![airbarriers_ReleasesMoisture-ALT-v2-FA_text[1]](http://www.constructionspecifier.com/wp-content/uploads/2015/05/airbarriers_ReleasesMoisture-ALT-v2-FA_text1-e1430936989614.png)
Making a moisture sandwich
A moisture sandwich occurs when a well-insulated wall system traps moisture from both the interior and exterior components. It is a scenario playing out with frequency as architects design walls and incorporate insulating products that create energy-efficient buildings. For example, many areas of the country are beginning to install exterior insulation to help increase a wall’s R-value, decrease its thermal bridging, and reduce the permeance level.
Extruded polystyrene (XPS) has a permeance level of .03, which is similar to 152.4-µm (6-mil) poly. A common assembly may comprise:
- moisture-retentive cladding like fiber cement, brick, or stucco;
- exterior insulation that acts as a vapor retarder similar to 152.4-µm polyethylene;
- oriented strandboard (OSB), which is semi-permeable at 2.0;
- kraft-faced fiberglass batts at a range of .3 to three or unfaced batts and 152.4µm polyethylene with a permeance rating of .05; and
- dryall with a permeance rating of three to 35, depending on the paint.
Unfortunately, this creates a moisture sandwich: moisture gets into the wall and is trapped between polyisocyanurate (polyiso) foam board on the exterior, and a 152.4-µm polyethylene on the interior with no ability to dry. It is a probable situation that is likely under construction throughout the country at this moment.
Consequences of a moist wall
Having moved beyond the era of leaky buildings, the industry is now facing a new set of challenges stemming from this era of airtight construction. Moisture, when trapped inside a wall cavity for an extended period, can cause building materials like wood, traditional paper-faced gypsum, and steel to eventually deteriorate or corrode. Even R-value goes down when insulation gets moist, and thermal performance is the reason the wall system was constructed to be airtight in the first place.
It is common knowledge moisture buildup can lead to health issues through mold growth that releases potentially harmful spores into the air. These airborne spores can cause occupants to experience acute health and comfort issues that correlate with the time they spend inside the building.
Architects want to design wall systems that are able to dry; otherwise, these types of product deterioration scenarios and mold growth are likely. Since the moisture is within the wall, the issues are unlikely to be found until it is too late. This is when the large and expensive problems like mold remediation and litigation arise.
It is possible to design a continuous airtight wall system that also exerts moisture control.
A great first step is to focus on the management of air and moisture flow through the building envelope. Continuous air barriers and smart vapor retarders are able to address both airflow and manage the moisture profile of the exterior wall cavity. This helps minimize and limit the risk of moisture-based building issues while adding minimal additional labor to projects.
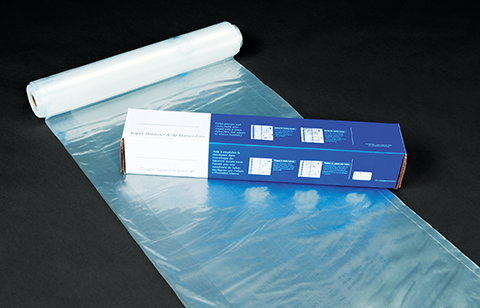
Changing the drying potential of a wall
Poly vapor retarders are part of the traditional approach to keeping moisture out of a wall, but as mentioned, moisture seems to find its way in, one way or another. Historically, building codes have classified vapor retarders as having a water vapor permeance of 1 perm or less when tested in accordance with the ASTM E96 desiccant/dry cup method. As such, most products are only evaluated under dry conditions. Products like polyethylene film or aluminum foil have low permeance values that remain constant between dry and wet conditions.
Rather than contributing to a healthy wall cavity, vapor retarders can often become part of the problem. These low-perm materials slow the rate of water vapor diffusion, but do not totally prevent its movement. As water vapor moves from a warm interior through construction materials to a cooler surface, the water vapor may condense on these vapor retarders as liquid water that could damage the building. It is for this reason smart vapor retarders are needed. Not only do they retard moisture penetration, but they also increase the potential for materials to dry. The wall’s drying potential must always be greater than the wetting potential so the amount of moisture getting into the system is less than the amount of moisture that can leave it.
Smart vapor retarders, though not required by code, are the better approach to a healthy wall assembly in many regions. Fortunately, building codes are continuing to evolve and adapt; it is important to use progressive solutions that also actively manage conditions within the wall assembly. Design professionals should strive to build beyond current practice—selecting adaptive solutions like smart vapor retarders can be the better practice in various situations.