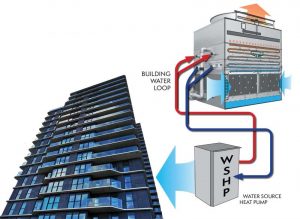
This example shows a cooling tower system installed at high-rise condominiums using WSHPs. While installing a heat exchanger achieves the intended purpose of isolating the chiller or heat pumps from the cooling tower, its addition comes with some deficiencies, such as:
- Tight spaces between the plates increases the risk
of fouling. - High pressure drops due to the restricted flow path between the plates.
- Heat exchanger approach lowers the system’s heat transfer efficiency.
In this type of system, the water sent to the WSHP 31 C (88 F) from the heat exchanger will be hotter than the tower supply water 29 C (85 F) due to the approach across the heat exchanger. Consequently, the cooling tower must be oversized to maintain WSHP efficiency levels achieved in a system that lacks a heat exchanger.
Closed circuit fluid cooler
Figure 3 illustrates the use of a closed-circuit cooler paired with WSHPs, though this design would work just as well in a chiller application.
The fluid cooler contains a heat transfer coil bundle(s) which shelters the process fluid inside from environmental impurities. In effect, the heat exchanger has been moved inside the evaporative unit—this provides the advantages of the heat exchanger without its inherent disadvantages.
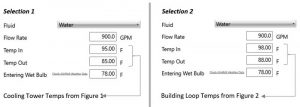
The building water loop in Figure 3 is now supplying 31 C (88 F) water directly from the cooler to the WSHP. One will notice the supply water temperature coming from the cooler is -16 C (3 F) higher. This is acceptable because there is no efficiency loss across a plate-and-frame heat exchanger.
One should not simply use the same design conditions to compare a tower/heat exchanger to a cooler. Looking at the impact on the size and cost of the cooler to see if correct temperatures are excluded from the analysis, Table 1 and 2 demonstrate the operating parameters the engineer will need to make a standard closed-circuit cooler selection.
Notice the differences between fluid cooler one versus fluid cooler two:
- 36 percent bigger
- 31 percent heavier
- 25 percent higher in total connected heat pumps
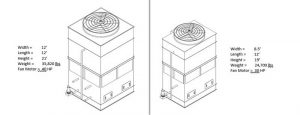
Real-world examples
Following the key differences, downfalls, and advantages of cooling towers and fluid coolers, and delving into several examples of how fluid coolers have been applied to real-world projects across the country, and the specific design considerations that led engineers to specify fluid coolers over cooling towers.
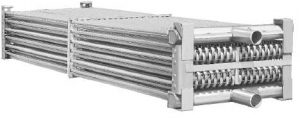
Hybrid fluid coolers lower data center operating costs
Hybrid fluid coolers are closed-circuit coolers that can operate with the spray pump off and with only the fan running. While these units look similar to traditional fluid coolers, they have the enormous advantage of being able to operate without the use of water. The coil sits in the air stream so dry capacity can be provided simply from air passing over the coil. They are most often specified when water savings and efficiency are of utmost importance, or when cooling capacity is still needed within a facility when outdoor temperatures are low enough to present the risk of freezing.