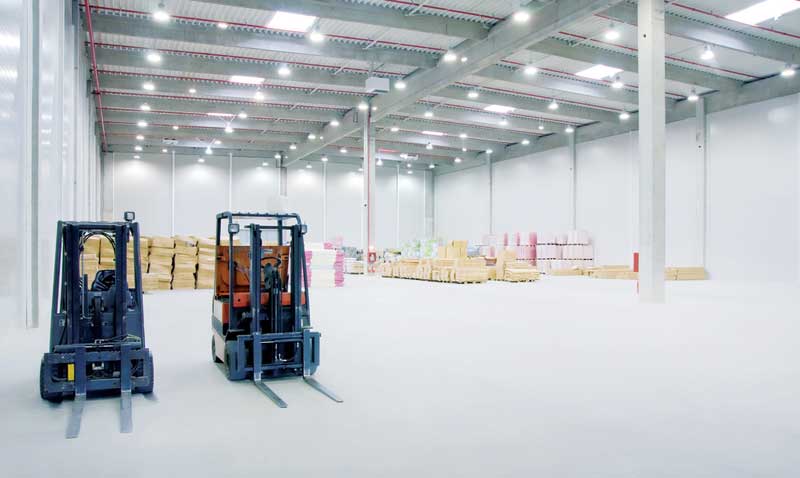
Promoting longevity to reduce costs
A specifier can have the greatest impact on reducing the hidden costs of a flooring system by selecting products that offer long life cycles. That means specifying materials with high resistance to moisture, abrasions, thermal shock, chemicals, and additional factors relevant to the application. A system’s long-term durability, along with its ease of repair, reduces maintenance needs and delays complete flooring replacements.
Of course, specifiers must still balance property tradeoffs (e.g. swapping long-term durability for installation ease) as they consider project time constraints and life-cycle costs. For example, specifying a floor with a faster upfront installation but lower durability, such as a thin-mil system, could mean replacement every five years, which raises life-cycle costs. When a 3.2-mm (1/8-in.) system is called for, it may be more expensive upfront, but it might only require a topcoat every five to 10 years. This would be far more cost-effective over time.
When weighing product decisions based on durability, specifiers may need to overcome some common misconceptions about product performance data. For example, many specifiers believe the harder the flooring, the greater its abrasion resistance. Therefore, they may specify an epoxy system because it has a Shore D hardness of 90, compared to a urethane coating with a 6H pencil hardness. However, because they are softer, urethane coatings actually have three to five times the abrasion resistance of epoxies.
Compressive, tensile, and flexile strength are other properties that many specifiers misunderstand. For example, a design professional may automatically choose an epoxy system with a compressive strength of 82.74 MPa (12,000 psi) over its 48.26 MPa (7000-psi) urethane concrete counterpart because the bigger number sounds better. However, it is important to remember either system will be applied to a concrete substrate, which has a compressive strength of only about 27.58 MPa (4000 psi). It can actually be advantageous to select the urethane concrete because a system with a compressive strength that is closer to that of concrete is less likely to debond from the concrete when subjected to thermal shock. The urethane concrete’s flexibility allows it to move more uniformly with the concrete as it shifts from temperate cycling due to thermal shock. Since a more rigid epoxy cannot move as easily with the concrete, it would be more prone to delaminating from the concrete substrate.
Specifying a flooring system
The true cost of a floor includes much more than the expense of materials and labor. Specifiers need to consider the downtime associated with all aspects of the project, whether any installation efficiencies are possible, and how long they can expect the flooring to last to determine the complete life-cycle costs of a system. Examining these parameters against various systems could expose several tradeoffs—such as faster installations, but lower durability—that may complicate the selection process. To alleviate confusion, specifiers can work with a specialized flooring provider to sort through potential scenarios associated with an installation, repair, or renovation to arrive at the appropriate product choice. This may help specifiers avoid choosing the least-expensive option upfront when it may have significantly higher life-cycle costs.
RESINOUS FLOORING APPLICATION CONSIDERATIONS |
Specifying a resinous flooring system involves a wide range of considerations. Here are a few application characteristics to keep in mind.
Application to green concrete Removal of existing floors If an existing system needs to be removed, crews have to peel it off and then remove any remaining glues and curing compounds via chemical and/or mechanical means. For example, crews may need to use citric acid to soften and remove glue, and they may need to shot-blast, grind, mill, or even scarify the surface to fully remove the adhesive and get the surface to a smooth finish. In extreme cases, a flooring renovation will require breaking up the concrete base and pouring a new substrate. Controlling cracks Addressing joints Addressing termination points |
Casey Ball is regional market segment director of flooring for Sherwin-Williams Protective & Marine Coatings. He previously served as a project development manager, drawing on his experience as a corrosion specification specialist and a technical service representative for Sherwin-Williams after starting his career as a lab technician at General Polymers. Ball has specialized in the flooring and coatings market for 15 years. He is a NACE-certified coatings inspector, and a Society for Protective Coatings (SSPC)-certified concrete coatings inspector. Ball can be reached via e-mail at casey.a.ball@sherwin.com.