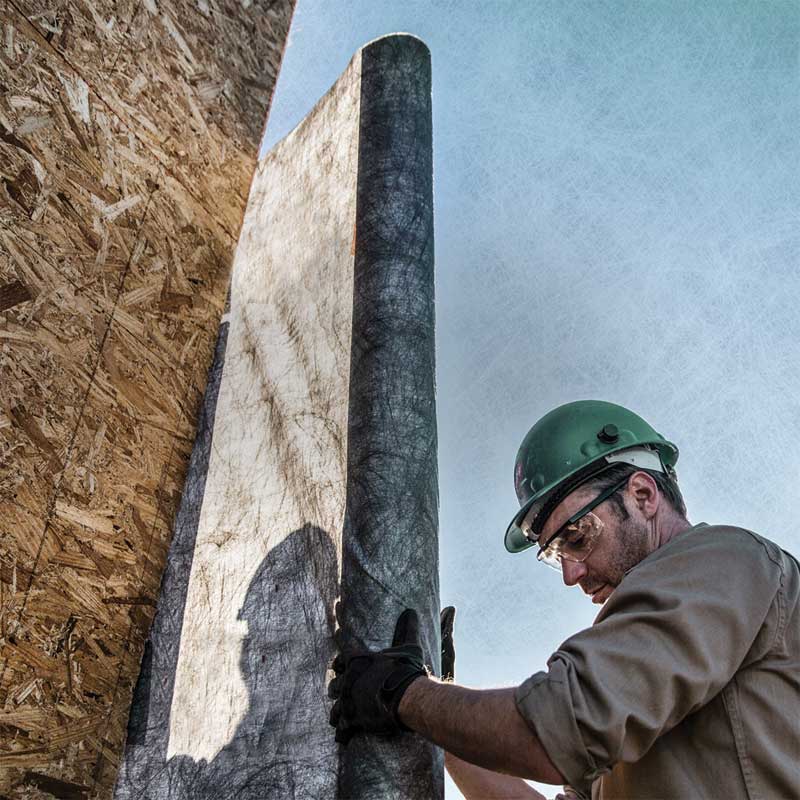
Why use an air barrier?
It is important to establish a continuous air barrier for several reasons. As an air barrier isolates the indoor environment, it plays a major role in the overall energy efficiency, comfort, and indoor air quality (IAQ) of a building. According to the U.S. Department of Energy (DOE), up to 40 percent of the energy used to heat and cool a building is consumed due to uncontrolled air leakage. Establishing a continuous air barrier reduces heating and cooling costs, thereby lowering greenhouse gas (GHG) production.
Air barriers create a much more comfortable environment for building occupants by reducing drafts, keeping conditioned air inside the building, and minimizing temperature differences between rooms. Air barriers play a central role in ensuring healthy indoor air, as well, because they reduce the infiltration of outdoor air pollutants and help control moisture issues that can lead to problems like mold growth.
In addition to the 2012 IECC requirement, a growing list of states now includes air-barrier requirements in their commercial energy conservation codes. Among these are California, Oregon, Illinois, the District of Columbia, and Massachusetts. The U.S. government mandates air barriers be installed on federally funded building projects, as well.
Air barrier systems comprising building wraps
Numerous materials can achieve the ASTM air leakage requirement, but this does not necessarily mean they will perform in the field once installed as part of a system. The question becomes whether the material will be able to hold up to the rigors of the jobsite and installation. After all, an air barrier’s performance is defined by its weakest link, and it only takes one tear or unsealed connection to compromise the entire system’s integrity.
Standing up to the elements is a tall task. As the primary boundary between indoor and outdoor air, the assembly will be subjected to constant air movement, water, ultraviolet (UV) light, and surfactant chemicals present in certain cladding materials and cleaning agents. Any one of these elements could potentially cause materials to break down over time, jeopardizing their effectiveness as air barriers. Likewise, if a material is not sufficiently durable to stand up to installation conditions, it cannot perform its function.
Commercial construction amplifies the importance of these concerns. Exceptional durability is needed to handle the stronger wind loads faced by taller buildings. Tear strength, as measured by the grab trapezoidal tear test as part of ASTM D5034, Standard Test Method for Breaking Strength and Elongation of Textile Fabrics (Grab Test), is a good measure for predicting an air barrier’s ability to stay on the wall after installation. In this test, a 1.2 x 1.8-m (4 x 6-ft) sample is tested for tensile strength by moving a pair of clamps apart at the specified rate until the specimen breaks or ruptures.
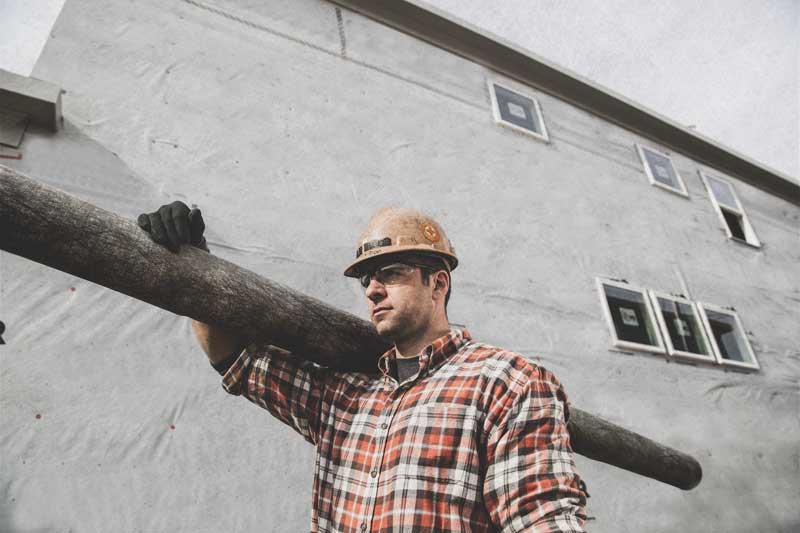
Further, the longer construction timelines typical of many commercial building projects put added emphasis on an air barrier’s ability to withstand extended exposure to UV light, as weeks or even months may pass before exterior cladding is installed over the building wrap. It is critical to double-check how much exposure time the manufacturer’s warranty covers.
It is also important to consider the type of exterior cladding to be installed over the building wrap. Some materials, such as brick or stucco, absorb moisture that can be driven into the wall assembly by solar energy. Stucco, cedar, and other wood sidings may also contain surfactant chemicals (e.g. soaps, oils, and paints) that can degrade the performance of a building wrap over time, so it is important to choose a material resistant to these chemicals to ensure sustained performance.
While several materials can impede air movement through a wall assembly, certain technologies perform better than others in demanding conditions. Historically, wood-pulp-based building paper was the most commonly used material for weather-resistant barriers, but it tends to tear easily and is not very durable. In the 1970s, plastic building wraps made of polyethylene or polypropylene fabric began gaining popularity for their durability and ease of installation, and these remain reliable options.
Plastic building wraps are typically either woven or non-woven—an important difference when it comes to specifying an air barrier. Woven polypropylene with slit-film perforated coating typically offers two months of UV resistance, but most types do not meet ASTM requirements for air-barrier materials and are not surfactant-resistant. That said, spun-bonded polypropylene with micro-porous coating, on the other hand, often meets ASTM requirements set for air barriers, is resistant to surfactant chemicals, and offers six months UV exposure resistance. Depending on the type of cladding to be installed over the wrap, and how long the wrap will be exposed to the elements before the cladding’s installation, these additional durability benefits may be important.