Veneer extrusion systems incorporate all the performance issues the mullion’s connection to the glass does, but the aluminum box structure is eliminated. As a result, it does not have the structural performance of a typical curtain wall and must be supplemented with something else. This opening presents an opportunity. Why use an aluminum box when a glued-laminated timber (glulam) or steel fin would perform even better or span farther? Also, why not change the overall look from conventional to extraordinary?

Photo © Paul Rivera
Another limitation is an aluminum box structural system is generally only extruded in sizes to fit common apertures. For regions struggling with high wind speeds, or projects requiring spans exceeding the prescribed 6 or 7 m (20 or 23 ft), this is clearly an issue. Aluminum box systems necessitate breaking up longer spans with more conventional structures not part of the original system. However, if the aluminum box could be replaced with another structural element that would allow for 9-, 12-, or 30-m (30-, 40-, or 100-ft) spans, greater performance could be delivered, and the designer’s original intent would be more elegantly accomplished. Other structural elements could include steel-fin plates, or glulams and steel beams. Even structures normally used for floors or roofs can be reconfigured to support curtain walls.
Further, using a veneer curtain wall system allows warranties and tested assemblies for water and air infiltration to be maintained, while delivering a capture system glass installers can feel comfortable working with. As the system’s complicated thermal and condensation performance factors are accommodated within the veneer, installers can easily fasten it to conventional structural members. This benefits designers looking to create unique façades to increase span distances and produce a customized look, without sacrificing performance. Reconfigured veneer systems also exceed conventional approaches without necessarily spending more, as the material costs of these alternate systems are often significantly less than the price of aluminum.
An example of a high-performing reconfiguration of a veneer system is the 12 by 21-m (40 by 70-ft) high, curved façade of the City of Denver’s new Ralph L. Carr Justice Center, which looks out on Colorado’s capitol dome (shown on the cover and on page 20). This system was designed using a series of horizontal steel plates suspended from the roof with veneer extrusions mounted to them. Designed as a one-way span, the glass eliminates the need for vertical mullions, increasing the system’s transparency. The conventional method of creating a façade for this space would have required large, steel-tube wind girts at 6 m on center (oc), with an aluminum curtain wall system spanning the distance between them. However, this would have greatly decreased sightlines and eliminated some of the system’s elegance. Interestingly, the veneer system was less expensive than the alternative, which would have required additional structure and connections.
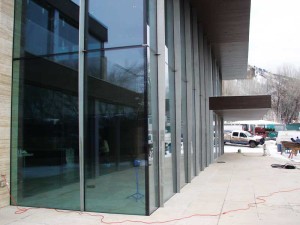
Photo courtesy Pinnacle Glass
Structural silicone glazed systems
Another example is particularly useful where a higher-performing system with less thermal bridging is required. More often than not, structural designers and specifiers eliminate the exterior façade element that makes up the capture system, and then adhere the glass to the structure using structural silicone glazing (SSG) or very-high-bond (VHB) tape. However, once again, when the intent is to simply adhere the façade to the aluminum box (which is essentially just structure), then why not adhere it to something more interesting—such as steel or glass fin?
An added benefit is SSG systems—‘thermally broken’ with a thermal conductivity at or below 3.6-BTU-in/hr-sf-F and a minimum thickness of 5.3 mm (0.21 in.)—have superior thermal and air infiltration performance. Further, none of their lateral support elements extend through the glazing joint. Although many ‘thermally improved’ systems tie elements to interior elements with materials more thermally inert than aluminum, a thermal bridge is still being created. Also, while numerous aluminum box systems operate in this manner, they clearly limit architectural aesthetics and potential spanning capabilities. On the other hand, using structural silicone allows the bridge to be eliminated.
This SSG system approach is demonstrated by the recently completed Colorado School of Mine’s Marquez Hall project located in Golden, Colorado. Here, the typical aluminum curtain wall was replaced with steel fins suspended from the roof. This allowed a system that is primarily in tension, eliminating buckling as a control in the structural design to be developed. In fact, it would have to experience compression—either locally due to bending, or globally—to have buckling reach failure mode. Thus, by hanging the system, the fin has been essentially pre-stressed to ‘trick’ it into behaving as if it was in tension.
A typical aluminum mullion is 63.5 mm (2.5 in) wide, and the depth is governed by the span. However, with the hung steel-fin system, the structure is only 12.7 mm (½ in.) thick, and it exceeds the span capabilities of a conventionally reinforced aluminum curtain wall by more than 50 percent.
Of further interest is Marquez Hall’s 9-m (30-ft) tall façade where design wind speeds can exceed 185 km/h (115 mph). Since the façade employs a double insulated unit, or triple-glazed panels, the system had to include three lites of 6.3-mm (¼-in.) glass, which also provides greater rigidity than a typical insulated glass unit (IGU). This made it even easier to eliminate the horizontal mullions and span the glass horizontally.
Typically, façades that do not use horizontal mullions to support the glass panels’ weight are point-fixed. Point-fixed glass traditionally requires bolts and holes inserted into it, which increases not only costs, but also, frequently, thickness. More recently, many in the industry have moved to clamps installed at the corners of the glass panels, but with castings. On Marquez Hall, the upper glass panels bear on steel plates and a cover plate is thermally isolated and adhered to the glass to protect the bearing joint from weather. In using steel plates to create corner clamp details, the design team was able to achieve a more cost-effective design by eliminating expensive castings and bolt fittings. Sight lines were also minimized as the steel plate can be directly welded to the fin.