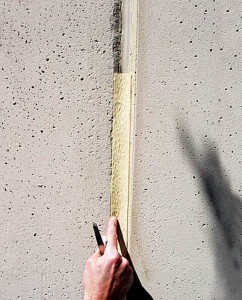
Glass, aluminum, and steel
When it comes to new office buildings, high rises, and modern structures with glass and aluminum or steel cladding, the most common application for precured silicone sealants are: expansion joints and window weatherproofing.
Expansion joints
Precured seals provide some additional advantages over traditional expansion-joint sealants. Greater movement capability, faster cure times, higher tear resistance, wider operational temperature range, and ease of installation are just a few of the factors spurring engineers and architects to consider specifying precured seals instead of the traditional closed-cell-foam backer and tooled-on, liquid-applied silicone sealant systems.
Precured silicone sealant virtually eliminates the need for the traditional hour-glass-shaped bead of caulk with foam backer system that has been in use for more than a half-century. Precured seals come in standard widths of 25 to 300 mm (1 to 12 in.), so they can be used across a wide array of expansion joint configurations, such as:
- traditional bridge joints;
- recessed bridge joints;
- concave bridge joints;
- recessed concave bridge joints; and
- U-joints.
Windows
Precured silicone seals are predominantly used to repair failed liquid-applied structural glazing systems. In terms of cost and aesthetics, precured seals save time and money in situations where the old, failed structural glazing would have to be removed by hand in order to re-glaze the mullion-to-glass or glass-to-perimeter transition. This kind of labor-intensive repair also poses a risk of damaging the glass or mullion.
With precured sealant, however, the contractor can install the new seal right over the top of the failed structural glazing without having to scrape and dig out the old material. The profile of each strip of precured sealant can be customized with notches to form easy-to-install, weathertight covers for mullions and window transitions.
Generally speaking, time and labor costs are very job-specific. Some applications require much more work than others in order to prepare an expansion joint/seal prior to re-applying a wet-applied sealant. The labor saved from not removing the old/failed sealant and surface preparation is the reason there is a market for this technology.
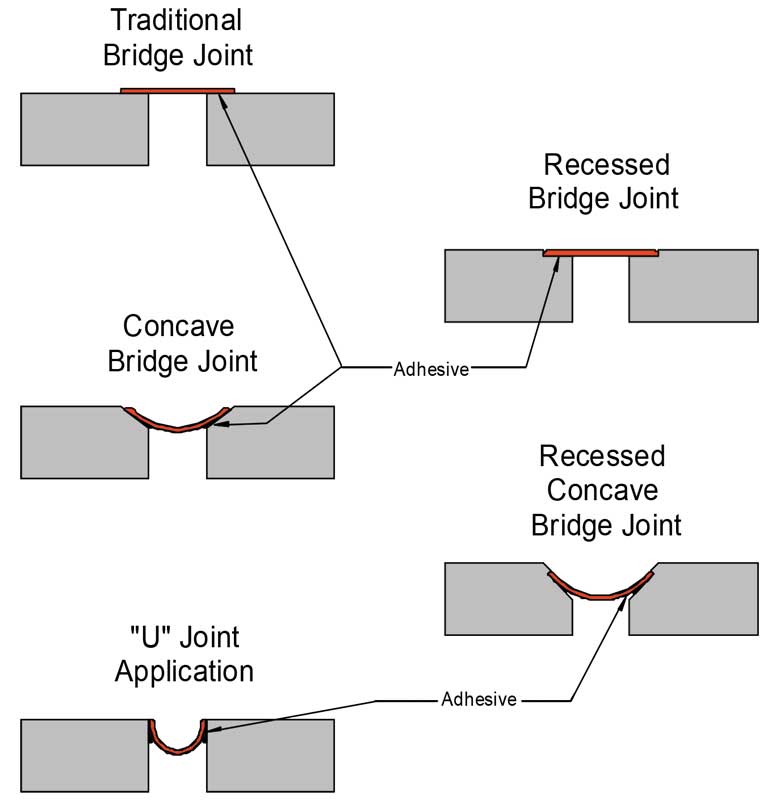
Building remediation and retrofitting
By far, the most common use of precured silicone sealant is for remediation. Conrad uses precured seals to bridge over joints where there is a risk of damage to the substrate.
