Basic factor considerations
The engineering design rules cover five basic mechanical factors:
1. Load distribution and magnitude
The uniform wind load acting on the product is assumed to be distributed in a manner depicted as a triangular (or in a combination triangular-trapezoidal) pattern across the framing members supporting glass or opaque panels. Diagrams within AAMA 2502 indicate the areas of glass to be considered as collecting and transmitting the wind load to individual members for a variety of window configurations. The total load acting on a member is calculated by multiplying the defined area of the glass or panels that it supports by the applicable design pressure for the building’s location.
2. Section properties
These include the area moment of inertia, the section modulus, and the bending moment. The behavior of a framing member of a given material with a specific cross-sectional configuration depends principally on two of these properties: a) the area moment of inertia, which together with its modulus of elasticity, governs deflection; and b) its section modulus—the ratio of moment of inertia to the greatest distance of the beam’s edge from its neutral axis—which governs stress. The bending moment (the resistance of a member to bending due to the application of external forces) is also a factor.
Section properties for many sizes of solid rectangles, square bars, round rods, square tubes, round tubes, pipes, standard structural shapes (e.g. channels, I-beams, wide flange beams, angles, and zees) as well as certain channels and tees are given in various, material-specific engineering texts. For example, one source of data on aluminum is the Aluminum Design Manual, published by the Aluminum Association.
3. Strength
This is defined by stress calculations for both tension and compression. The calculated stress cannot exceed guidelines in NAFS and/or other applicable industry standards for different framing materials. If not otherwise defined in the referenced documents, the material yield stress is subject to a minimum safety factor of 1.5 as the basis for allowable stress design.
4. Connections
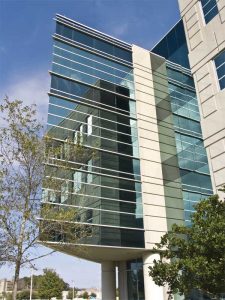
To ensure proper design, connections must be analyzed for tensile, shear, and bearing strength. The total strength in tension and in shear provided by the fasteners must be the same or greater than the tensile and shear loads at that connection. For further reference, single-shear strengths for screws and bolts of various alloys are given in AAMA TIR-A9-14, Design Guide for Metal Cladding Fasteners. Also, the capacity of fasteners can be calculated per AAMA 2501-20, Voluntary Guideline for Engineering Analysis of Anchorage Systems for Fenestration Products Included in NAFS.
Where the framing members are rigidly and securely fastened together, the assembly will act as one integral member. The fastening devices or welds connecting the members together must be strong enough to withstand the loads applied to them.
5. Deflection
Formulas are provided for figuring deflection and stress limits of simply supported beams, including the calculation of modulus of elasticity (which varies by material), for both symmetrical and unsymmetrical profiles. Formulas are also given for calculating the deflection of composite framing members such as thermally broken framing. In the case of composite framing members with integral thermal breaks, it is recommended they are tested per AAMA 505-17, Dry Shrinkage and Composite Performance Thermal Cycling Test Procedure, and analyzed per TIR-A8-16, Structural Performance of Composite Thermal Barrier Framing Systems.