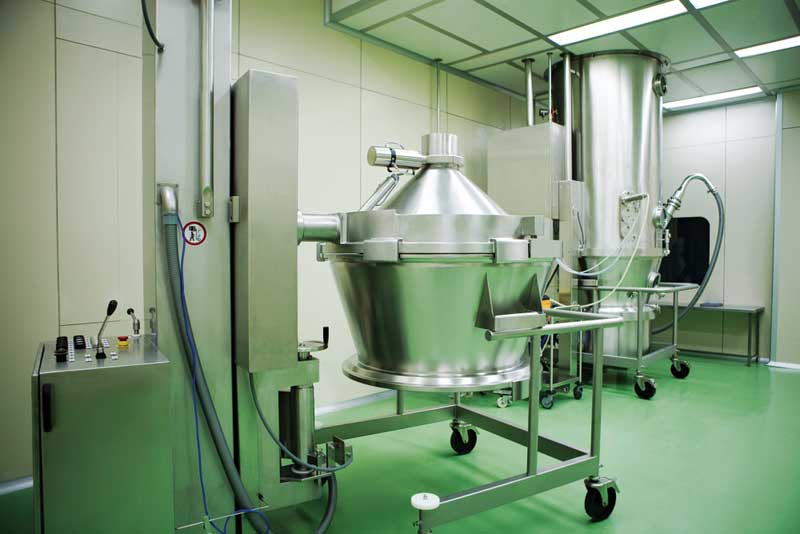
Minimizing operational downtime
Downtime is the scourge of any operation, as it can lead to increased costs, production delays, and lost revenue. However, ‘down’ need not mean ‘out’ with flooring installations. Specifiers have the capability to help contractors and building owners realize faster return-to-service times via their product recommendations.
Installing or repairing a resinous floor requires downtime interfering with the productivity of other operations. Flooring systems go down wet, which means other trades and/or facility personnel will need to stop work and avoid the area to prevent contamination. They will not be able to re-enter until the applied flooring dries sufficiently to handle foot traffic—they may have to wait even longer (typically twice or threefold as long) for it to cure adequately to support equipment traffic.
Available flooring systems include a wide array of technologies featuring varying levels of application efficiencies, curing times, durability, repairability, and other characteristics. (See “Getting to Know Resinous Flooring,” for a rundown of common choices and their respective properties.)
Based on the desire to reduce downtime, some design professionals assume it
is critical to simply specify a flooring system with the fastest installation and curing times. However, the real best bet is to find a balance of desired properties related to the project requirements.
For example, if one only has a four-hour shutdown to complete an installation, a methyl methacrylate (MMA) floor may be the sole suitable choice. However, MMAs can present flammability and odor concerns. If a buffer of even a few extra hours is available for the installation, specifying a polyaspartic (PAE) floor could be a better fit, as it trades some of the speed of an MMA for greatly reduced odors. When there is an opportunity for an even longer installation window, the product choices open up to include dozens of options, each with its own property tradeoffs related to speed, cost, and durability.
Waiting out concrete-curing times
Potential downtime associated with flooring installations actually begins the moment contractors finish pouring the concrete substrate. The concrete needs to cure at least 28 days before most flooring types can be installed—the moisture vapor content must drop to acceptable limits for proper adhesion. Other facility work can take place in the interim, but crews cannot apply flooring products like a traditional epoxy system until at least four weeks after the concrete pour.
During this wait, other work, such as the placement of equipment and floor cabinetry, may reach a stopping point until crews can install the floor. However, specifiers can accelerate the entire process by recommending a floor allowing for application over ‘green’ concrete. For example, urethane concrete floors are highly tolerant to moisture, which allows crews to apply them over fresh concrete in as little as three to five days following the pour. This option would allow installers to apply urethane concrete at least 23 days sooner than a traditional epoxy, which could greatly speed up construction timelines and reduce downtime.
Accelerating project schedules can be especially important when renovating facilities. For example, if a renovation calls for adding a new electrical trench, the relatively small area of new concrete poured to cover the trench could cause a month’s delay before crews are able to install the flooring system. Using a moisture-tolerant floor would cut that time down to days, allowing the renovated area to return to service much sooner.
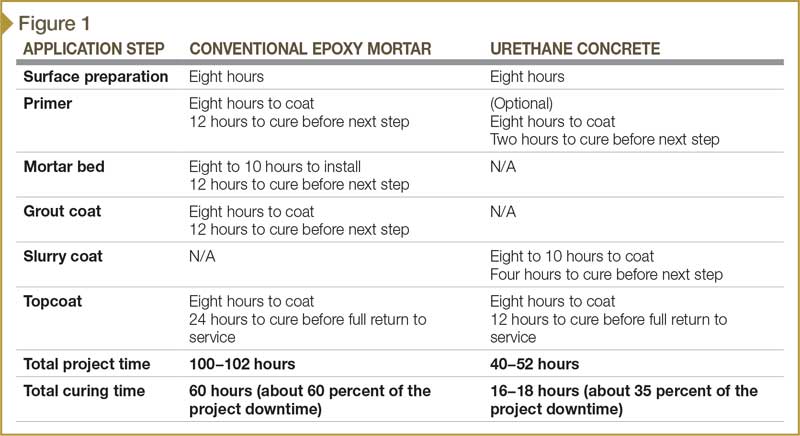
Accelerating flooring curing times
The steps required to apply a flooring system depend on the amount of coating layers needed before topcoating. While this number certainly has some bearing on project length, the curing times associated with each layer have the greatest influence. If a particular layer cures rapidly (e.g. a primer taking two hours), the contractor may be able to apply the next layer the same day. This efficiency could mean the difference between a crew completing the whole project in one or two visits and needing to return to the site multiple times.
To enable more efficient installations, specifiers can recommend flooring options that have faster cures for each applied layer. The installation of epoxy mortar versus urethane concrete for a 930-m2 (10,000-sf) facility using a five- to seven-member crew provides an example. Figure 1 details the full installation times of epoxy mortar (more than 100 hours) and urethane concrete (52 hours when using the optional primer).
The epoxy mortar floor requires one additional step that adds to the project length, but the curing times represent the greatest time sinks. Calculating the curing times shows a difference of 42 hours between the systems and a major disparity in their contributions to project downtime—60 hours of curing time (or about 60 percent of the project downtime) for the epoxy mortar and 18 hours (or about 35 percent of the downtime) for the urethane concrete. Further, urethane concrete allows full service within six to 12 hours of topcoating, compared to 24 hours for epoxy mortar, allowing the facility to resume operations at least a half-day sooner.