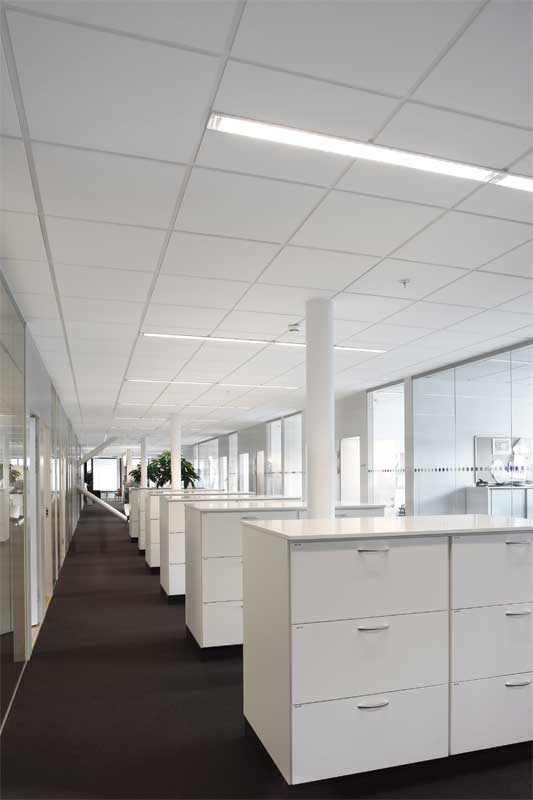
Stone wool plenum barriers
Plenum barriers can be constructed of a variety of different lightweight materials, including:
- limp, mass-loaded vinyl (MLV);
- stone wool insulation with a foil facing;
- standard gypsum wall board; or
- some combination of these materials.
This article omits research done on MLV plenum barriers because they generally do not perform as well as stone wool insulation and gypsum-board plenum barriers; further, plenum-rated MLV is much more costly than stone wool insulation and gypsum board. Additionally, the MLV plenum barriers are more time-consuming to install.
While gypsum-board plenum barriers are just as cost-effective as stone wool plenum barriers and perform as well acoustically, the rigidity of the material can be a disadvantage in some buildings where there is floor/roof deflection, seismic joints, or expansion/contraction joints. This article focuses on stone wool plenum barriers due to their low cost, relatively quick installation, pliability, and high sound-isolation performance, but other materials may prove to be appropriate in some applications.
The goals of this most current phase of the research were twofold. First, the objective was to test whether stone wool plenum barriers could achieve the high sound-isolation ratings that are required by acoustic standards. Secondly, the mission was to determine whether the plenum barriers could be simplified to decrease material cost or installation time. The test series investigated if the thickness/weight of the plenum barrier could be decreased, if the foil facing could be eliminated, and if taping the vertical seams between plenum barrier panels could be eliminated.
A series of sound-isolation tests was performed on a suspended, modular, acoustic ceiling system with and without various lightweight plenum barriers under laboratory conditions in a dual-room chamber. For the baseline test, the specimen comprised a metal suspension grid filled with ceiling panels, but no plenum barrier above the demising wall. Subsequent tests added various lightweight plenum barriers. In all cases, the ceiling grid ran continuously (uninterrupted) over the top of the laboratory’s central demising wall.
A senior test engineer performed all tests at NGC Testing Services (Buffalo, New York). The laboratory is accredited by the National Voluntary Laboratory Accreditation Program (Laboratory Code 200291-0). Tests were performed according to ASTM E1414, Standard Test Method for Airborne Sound Attenuation Between Rooms Sharing a Common Ceiling Plenum, and ASTM E413, Classification for Rating Sound Insulation.
Figure 3 shows the single- and double-layer stone wool plenum barriers being installed in the laboratory for testing. The stone wool material was 38 mm (1 ½ in.) thick with a density of 128 kg/m3 (8 pcf) and surface weight of 4.88 kg/m2 (1.5 psf).
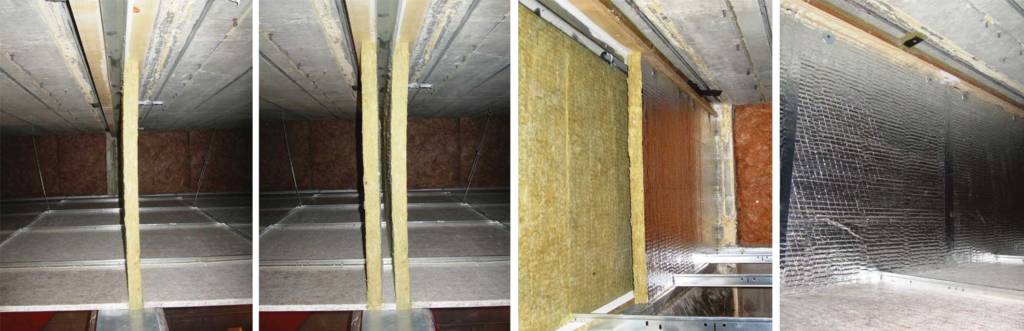
For most of the tests, the plenum barrier panels had a fiber-reinforced foil facing on one side. When the double-layer plenum barriers were tested, the foil was oriented toward the open ceiling plenum—not into the small, interstitial airspace between the two layers. The plenum barriers were mechanically fastened along the top edge using common, self-tapping, sheet metal screws with insulation washers into a common 41-mm (1 5/8-in.) wide metal channel attached to the test chamber overhead slab. Screws were spaced approximately 305 to 457 mm (12 to 18 in.) on center (o.c.). Typically, each 610-mm (24-in.) panel had two screws along the top. The bottoms of the plenum barriers were only friction-fitted against the top track of the demising wall and the grid. They were not mechanically fastened, glued, or caulked. No neoprene gaskets (as seen in some project-specific plenum barrier details) were used.
Each panel was abutted to the adjacent panels along the sides with no overlap. For some tests, the vertical seams between adjacent panels were taped using 50-mm (2-in.) wide metal tape for sealing butt-joints. When the double-layer plenum barriers were tested, the 610-mm (24-in.) wide panels were staggered 305 mm (12 in.) so the seams were not aligned. This required a small cut along the bottom of one layer of the plenum barrier panels so they could slide down over the grid bulb and allow the bottom of the plenum barrier panel to sit on the top track of the demising wall.
No caulk or sealant was used. Small gaps around and between some of the plenum-barrier panels were visible. Most gaps were closed during installation due to the pliability of the stone wool. The panels were cut slightly oversized and then compressed vertically and laterally during installation, which helped prevent gaps.
what about security of the adjacent room in case the plenum barrier is used.