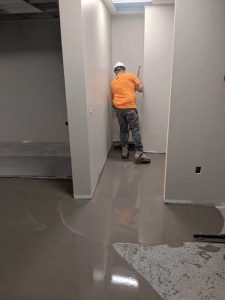
In-situ probes measure the moisture content within the concrete matrix, whereas calcium chloride tests only the surface of the slab. Each probe or sensor requires a hole measuring 19.05 mm (0.75 in.) in diameter and at a depth equaling 40 percent of the slab’s thickness for slabs drying from one side, or 20 percent depth for a slab drying from two sides. The probes can also stay in place for weeks at a time to determine if there is a change in moisture levels. When testing, it is also crucial for installers to consult floor covering product manufacturers, since surface preparation requirements and methods vary depending on the specified type of substrate, subfloor, underlayment, and floor covering.
For example, when applying floor finishes over concrete substrates, some floor coverings require a light grind or shot blast to a specific concrete surface profile while others require a more aggressive mechanical surface preparation in order to achieve a tenacious bond. Slab moisture conditions such as RH, MVER, and the level of alkalinity (pH) also require consideration. In addition to ASTM F1869-16a and F2170-19a, ASTM F710-19e1 covers the determination of the acceptability of a concrete subfloor for the installation of resilient flooring, thereby ensuring resolution of concerns with substrate profiling and potential bond breakage. This assures conditions are acceptable for the installation of the resilient flooring in a timely manner.
Despite the general adoption of these testing methods, there remains an alarming number of flooring failures. From hospitals to office buildings, hotels to university campuses, fast-track construction, tight budgets, and a lack of awareness of these testing standards have resulted in $2.4 billion in annual expenditures in the U.S. to remediate moisture and repair or replace damaged flooring, according to data from Independent Floor Testing & Inspection.
Barriers to proper prep and testing
Perceived costs and timeline restrictions are, unsurprisingly, major barriers to proper moisture testing and mitigation. General contractors may bid a project at one price and then negotiate lower costs with subcontractors once they secure the project. Additionally, since material science education is not a common practice in the industry, there can also be a lack of material literacy among contractors and subcontractors. If contractors feel no need to prepare the floor, they will simply not pay subcontractors to do it.
“Flooring contractors can feel pressured by general contractors to install a floor without proper flooring prep and moisture testing,” said Steve Poniatowski, vice-president of sales at ReSource New Jersey. “If they’re green and not experienced enough to stand up for themselves, they will likely cave to the pressure. However, this can come back to bite them and literally put them out of business if flooring failures add up.”
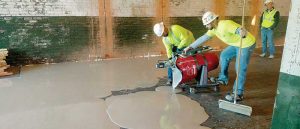
Another barrier is the increasing use of power troweling by concrete contractors. Power trowelers allow concrete professionals to install and finish large swaths of flooring in a short period of time. This helps them stay on schedule and within budget in a world of ever-tightening construction deadlines. While the finished floor looks fine and is moisture-free at the surface, power trowel machines create a non-porous finish which locks moisture deep within the slab. Moisture will eventually make its way to the surface, and if resilient flooring is installed on top, it will fail months or years down the road. Power trowelers also create a surface that floorcovering materials have difficulty bonding to.