“The ability to leave existing failed seals in place” is a key advantage, he says.
While basic preparation work is still required to create a clean, dry surface for the precured seal’s bonding adhesive, the crew does not have to remove the old sealant—and risk damage to the joint and substrate—before installing the precured seal. This is especially true with EIFS, where the exterior stucco-like coating is thin and easily damaged when contractors try to remove old liquid-applied sealants.
The precured sealant is installed with a silicone sealant or adhesive, bonded to the substrate on either side of the failed expansion joint or seal. The preparation required depends on the surface on which it is being installed—ultimately, it needs to be clean, dry, and frost-free. Precured joints are wider than the original joints, with the extent depending on the width of the material being installed and the installer. For smaller extrusions, it might be 9.5 mm (3⁄8 in.), or as much as 25 mm (1 in.).
For new construction, its appearance can be viewed as a negative by architects desiring recessed or flush seals, but most applications are very large multistory buildings—in other words, seals on the third floor and beyond tend to be only visible to the window cleaners. Further, there are engineering/architectural ways of using precured extrusions with a flush seal.
During building remediation, owners try to get the most out of their building with as little disruption to their tenants and as low a cost as possible. This is where precured joints fit in.
Continuous air and vapor transitions
To return to this article’s original metaphor, these aforementioned applications are the outer rain gear of the cladding system, but the use of translucent extruded silicone strips along with molded silicone pieces for curtain-wall transitions is a bit more like a good pair of long underwear underneath. Not only does a continuous air and vapor transition system provide another layer of protection against water infiltration, it can also be considered a part of a ‘green’ energy-efficient design that creates a leak-free air barrier.
The translucent feature of preformed transition strips and pieces allows inspectors to easily see and verify the bonding adhesive forms a continuous seal. Preformed transition strips and pieces are used to seal transitions in curtain wall, façade, punched windows, and storefront cladding systems. Molded transition pieces are available for inside and outside corners and can be installed in-shop or in the field.
Preformed transition strips and corner pieces can help contribute to successful Leadership in Energy & Environmental Design (LEED) certification, ranging from low-volatile-organic-compound (VOC) material use to thermal comfort. According to U.S. Department of Energy (DOE) EnergyStar estimates, up to 30 percent of the costs of heating and cooling a building are wasted due to building-envelope air leaks. Preformed silicone transition strips and molded pieces can be used to considerably reduce that waste.(Visit www.energystar.gov/buildings/facility-owners-and-managers/existing-buildings/save-energy).
For building remediation projects, it is important to remember how far the technology has come. One of the first large projects where precured extrusions were installed, the workers started on the top floor and progressed toward the bottom. By the time they got within three floors from the bottom, there was so much air coming out of the original failed joints that the extrusion was blowing off the building before the adhesive sealant could cure. They had to drastically reduce the HVAC make-up air in order to complete the installation. The old solution was to pressurize the building to prevent water infiltration.
Conclusion
No matter what type of cladding specified for a project, precured silicon sealant can play a vital role in keeping outside weather out and indoor climate in. The material’s use continues to grow throughout the construction industry. Its large potential for marine, transportation, and other construction-related applications has barely been tapped, from certain residential uses to window manufacturing applications.
Chris Bovee is vice president of Sealex Inc., a manufacturer and developer of precured sealant technology. He holds degrees from Ferris State University in both plastics and rubber engineering. Bovee can be reached at chrisbovee@sealexinc.com.
I didn’t realize how imporant sealants could be. I would imagine that proper application is cruecial. I’ve heard that most people who apply it without professional help actually do it wrong. Is that true?