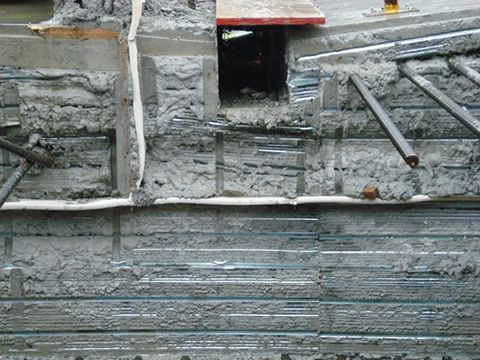
Applications for hydrophilic waterstops are not limited to cast-in-place concrete construction joints. Due to their flexibility and conformability, hydrophilic waterstops can be easily installed around pipe penetrations, I-beams, concrete pilings, and irregular-shaped surfaces. Hydrophilic waterstops are also used to seal new concrete placed against existing concrete. Additionally, they are lightweight and flexible, and do not require any special order prefabricated Ts, Ls, or crosses. The installation efficiency of this type of waterstop makes them a favorite amongst contractors.
For hydrophilic waterstops, manufacturers typically require a minimum 50 to 75 mm (2 to 3 in.) of concrete coverage depth, depending on the profile size and material type. These waterstops must be installed in strict accordance with the manufacturer’s minimum concrete coverage guidelines to eliminate the potential of concrete spalling due to insufficient concrete coverage. They need to be installed without overlapping adjoining strip ends; the strip ends must be tightly abutted to form a continuous system.
Since these products expand in the presence of water, they should not be prematurely wetted. This requires the second concrete placement take place promptly after the waterstop placement; otherwise, the waterstop might expand if exposed to rain. The ‘free water’ in a concrete mix is not enough to physically swell a hydrophilic waterstop. After the concrete has cured, a sufficient external source of water that migrates into the joint and comes in contact with the waterstop is required for it to actually swell. If no external water source comes in contact with the hydrophilic waterstop, it simply remains dormant.
Not all hydrophilic waterstops use bentonite clay as their hydrophilic agent. Hydrophilic rubber waterstops expand upon contact with water and maintain a solid material integrity that will not deteriorate due to uncontrolled expansion. However, since they are produced with different types of hydrophilic agents, they may have different expansive properties (in terms of rate and volume) when exposed to water. Also, some are produced with portions of the profile made of non-swelling rubber—this means the entire profile does not activate and swell.
This class of hydrophilic waterstop has the same limitations as less-expensive bentonite-based waterstop products—namely, the inability to swell in fluids other than water, and the lack of expansion joint functionality.
Special Conditions: Shotcrete |
With pneumatically applied concrete (i.e. shotcrete) foundation wall construction, it is advisable to install a waterstop in all construction joints and whenever possible all lift joints. Typically, the preferred waterstop type is a strip hydrophilic class waterstop, in lieu of a PVC dumbbell, due to the application of the shotcrete. With ribbed center-bulb waterstop profiles, it is difficult to spray and properly consolidate the shotcrete behind the wide waterstop flange. The consolidation can also be affected by any movement (vibration) of the waterstop flange by the force of the shotcrete spray. Today, many waterproofing membrane manufacturers include their own branded waterstops as part of their overall waterproofing system. Therefore, for waterproofing warranty eligibility and issuance, the manufacturers require the use of their waterstops. |
In-situ performance of hydrophilics
Hydrophilic waterstops are effective in providing protection against water infiltration through concrete construction joints, including those under high-pressure and intermittent hydrostatic conditions. Due to their product design, hydrophilic waterstops exhibit a high degree of expansion when hydrated in a non-confined, free-swell condition, such as in
a bowl of water.
In a non-confined condition, the product may exhibit some fracturing as it approaches maximum expansion. Although this may appear to be a negative aspect of the material, the fracturing is an indicator of positive performance for in-situ concrete joint conditions. It means the waterstop compound expands and easily conforms to the interior surfaces surrounding it within a concrete joint, no matter how irregular.
Further, the plasticity and expansion properties provide it the ability to extrude into cracks and advance around angle transitions that may be present in the joint. Bentonite compounded strips have been observed expanding through narrow cracks to fill larger void areas beyond the poorly consolidated concrete interface with the waterstop strip.
This dynamic sealing ability is possible because of the expansive properties; the same capabilities would be impossible with a high-tensile-strength material such as a hydrophilic rubber waterstop. It has been observed through lab testing that hydrophilic rubber waterstops have limited expansion into cracks, gaps, and joints that surround them due to their more rigid material properties. The hardness of the rubber may allow the waterstop to expand only a swallow convex amount across the opening of the crack and not extrude into its depth.
The maximum expansion a hydrophilic material exhibits in non-confined, free-swell conditions will not materialize in properly consolidated concrete. In-situ, hydrophilic waterstops only have to expand slightly to form the positive seal against the concrete interface around it. This limited swell affords the product a ‘reserve swell potential’ to seal poorly consolidated concrete or for concrete cracking that may occur later during building settlement or seismic activity.
Once hydrated, hydrophilic waterstops rarely undergo wet-dry cycling. When confined in concrete and below-grade, the material maintains its hydrated equilibrium and does not shrink during typical water-table fluctuations or intermittent water conditions. Interestingly, bentonite can be hydrated and dried an infinite number of times without losing its original, natural swelling capacity. Similarity it can be frozen and thawed repeatedly without losing swell performance. Finally, even if in-situ drying were to occur (an extremely remote possibility), bentonite has been proven to rehydrate to its original level of performance.
One question. When overlapping the water stop. What is the minimum overlap?
the ends should not be lapped, the ends should be welded together.
I thought that too but I’m not sure how that’d be accomplished…. Can you elaborate on this detail please….. Thanks in advance
You have to use a Splicing Iron (most waterstop manufacturers discuss splicing irons in their installation guides and other product information sheets).
is splicing iron possible to connect two waterstops with different material?
WHAT IF THE WATER STOP IS ALREADY ATTACHED TO THE CONCRETE AND DUE TO DELAYED WORKS IT IS EXPOSED TO WATER AND WEATHER THAT IT CAUSES THE WATER STOP TO SWELL AND VISIBLE CRACKS ARE SHOWN. HOW TO CORRECT THIS BEFORE CONTINUING CONCRETE POURING?
How can we connect different material class waterstops in our installation works say pvc and neoprene joining together?
What a very informative discussion about waterstop from a reputable, experienced and meticulous waterproofing consultant. Do you have writings available for copying in your website?
What continues to baffle me is why anyone believes a small piece of expansive material will do anything to prevent water intrusion through a concrete foundation wall and footing after an entire system designed and installed to prevent ANY infiltration fails. The concrete is not waterproof by nature and there are cracks and tie holes and other weak points where water will always find its way. We install this product in short 6″ or 8″ curbs/walls and it actually explodes the concrete. It is my belief waterstop can be marginally beneficial in instances where there is not waterproofing where there is not hydrostatic pressure but maybe some residual water and it may prevent some migration at the footing to wall horizontal joint. I find it hilarious that waterproofing companies require “their” version of what is essentially the same product as part of their waterproofing warranty. It’s the equivalent of saying you need a red solo cup on your boat to assure the warranty on the boat being able to not take on water.
If you are blowing up concrete, it is because you are using a hydrophilic waterstop and not providing sufficient concrete cover. Most of these products will require a minimum 2″ cover on all sides of the waterstop material.
Over lapping waterstop is not the correct way to continue through the joints, they must be welded to each other to continue through.
How to determine width PVC waterstop for internal Construction joint compared to the depth of water ?