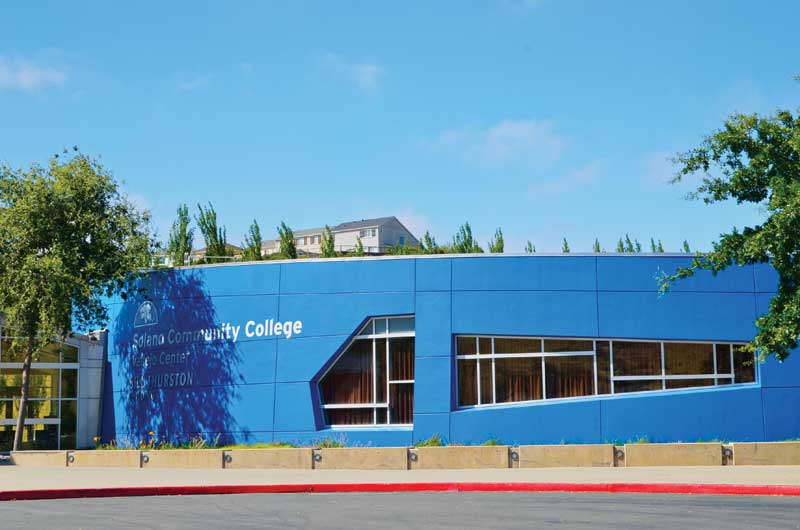
3. What are the relevant environmental and safety concerns?
In the United States, numerous Occupational Safety and Health Administration (OSHA) standards cite how, when, and where workers need to be protected. Adequate ventilation and proper National Institute for Occupational Safety and Health (NIOSH)-approved respirators are imperative. One should inquire about the written documentation for compliance with OSHA, local and equipment regulations, and guidances to help avoid liability.
Protecting a building’s occupants and guests is also important. Objectionable odors and chemical vapors can be significantly reduced or eliminated entirely with water-based coating formulations that are low in volatile organic compound (VOC) content and applied by brush or roller instead of spray equipment. VOC regulations vary by state; as an example, California specifies industrial maintenance coatings should contain 100 g/L or less, according to South Coast Air Quality Management District (SCAQMD) 1113. (For projects seeking certification under the Leadership in Energy and Environmental Design [LEED] program, VOC limits can be a concern for building owners and specifiers when sourcing compliant architectural coatings. For exterior architectural coatings, U.S. Green Building Council [USGBC] uses California Air Resources Board Suggested Control Measure [CARB-SCM] Compliant Exterior Coatings, SCAQMD Rule 1113, Ozone Transport Commission [OTC], and other state-specific regulations to comply with the certification.)
Another environmental concern is wastewater runoff. This is critical when one considers the total VOC content in the coatings used on the job can eliminate nonconformances with local and state/province regulatory codes.
A coating system is more than just paint
The vast majority of coating system failures can be traced to poor surface preparation. In the case of newly applied substrate materials like concrete, masonry, and plaster, it is important to let the substrate material cure for at least 30 days before coating—a critical project timeline consideration. For steel, the degree of corrosion and pitting need to be evaluated and properly mitigated prior to coating with a product that will effectively stop the corrosion from continuing.
A primer will provide an important bonding layer to help the topcoat adhere to the surface. Compatibility between the primer and the topcoat is crucial; one should never specify a primer from one manufacturer and a topcoat from another and expect the two products to be compatible. Incompatibilities can lead to poor intercoat adhesion, which can allow moisture to get in between the primer and the topcoat, leading to blistering or delamination. ( To ensure compatibility between shop primer and field-applied coatings, one should consult the coatings supplier/manufacturer, which should conduct adhesion testing on the surface prior to specifying a coating system for the job. The provider will test topcoat over the primed surface and/or tie coat options compatible with its formulation. Manufacturers can also consult on the number of coats for an application.)
As this article makes clear, selection of the right primer depends on the substrate and the environment. Some primers are specially formulated to resist corrosive chemicals, while others are formulated to block the migration of tannins and efflorescence (i.e. salt). When using a water-based primer on a metal surface, good initial water resistance and protection against rust are important properties.
Proper application techniques for the primer and topcoat must be followed, according to the coating manufacturer’s instructions. The coating system’s field application guide, product data sheets, and CSI specification will outline coverage rates, dry time (to touch and to recoat), pot life, reduction instructions, and optimal ambient temperature and humidity conditions for application. Although it is not always possible, application in direct sunlight also should be avoided, as sunlight can affect the flow, leveling, and application characteristics. High wind velocities can impact spray application, which can result in loss of materials, low film build, excessive dry spray, or overspray. It is important to work all these weather-related variables into the project timeline.
If the structure is normally exposed to dust and contaminants, the RFP must address how the contractor will protect the surface during the application and curing process. Dust and contaminants that settle on freshly applied coatings can impair the integrity of the coating, leading to a shorter coating life and reduced performance.
It is always a good idea to require an installation mockup on a small portion of the structure prior to coating the entire structure to allow for adhesion testing and ensure the finish and color meet the client’s expectations.