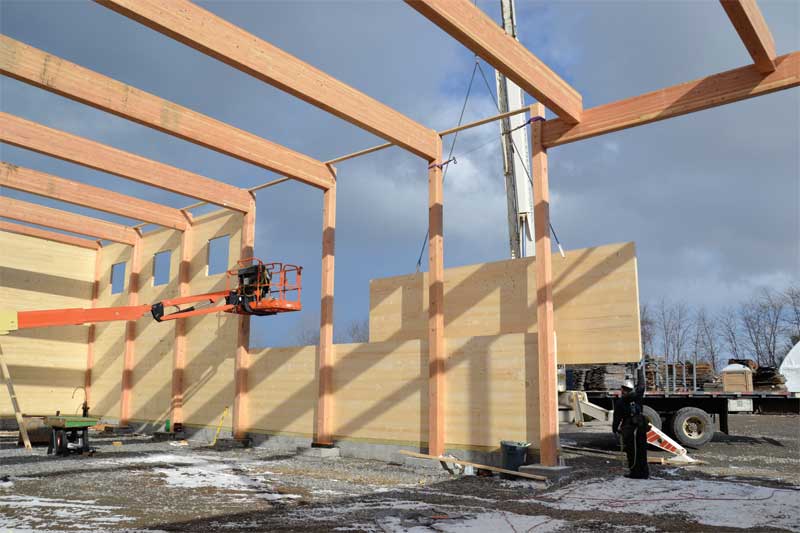
Other components
New Energy Works is one of the first U.S. companies to incorporate advanced wood fiber insulation board on the walls and roof of a commercial building. Another product produced from sustainably managed and certified forests, the board offers a thermal efficiency of R-3.5 per inch, stores carbon, and is prepanelized for efficient onsite installation. For the walls of this CLT project, the project team installed 101-mm (4-in.) wood fiber wall panels and 203-mm (8-in.) roof panels. Manufactured with a tongue and groove, each panel nested together smoothly for effective installation.
At this time, exterior wood fiber insulation is a more expensive option than rigid petroleum-based insulation types such as expanded polystyrene (EPS), extruded polystyrene (XPS), polyisocyanurate (polyiso), and mineral wool. All of these work to enclose the exterior of the structure, breaking the thermal bridge that otherwise lessens the efficiency of the cavity-based insulation methods typical in U.S. construction. However, wood fiber insulation achieves this goal with a
very low carbon footprint. The decision to go this route was a conscious one by New Energy Works, supporting the development of the European manufacturing technology in the United States. The company believes the technology
will only become more financially viable with domestic manufacturing facilities.
A special post in this project is a 60-year-old Acer macrophyllum (i.e. big-leaf maple) selected for its particular size, shape, and branch structure. It is a loadbearing post supporting a 13,608-kg (30,000-lb) gravity load and a 25-m (84-ft) glulam beam. The beam pocket is made up of two upright co-dominates (co-dominate, in this case, refers to how the main trunk splits and becomes two). A chainsaw with a 1067-mm (42-in.) bar was used to cut the base. In a personal touch, New Energy Works employees signed the base prior to raising the post.
The company also explored peg-laminated timber (PLT), crafting 6-m (20-ft) panels using reclaimed wood planks and hardwood pegs. Weighing 4989 kg (11,000 lb) each, joined with thousands of pegs, the panels form the building’s entry roof, topping industrial salvaged timbers. While interesting and aesthetically pleasing, their creation proved less efficient in terms of time spent on fabrication than using prefabricated, fully manufactured panels.
A clerestory allows natural light into the production space, reducing the demand for artificial lighting. Future plans include a rooftop photovoltaic (PV) system to tie in with the campus’s existing 400-panel array.