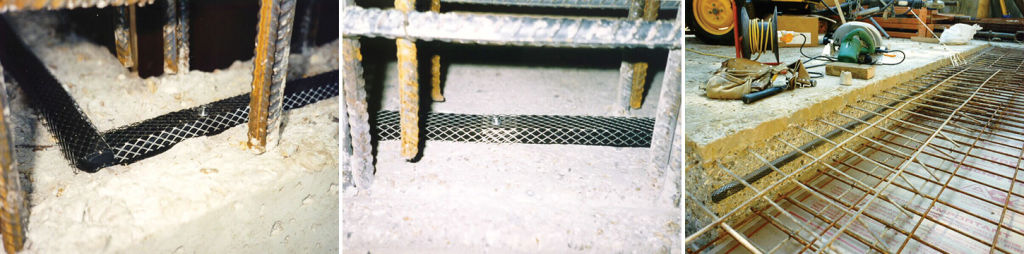
Multiple system installation
Waterstop systems are relatively low
in cost, so having a secondary product installed can be a wise and inexpensive investment. This leads to the question, ‘If the concrete joint has the appropriate width clearance, why not use one waterstop as the primary barrier and another as a secondary barrier as an insurance policy?’ If the primary system fails in any way due to material or installation defect, the second system is there to ensure fluid-tight integrity at the concrete joint.
To clarify, when a ribbed center-bulb or hydrophilic waterstop is properly installed, there is really no need for a secondary waterstop system. Regardless of polymer or manufacturer, these waterstop products really only leak from poor installation procedures and a lack of quality assurance.
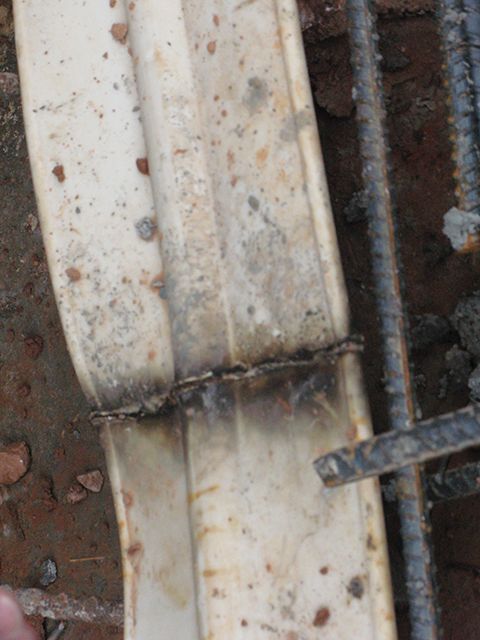
A typical belt-and-suspenders approach would be to have a ribbed center-bulb waterstop on the positive-pressure side of the joint and a hydrophilic or mastic strip-applied waterstop several inches away from it on the negative pressure side of the joint. An alternative secondary waterstop would be an injection tube system placed on the low pressure side.
The benefits of redundancy in installed waterstop systems is great and the cost is low, especially when amortized over an extended life of the concrete structure in which they are installed.
On projects, hydrophilic waterstops can also be used around pipe and mechanical penetrations, while PVC hydrophobic waterstops can be specified for the concrete construction joints.
This author has seen critical infrastructure subway projects with three waterstop systems specified and installed in the construction joints of the thick concrete walls. The installation included a PVC ribbed center bulb to the positive pressure side, a bentonite hydrophilic strip in the center, and an injectable hose waterstop installed closest to the interior face of the concrete wall.
Conclusion
Contractors have perhaps the most important role with regards to waterstops—the installation. These systems should be treated as strategic building envelope barrier material for the long-term success of a project. For any waterstop to be effective, proper design, installation, and concreting practices must be followed. Foremost, one must select a product size and profile suitable for the expected joint movement, hydrostatic head, and chemical resistance required.
Stacy Byrd, GRP, LEED AP, is the national products manager at CETCO, a manufacturer of waterproofing, green roof systems, composite drainage, and waterstops. He has a quarter-century of technical waterproofing design application and practical field experience with below-grade foundations, plaza-decks, tunnels, and vegetated roofs on commercial, institutional, civic, and government projects. Byrd is an active member with ASTM International Committee D08 on Roofing and Waterproofing and a Green Roof Professional (GRP). He can be reached at stacy.byrd@cetco.com.
One question. When overlapping the water stop. What is the minimum overlap?
the ends should not be lapped, the ends should be welded together.
I thought that too but I’m not sure how that’d be accomplished…. Can you elaborate on this detail please….. Thanks in advance
You have to use a Splicing Iron (most waterstop manufacturers discuss splicing irons in their installation guides and other product information sheets).
is splicing iron possible to connect two waterstops with different material?
WHAT IF THE WATER STOP IS ALREADY ATTACHED TO THE CONCRETE AND DUE TO DELAYED WORKS IT IS EXPOSED TO WATER AND WEATHER THAT IT CAUSES THE WATER STOP TO SWELL AND VISIBLE CRACKS ARE SHOWN. HOW TO CORRECT THIS BEFORE CONTINUING CONCRETE POURING?
How can we connect different material class waterstops in our installation works say pvc and neoprene joining together?
What a very informative discussion about waterstop from a reputable, experienced and meticulous waterproofing consultant. Do you have writings available for copying in your website?
What continues to baffle me is why anyone believes a small piece of expansive material will do anything to prevent water intrusion through a concrete foundation wall and footing after an entire system designed and installed to prevent ANY infiltration fails. The concrete is not waterproof by nature and there are cracks and tie holes and other weak points where water will always find its way. We install this product in short 6″ or 8″ curbs/walls and it actually explodes the concrete. It is my belief waterstop can be marginally beneficial in instances where there is not waterproofing where there is not hydrostatic pressure but maybe some residual water and it may prevent some migration at the footing to wall horizontal joint. I find it hilarious that waterproofing companies require “their” version of what is essentially the same product as part of their waterproofing warranty. It’s the equivalent of saying you need a red solo cup on your boat to assure the warranty on the boat being able to not take on water.
If you are blowing up concrete, it is because you are using a hydrophilic waterstop and not providing sufficient concrete cover. Most of these products will require a minimum 2″ cover on all sides of the waterstop material.
Over lapping waterstop is not the correct way to continue through the joints, they must be welded to each other to continue through.
How to determine width PVC waterstop for internal Construction joint compared to the depth of water ?