by Steve Weyel
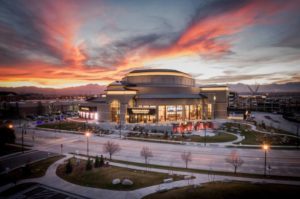
Stage wizardry is on full display at the newly opened Hale Centre Theatre—officially named Mountain America Performing Arts Center—in Sandy City, Utah. The $80-million theater measures 12,356 m2 (133,000 sf) and includes two stages with seating for 1368 patrons. The Centre Stage has 901 seats, and the Sorenson Legacy Jewel Box Stage can accommodate 467 people.
The former is the signature component at the Hale Centre, and is one of the most technologically sophisticated auditoriums in the world. Utah-based Beecher Walker Architects worked with Tait Towers and the Hale Centre’s leadership to create an entertainment facility with the stage as the jaw-dropping centerpiece.
The oval-shaped stage incorporates 47 axes of motion using more than 130 motors for hoisting, lifting, sliding, and revolving. The main portion of the stage consists of four quads that rotate, ascend, and descend, as well as work independently. Each of the four sections—called voms—is hoisted by two supporting lifts. A center column mounted on the stage can revolve in either direction and is capable of six rotations per minute.
When lifts supporting the four-section main stage descend, two 20-ton crescent lifts bring in a slip stage, allowing for uninterrupted performances. The crescent lifts are independently controlled and move at a rate of 1.2 m (4 ft) per second. Performers never have to use blackouts because the stage can transform right in front of the audience.
The specialized stage flooring includes a 25-mm (1-in.) base layer of plywood, topped by 6.35-mm (¼-in.) plywood, which can be painted and textured for each show. Stage and floor components were constructed in London by Tait’s engineers and shipped to the United States.
The 177.5-m2 (1911-sf) stage, which is 15 m (50 ft) in diameter, can descend as far as 8.5 m (28 ft). It is encased within 0.61-m (2-ft) thick walls extending nearly 18 m (60 ft) into the ground, and is supported by a 1.2-m (4-ft) slab and 40 piles. Due to the high water table in the area, construction teams drove piles as far as 27 m (90 ft) into the ground. In all, the structure is supported by 225 piles. The stage also includes a structural steel frame and moves with chains powered by more than 130 motors.
Another interesting component of the Hale Centre is the double-leaf terrazzo doors that allow crew members to lift equipment up to the stage. The doors are covered with a fillable pan accepting any type of architectural flooring. They also have an extruded aluminum frame with built-in anchor flange around the perimeter, as well as stainless steel hinges and slam lock with fixed interior handle. Compression spring operators enclosed in telescopic tubes make for easy one-hand operation.
Architects finished the rest of the Hale Centre with a variety of floorcoverings. The main lobby is covered with a patterned dark red carpet with a solid red border. Carpet was installed in several other rooms of the theater. Vinyl composition tile (VCT) and luxury vinyl tile were also employed.
From top to bottom, attention was paid to the tiniest details. The roof, for instance, includes acoustic smoke vents to limit noise intrusion. The vents feature a sound transmission class (STC) 46 acoustical sound rating and include 24-volt electric thermos latches. This is important because the theater is located directly in the flight path of an airport, and is also adjacent to a busy interstate.
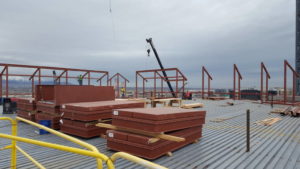
The vents also play a critical part in protecting the visitors. They include gas spring operators that open the covers in snow and wind, and also have built-in dampers to ensure smooth opening and eliminate the possibility of operational, roofing, or structural damage. The vents create a passive smoke ventilation system leading up through the loading level, which keeps the smoke out of the theater so everyone can exit safely.
The theater’s uniqueness extends overhead as well. Two overhead crane trolleys allow up to 16 independent pieces or performers to be raised or lowered while traversing or rotating. The trolleys traverse the 36.5-m (120-ft) span of the theater at 0.91 m (3 ft) per second. Pieces are picked up from storage zones and lowered into view of the audience. Each trolley contains eight hoists and can rotate in either direction at up to three revolutions per minute.
Four high-capacity winches on each trolley can extend all the way to a sub pit below the main stage, and can lift 453.6 kg (1000 lb). The winches can raise individual pieces or lock together to lift heavy props (e.g. cars). The fly loft where the trolleys are located is constructed with eight structural steel beams, welded and fabricated onsite.
The halls are brought together by a massing area where patrons can linger before the shows. An assortment of other amenities caters to theatergoers as well, including:
- expanded legroom in the seating areas;
- plenty of bathroom stalls in women’s restrooms;
- catering rooms; and
- a parking structure adjacent to the building so guests can enter the theater without worrying about snow or rain.
The front of the building includes a plaza where people can soak in views of manmade waterfalls within the plaza and the surrounding majestic mountain scenery.
Architects also took measures to ensure audio quality met the perfect pitch for all guests. A hearing loop technology allows patrons with cochlear implants and hearing aids to hear performers as the sound is projected directly to their devices using magnetic fields.
Layton Construction spearheaded the building of the Hale Centre, which required 7493 m3 (9800 cy) of poured concrete and 1800 tons of structural steel. If the building had been constructed completely above ground, it would extend 11 stories high. Construction began in September 2015 and required 417,130 working hours (the equivalent of nearly 48 years) to put all the pieces in place.
The Hale Centre has come an extraordinarily long way since its first opening in 1985. The original iteration was formed in a renovated lingerie factory in South Salt Lake with seats purchased from a movie theater, and painted green to match the upholstery fabric, which was the only color on sale. The sound system consisted of a cassette player placed near a microphone, and costumes were made from materials such as bedspreads and poster board. The first performance, I Came to Your Wedding, played to a paid audience of 25 patrons.
The center’s administrators decided to build the new facility because the theater had simply outgrown its space in nearby West Valley. Performances at the Hale Centre played to capacity audiences for 13 consecutive years before moving into the new home. The project was funded with a $42.7 million bond secured by Sandy City, with the remaining $37 million provided by donations. The theater started selling tickets for performances in 2015, making it critical the project finish on time. This year, it will host 10 shows offering more than 700 performances.
Steve Weyel is product manager with the BILCO Company and has worked extensively with roofers and builders in the U.S. construction market. Weyel has academic degrees in mechanical engineering, business, management, and marketing from the University of New Haven. He can be reached at stevew@bilco.com.