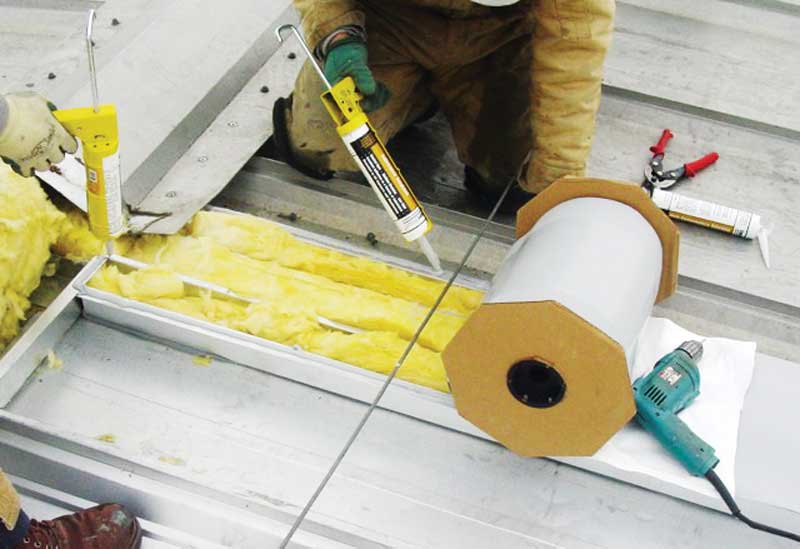
Exterior insulation and finish systems
Using precured seals with EIFS panels that have stucco or other-textured finish coats can have important dividends. Roy Conrad, a project manager with Gorman Moisture Protection Inc. of El Paso, Texas, has been using precured seals for about 30 years. (Gorman Moisture Protection is a regular presenter at the events held by SWRI, which offers results of long-term studies on how various sealants age in the field—real world versus manufacturer claims. Visit www.swrionline.org for more information). It is currently in the process of installing up to 518 m (1700 lineal ft) of precured seals on the $648-million Fort Bliss Replacement Hospital. Gorman is the subcontractor to general contractor Clark McCarthy, and the client is the United States Army Corps of Engineers (USACE)–Fort Worth District.
“We are technicians and our primary focus is on doing it right the first time,” Conrad says. “The physical consistency of precured seals is such that there is low bond-line stress on the substrate.”
Other liquid-applied, elastomeric sealant systems can generate higher bond-line stress on EIFS walls because of the thickness of the hourglass bead needed to bridge the joint. For a typical 19-mm (3⁄4-in.) wide expansion or perimeter joint, the sealant bead thickness ranges from about 5 to 13 mm (3⁄16 to 1⁄2 in.), whereas the precured seal is only 2 mm (1⁄16 in.) thick across the entire joint. The thicker the sealant, the less it can expand and contract with temperature and load changes. (This is akin to stretching a rubber band versus trying to stretch a rubber tire.)
If too much bond-line stress is exerted on the thin stucco finish coat of an EIFS panel, then the substrate is likely to crack and the seal is likely to fail. As mentioned, the precured seals, by contrast, can withstand movement of +200 percent expansion to −75 percent compression because they are thinner. They also offer customization potential, with notched profiles for bending and wrapping around edges and other difficult-to-seal details.
Masonry and stucco
Precured seals work well with masonry and stucco applications because of the aforementioned low bond-line stress. The thin bead of silicone adhesive used underneath the outer edges of the precured seals forms a chemical bond with the substrate.
Like their liquid-applied counterparts, precured sealants have the ability to match color and texture. A matte surface is the standard profile for most precured seals, but special surface texturing and custom color can be added to match almost any masonry or stucco substrate.
The molecular structure and high-bond energy of silicone is resistant to UV light and weathering, which means the colors selected for the project will resist fading for decades, just as with any quality liquid-applied silicone sealant. Precured or liquid-applied sealants that are polyurethane-, polysulfide-, or butyl-based tend to not have as effective UV and weathering resistance properties, however.
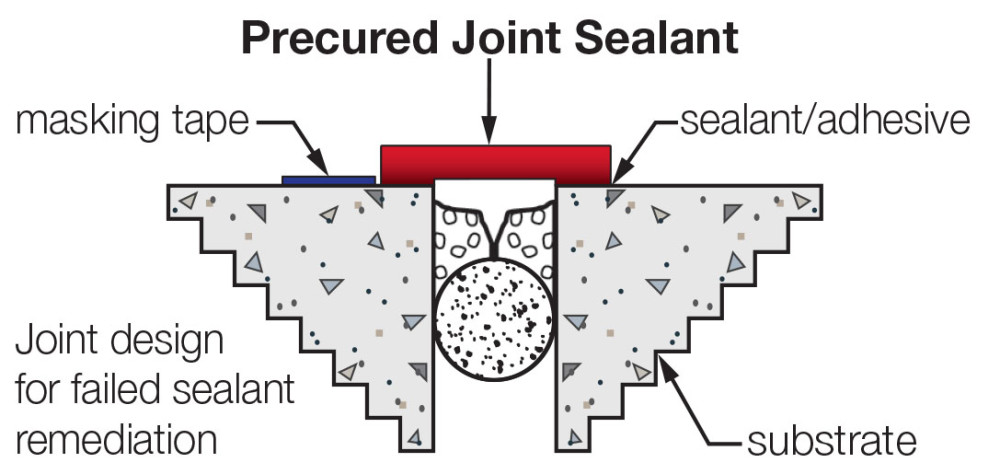
Metal building
Precured silicone sealants are primarily used on metal buildings to help keep weather out of hard-to-seal areas of both roof and cladding systems:
- roof-to-wall transitions;
- roof height change details;
- roof curb seals;
- ridge applications;
- vertical and horizontal expansion joints;
- joints between new buildings and existing buildings;
- pipe and other penetrations; and
- repairs.
Span Construction (Madera, California) is building about 90 Costco warehouses around the world. Its crews use precured seals for a vital detail on its projects—rain gutter joints. Warehouse manager Jerry Christian says these gutters are basically big troughs capable of holding a lot of water pouring off the roofs. His crews use 3.1-m (10-ft) long lengths of 76-mm (3-in.) wide, precured silicone sealant to seal up the gutter joints.
Span has been employing precured seals for about four years because of the material’s ability to handle a wide range of multi-directional expansion and contraction. The precured seals also eliminate the need to put additional holes into the gutters because no mechanical fasteners are needed to hold the seals in place.
Precured seals are a suitable solution for many specialty applications, but they are often just one component of the sealant system specified on a building project. Brushed-on or rolled-on elastomeric liquid-applied sealant may be more a cost-effective option for whole-roof coatings, for example, due to basic per-area material prices. Further, some highly contoured, detail applications may be better-suited to sealant systems that use mechanical fasteners to hold membranes in place while the bonding adhesive cures. A precured seal should lay flat on the bonding adhesive for at least an hour for the chemical bond to set up sufficiently. More detailed applications with contours and edge wrapping may require weights or clamps to hold the pre-cured seal in place during initial curing.
I didn’t realize how imporant sealants could be. I would imagine that proper application is cruecial. I’ve heard that most people who apply it without professional help actually do it wrong. Is that true?