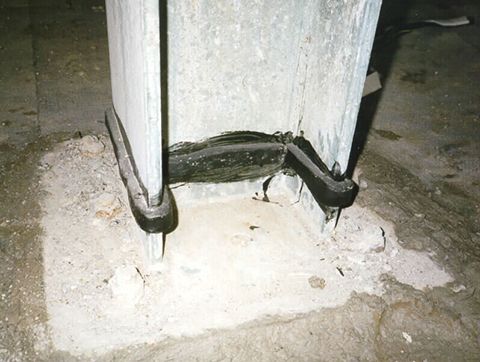
Non-expanding mastic strip waterstops
Mastic-strip waterstops are not susceptible to prehydration expansion like bentonite or hydrophilic rubber materials, but their reliance on adhesion to the concrete might prevent complete sealing of the joint if some areas are not bonded or joined together properly.
Like hydrophilic waterstops, most non-expanding mastic waterstops are produced in rolls or strips. The profile is usually a small rectangle shape, with 20 x 25 mm (¾ x 1 in.) being the most common for butyl-rubber compounds and dimensions of 38 x 12 mm (1 ½ x ½ in.) for asphaltic-based strips.
Mastic waterstops are typically a strip of tacky, asphaltic, or butyl rubber based compound. They are designed to stick to a primed surface of a cured concrete cold joint. The strip is adhered at a minimum embedment depth in accordance with the manufacturer’s guidelines and then a second concrete pour is cast that encapsulates the remaining three sides. The heat from the hydrating concrete causes the product to become even tackier, thereby sealing the joint by acting as an internal, adhered sealant.
Adhesion is important. Should the waterstop be displaced during the concrete pour, it can easily lose most, if not all, its water barrier performance. Mastic waterstops are designed for construction joints only—they should not be specified for use in expansion joints.
Mastic waterstop hydrostatic resistance performance is very limited as the only barrier to migrating fluids is the adhesion to the concrete of the low profile strip. Mastic waterstops are the lowest-performing of any commercially available waterstop and are priced accordingly, being the lowest in cost.
Injection-hose waterstops
Injection-hose waterstops are usually permeable or perforated hose installed during new construction with a series of injection ports and valves. These ports are placed exposed at the interior surface of the concrete for later access. Should a leak occur after construction, a grout pump can be used to inject a resin (usually polyurethane) to seal the joint and fill any adjacent voids in the concrete.
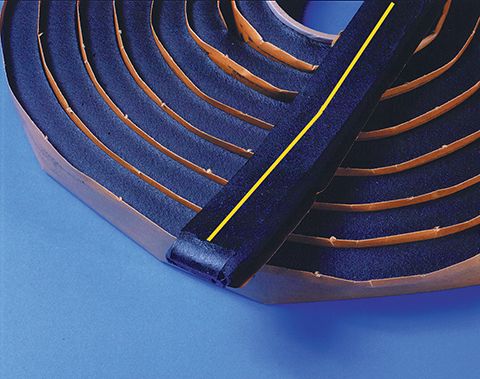
Manufacturers purport some products to be ‘re-injectable,’ but this is frequently not the case, due to cured resin surrounding the hose or contractors not adhering to the manufacturer’s guidelines (i.e. chiefly not cleaning out the hoses properly after the initial resin injection).
Each injection hose system uses permeable hose that is installed at construction joints, in short lengths (typically less than 9 m [30 ft]). The hose core is surrounded by a woven mesh outer layer so resin injected under pressure can pass out of the tube into the joint, but cement fines and aggregates cannot enter the hose and clog it. The hose is secured to the first concrete pour after it sets with clamps mechanically fastened (typically 305 mm [12 in.] on center).
Adjacent perforated hoses are placed overlapped by 150 to 300 mm (6 to 12 in.) at each segment end, with a short non-perforated tube attached in-line that exits the concrete as the injection port. After the structure is built, polyurethane resin is injected into the hose to seal the joint and fill any cracks or voids in the joint area. They can also be used to seal construction joints between new and existing structures. Typical applications include secondary containment, basements, and tunnels.
Metallic waterstops
Metallic waterstops can obstruct the passage of corrosive fluids, even at severely elevated temperatures. Therefore, metallic waterstops are used primarily for severe chemical and high-temperature environments that can degrade other materials. A variety of metals, grades, and gauges are available.
Stainless steel offers broad-spectrum corrosion resistance, and is virtually unaffected by the effects of ozone, making it an ideal choice for ozone contactor structures used in modern water treatment plants. Stainless steel waterstops are available in many standard shapes and sizes, including profiles for new and retrofit. All change-of-direction fabrications should be pre-manufactured, leaving only straight butt-welding in the field.
Metallic waterstops are probably the most difficult to install, as split-forming is always necessary by means of tungsten-inert-gas (TIG) or metal-inert-gas (MIG) welding. All straight-run material should be welded edge-to-edge (no overlapping).
The stiffness of metal waterstops can lead to cracking of adjacent concrete. Thereby, rigid metal waterstops should be installed with adequate concrete coverage.
One question. When overlapping the water stop. What is the minimum overlap?
the ends should not be lapped, the ends should be welded together.
I thought that too but I’m not sure how that’d be accomplished…. Can you elaborate on this detail please….. Thanks in advance
You have to use a Splicing Iron (most waterstop manufacturers discuss splicing irons in their installation guides and other product information sheets).
is splicing iron possible to connect two waterstops with different material?
WHAT IF THE WATER STOP IS ALREADY ATTACHED TO THE CONCRETE AND DUE TO DELAYED WORKS IT IS EXPOSED TO WATER AND WEATHER THAT IT CAUSES THE WATER STOP TO SWELL AND VISIBLE CRACKS ARE SHOWN. HOW TO CORRECT THIS BEFORE CONTINUING CONCRETE POURING?
How can we connect different material class waterstops in our installation works say pvc and neoprene joining together?
What a very informative discussion about waterstop from a reputable, experienced and meticulous waterproofing consultant. Do you have writings available for copying in your website?
What continues to baffle me is why anyone believes a small piece of expansive material will do anything to prevent water intrusion through a concrete foundation wall and footing after an entire system designed and installed to prevent ANY infiltration fails. The concrete is not waterproof by nature and there are cracks and tie holes and other weak points where water will always find its way. We install this product in short 6″ or 8″ curbs/walls and it actually explodes the concrete. It is my belief waterstop can be marginally beneficial in instances where there is not waterproofing where there is not hydrostatic pressure but maybe some residual water and it may prevent some migration at the footing to wall horizontal joint. I find it hilarious that waterproofing companies require “their” version of what is essentially the same product as part of their waterproofing warranty. It’s the equivalent of saying you need a red solo cup on your boat to assure the warranty on the boat being able to not take on water.
If you are blowing up concrete, it is because you are using a hydrophilic waterstop and not providing sufficient concrete cover. Most of these products will require a minimum 2″ cover on all sides of the waterstop material.
Over lapping waterstop is not the correct way to continue through the joints, they must be welded to each other to continue through.
How to determine width PVC waterstop for internal Construction joint compared to the depth of water ?