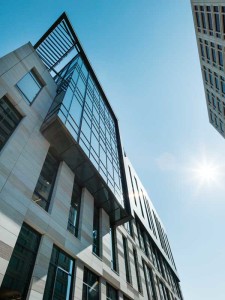
by Chris Bovee
When it comes to a leak-free building, the sealants are the backbone of the whole cladding system. Even the best exterior aluminum, masonry, glass, steel, or exterior insulation and finish systems (EIFS) are only as good as the sealants used to weatherproof the joints, penetrations, and transitions of the cladding system being specified.
Silicone has been used to seal building interiors and exteriors for close to a century because silicone sealants are ultraviolet (UV)-resistant and have an operational temperature range of −50 to 150 C (−60 to 300 F). However, construction specifiers have been turning to precured silicone seals for the past few decades because a precured sealant system can handle at least 100 percent more expansion and at least 25 percent more compression movement than traditional ‘liquid-applied’ elastomeric silicone sealants. (This comes based on a comparison of product data sheets from three liquid-applied sealant manufacturers with a validation certificate of a precured sealant on the Sealant, Waterproofing, and Restoration Institute (SWRI) website).
To oversimplify, a cladding system is the building’s outer rain gear, and sealants are like the zippers, cuffs, and drawstrings pulling the whole thing together. Precured seals either replace or work in conjunction with more traditional liquid-applied, elastomeric sealant or mechanically fastened weatherproofing systems to keep water out and heating and cooling in.
Not only are preformed sealants used to waterproof the exterior of a cladding system, but they are also available in a translucent form (extruded strips and molded corner pieces) that provide continuous transition and bridging to air and vapor materials behind the cladding—similar to another layer of waterproof clothing underneath the rain gear.
Possibilities with precured sealant
To fully appreciate the different applications of precured sealants with various claddings, one requires a basic understanding of the material’s features and benefits. Precured sealants start out as 208-L (55-gal) drums of silicone similar to the caulk found in tubes, without the curing agents. However, this sealant gets color and fast-curing ingredients mixed in; it is then extruded through a die, that was cut to exact specifications, allowing a continuous, consistent strip to feed through a long water trough. The result is a uniform, stretchable strip free of bubbles, voids, or any of the weak spots occurring when liquid or tape sealant is applied by hand or tooled into place onsite.
By the time the sealant reaches the end of the trough in the factory, it is fully cured and typically spooled onto rolls 15 to 45 m (50 to 150 ft) long. The precured seal is then boxed up and delivered along with a case of its manufacturer’s specially formulated high-performance, neutral-cure silicone adhesive.
At the jobsite, the seal is rolled out, separated from a packing backer, and cut to length with a utility knife or scissors. There is no need for special splice kits, as ends are just lapped and sealed. (Silicone sticks to silicone; manufacturers should have a list of tested silicone sealants where the adhesion has been tested with precured extrusions.)
Only a thin bead of silicone bonding adhesive underneath the outer edges of the precured seal is needed to set the sealant system into place, and keep water and weather out for the long haul. To finish the process, one simply presses the seal into the adhesive bonding bead (i.e. silicone sealant for which adhesion has been tested) with a block of wood or a finger. Since there are no mechanical fasteners, holes do not need to be made in the roof, wall, or building transition being sealed up against the elements.
![Pressing-Pre-cured-Sealant-Into-Place[1]](http://www.constructionspecifier.com/wp-content/uploads/2016/03/Pressing-Pre-cured-Sealant-Into-Place1-e1457472508938-300x182.jpg)
Instead of waiting days (or even weeks) for thick liquid-applied sealants to cure, the thin bead of adhesive underneath the precured seal sets within a few hours under most weather conditions. The fast curing time of the silicone bonding adhesive means the seal installed in the morning will be set up to handle the expansion occurring with the heat of the afternoon and the contraction of the cool night.
This is vital to a good seal because many liquid sealant failures occur—even if they do not appear as leaks until years later—during the multiple cycles of expansion and contraction that happen during the curing period. With liquid sealants, a new or repaired joint can take days or weeks to fully cure; this can lead to loss of adhesion (i.e. tears or voids between sealant and substrate) and cohesive failure (i.e. tears or voids within the sealant bead).
By contrast, the precured sealant is able to withstand joint movement of +200 percent expansion and −75 percent contraction. Liquid-applied sealants range from +50 to 100 percent expansion and −50 percent contraction, depending on brand and formula. When choosing between liquid-applied and pre-cured sealant, the main consideration, just in terms of material costs, is the width of the expansion joint. A wider joint requiring lots of liquid-applied sealant may cost as much or more than a precured seal—the reason why the latter is mostly employed for niche applications in new construction.
How precured and liquid-applied sealants compare with respect to service life depends on the application and the chemistry. If both materials are silicone, then the only difference is the application. Due to the way which precured sealants are installed, there is a neutral area that is not bonded. This is a similar effect as utilizing bond-breaker tape and tooling sealant over an undersized joint.
When comparing typical expansion joints, precured sealants impose little to no stress on the substrate during a compression cycle. Certain substrates can be damaged from these forces, allowing water penetration during the expansion cycle. If a joint is properly designed and installed, the service life is probably the same. When the joints are improperly designed or installed, precured sealants could outlast their liquid-applied counterparts.
I didn’t realize how imporant sealants could be. I would imagine that proper application is cruecial. I’ve heard that most people who apply it without professional help actually do it wrong. Is that true?