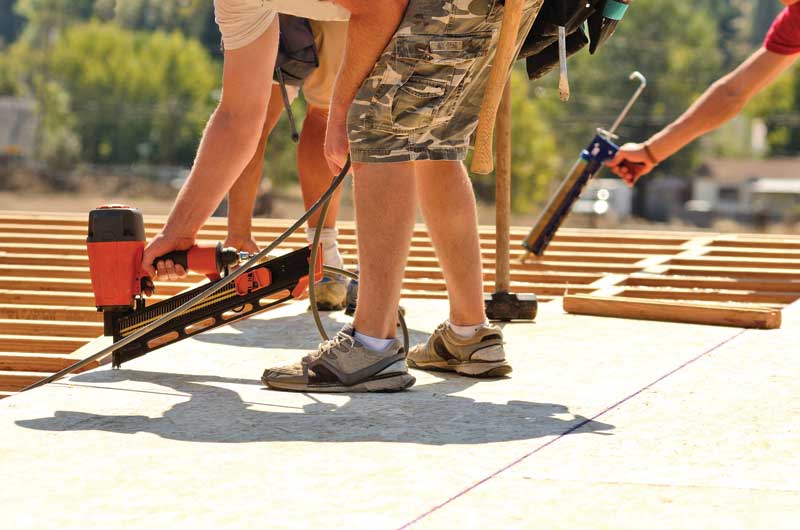
by Thomas D. Skaggs, PhD, PE
Engineered wood products are specified for a wide range of light-frame floor assemblies in light commercial and multi-family construction. I-joists, glued-laminated timber (glulam), rim board, laminated veneer lumber (LVL), laminated strand lumber (LSL), and oriented strand lumber (OSL) are popular due to their availability, precision, strength, and consistent quality.
As use of these products expands beyond conventional construction, engineers and specifiers are raising questions concerning the use of I-joists and rim board around the perimeter of the structure, where the wood floors are designed as diaphragms and the walls above are designed as shear walls.
In these applications, the engineered wood product forming the rim joist/board around a floor system is subject to numerous loads not normally considered in conventional, non-engineered applications. These additional factors include:
- transfer of shear wall forces from the walls above into the foundation/wall framing below;
- diaphragm perimeter nailing; and
- shear transfer of diaphragm loads to the foundation/wall framing below.
Such design forces create attachment requirements that exceed normal fastening requirements found in the building codes. The designer’s challenge is to detail these critical connections in order to transfer the applied loads through the connection economically and efficiently. One should consider that rim boards and I-joists may be used in rim joist applications, offering predictable performance and consistent quality. (Attachment considerations vary.)
Rim board
The International Building Code (IBC) is consistent in prescriptively requiring rim joists to be attached to structural framing below with 8d 3.3 x 63-mm (0.131 x 2 ½-in.) common toe nails spaced at 150 mm (6 in.) on center (oc) for conventional construction.
While this attachment schedule is sufficient to develop a lateral load capacity of 2.63 to 2.92 kN/m (180 to 200 lbf/ft)—as required for the conventional IBC construction provisions—it falls short of developing the actual lateral load capacity of the rim joist products, which exceeds 14.59 kN/m (1000 lbf/ft).
One should be cautious when attempting to increase shear-transfer capacities of the rim joist by spacing toe nails closer than 150 mm oc. Closer spacing may cause splitting in some rim joist products, and an increased lateral load capacity may not be achieved using this technique. Instead, one should consider using framing anchors or blocking to develop the additional lateral capacity required when using rim boards for transferring shear loads through floors.
I-joists
I-joists may be used as rim joists at diaphragm perimeters. By virtue of their flanges, toe nails are rendered unnecessary, making I-joists easier to attach to structural framing above and below the joist.
However, because flanges in some I-joist configurations may split with close nail spacing, the diaphragm lateral load capacities are limited by the minimum nail spacing recommended by the I-joist manufacturer. In some cases, staggered nailing may be necessary to develop the full diaphragm lateral load capacities.
Preventing incompatibilities
Some design professionals may be surprised to learn that they should never mix engineered wood products and sawn lumber in a roof or floor system without careful analysis of the potential consequences.
Engineered wood products are manufactured at very low moisture contents (i.e. five percent or lower) and with a high degree of dimensional accuracy. On the other hand, sawn lumber products are sized and sold at moisture contents often exceeding 16 percent. When used together on a jobsite, the engineered wood products may expand due to increased moisture content, while the sawn lumber products may shrink as they dry. In situations where lumber and engineered wood products are used together and are intended to ‘share’ vertical loads in floor or roof systems, this differential shrinkage can lead to situations that must be carefully considered.
There are applications, such as diaphragm, ‘squash,’ backer, or filler blocking, where sawn lumber may be used in conjunction with engineered wood products. In these applications, the sawn lumber member either does not carry vertical loads or is used in such a way the load is applied to the end grain in specifically sized members.
As an owner and subcontractor who spends 30% of my time on Safety and compliance issues, the first thing I notice in pictures such as the one above for engineered floors , is the sneakers, shorts, and no fall protection. The PPE requirements, cost to the job, and time invested to keep crews working safely has skyrocketed over the years. I think professional publications should reflect what CSI members actually look like in the field.
Thanks
CSI has been a great organization for us
Transfer of shear floor to floor. To all the Structural Engineers I pose the question when a floor truss,i-joist or roof truss gets cut or drilled inadvertantly some sort of fix is needed,generally is OSB or Plywood used to “gusset” the members together, its always been a very strong and effective way to cure the problem.I have framed millions upon millions of square feet of wood frames 4-5:story commercial, 1-3:story residential. Exterior shear walls OSB is easily stronger vertically then horizontally even when blocked. Transfer of shear, I continuously gusset the floors with the exterior sheathing 1st floor walls to 2nd floor walls to 3rd & 4th to 5th & parapets. It transfers shear better then what is shown and adds hold down. Why dont engineers understand this??