeled systems create headaches for building owners. Fire alarm, fire suppression, and passive fire protection systems are often not labeled at all, increasing the time it takes to test and troubleshoot problems. Additionally, specifying minimum clearances around and in front of valving and other equipment ensures adequate clearances are provided for performance-based systems such as sprinklers. Taking the time to coordinate these items and clarifying them in the specifications can also reduce maintenance down the line.
Taking a holistic approach
The importance of a fully coordinated building fire protection system is often overlooked because of the multi-disciplinary nature of fire protection. As a result, building fire protection is frequently not addressed in a holistic manner that looks for opportunities to decrease expenses or increase the long-term durability of the building.
One should begin his or her next project using an all-inclusive approach, and finish it off with a thorough commissioning effort to make for a successful, fully code-compliant building.
Tony Schoenecker, PE, is a senior fire protection engineer with Burns & McDonnell in their Minneapolis-St. Paul office. For the past 18 years, Tony he been involved in projects for medical, education, government, military, institutional, commercial, utility, and industrial clients. As a fire protection engineer his experience includes fire suppression, fire alarm, mass notification, life safety and building code analysis, smoke management, passive and active fire protection assemblies, deflagration venting and mitigation, smoke and egress modeling, and hazard analysis. Schoenecker can be reached at aschoenecker@burnsmcd.com
Fire Sprinkler system is the way to go
It’s interesting that people respond more quickly to voice instructions during an emergency. I would think that a simple alarm would do the job to get people moving really fast. However, I can definitely see how, during an emergency, people might need actual direction to avoid panic.
I’ve always wondered what different fire suppression systems there were. It seems like there are quire a few options! It makes sense that industrial areas would need bigger systems, considering their size and the higher effect of flames. It seems like a high-expansion foam system would be a good idea for an industrial area.