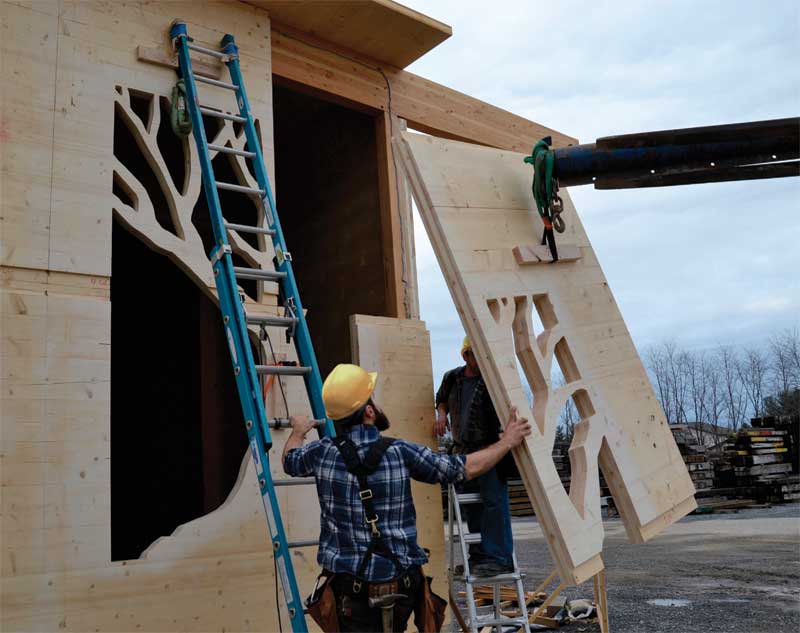
Sequencing, scheduling, and communication
A raising script or step-by-step plan was vital to the success of the hybrid project. Software was used to develop a 3D, fly-through visual representation of the sequencing, which was shared with the CLT manufacturer, onsite workers, officials, and subcontractors. Meanwhile, the CLT project management team created a computer-aided design (CAD) fabrication file for the finishing touches, which New Energy Works was able to review and provide feedback on to ensure an accurate fit of parts. Open and constant lines of communication between groups allowed the project to proceed with relative ease.
The panels were shipped from the manufacturer overseas in containers (resulting in a much lower carbon footprint than shipping via ground across the nation), which necessitated planning for offloading, staging, and preserving the material from weather before receiving any shipments. The company collaborated with the CLT manufacturer on the order in which the panels were stacked in each container and in what progression they would arrive at the site. Any sequence modifications would impact this process, potentially slowing it down or requiring a full rework of the original sequenced plan, and could have much bigger implications on larger projects, or on a site without enough staging area.
As the lighter CLT panels tie in with the timber frame, their installation was done in unison with raising the frame, allowing it to act as bracing. Containers arrived onsite while timbers for the frame were being staged. A set of shop drawings was used as an installation guide, providing the panel numbers (and therefore the sequence), along with fastening and air-sealing details. The teams were aware of what container they were working with and, as was planned, only needed access to two containers at a time during the install. Packets (i.e. bundles of CLT panels) were placed in containers in reverse order to account for offloading onsite in the correct order. This process also helps minimize handling as much as possible in the field.
The panels were each tagged with three variables:
- the container number;
- W’ or ‘R’ to designate wall or roof panel; and
- the installation sequence number.
To ensure accuracy, several layers of numbering were employed in the project, including the sequence number. There were numbers specific to each panel, as they all had a precise location to be installed. The packets previously mentioned were used for loading and offloading the panels, and were packed in a manner that best aligned with the installation sequence while preserving efficiency of shipping volume.
The combination of many great minds working together, offering their expertise and dedication, helped provide a smooth learning curve without many site challenges during raising of the new wood shop.