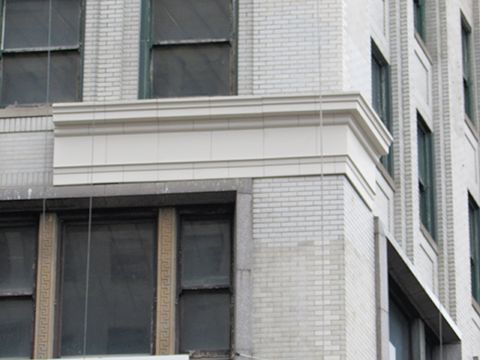
For the David Whitney Building, the 26 lion’s heads on the cornices were made by a slightly different method. The pattern was sculpted in clay by sculptor Sergio DeGusti. A silicone mold, taken from the clay, was used to make each of the bas reliefs, which were then cast into the panels that bear them on the building.
Each head is about 900 mm (36 in.) in diameter, with a 50-mm (2-in.) border framing it, for a total 1000-mm (40-in.) diameter casting. Each is approximately 50 mm (2 in.) thick, and weighs about 45 kg (100 lb). The terra cotta originals are estimated to have weighed 180 to 227 kg (400 to 500 lb) each.
To attach the water-tables and cornices, two strips of 2×6 lumber were anchored to the building. The edges of the FRP element fit over the top strip and under the bottom strip, and are fastened to the wood with screws. Most pieces—other than the sign atop the building—were light enough to be hoisted up the building on the swing stage, without the use of a crane, and then positioned and anchored by three or four men—two on the swing stage and others at nearby windows or on the roof.
Di Rita also notes that after the mockup was placed on the building, it remained in place for about a year before the permanent FRP water-tables were installed. At that time, he found it indistinguishable from the new pieces in color and texture.
The sign atop the building was made in three large panels, and was hoisted into place by crane. Each FRP panel has three horizontal strips of paired 2x6s attached inside, running the length of the panel. Anchored in the 2x6s are 16-mm (5/8-in.) stainless steel threaded rods, either 15 or 18 per panel, depending on its size. The rods stick straight out the back of the sign.
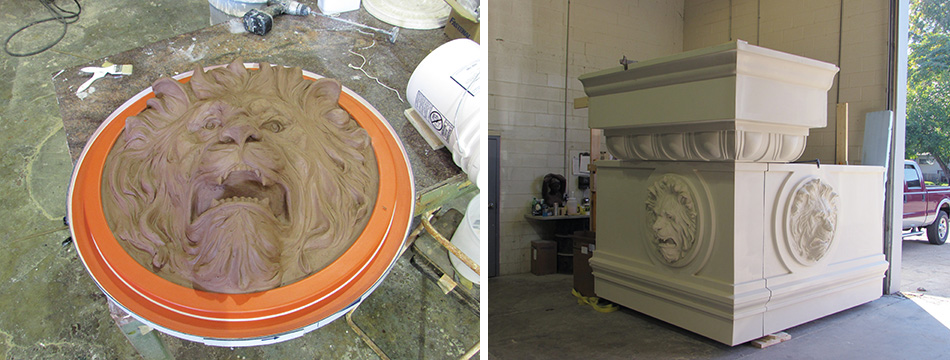
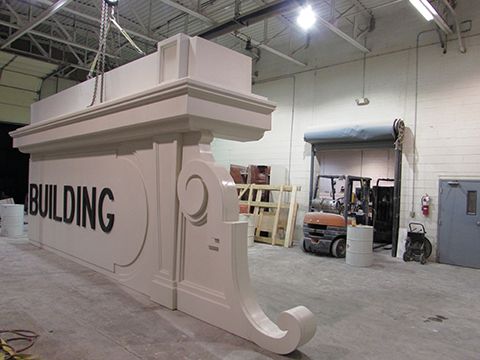
The fabricator provided the contractor with templates of the exact positions of the rods, allowing the contractor to drill anchor holes in the masonry wall of the penthouse atop the building. Each piece of the sign was held aloft by the crane and the rods aligned into the holes in the wall—a tricky procedure, but one performed successfully due to both the templates’ accuracy and the contractor’s skill.
David Di Rita’s recollection of the installation of the sign underscores the emotional aspect of architectural restoration. For him, it was a transformational event.
“That sign went up like three pieces of Lego, all in about three or four hours. It was the most amazing thing I’ve ever seen,” he said. “Three large pieces go up and just slide into place, and instantaneously restore this huge sign. It was such a dramatic change to the look of the building in a single day.”
Architect Rabe believes that, with both the cornices and the sign, the fiber-reinforced polymer composite restorations fulfill the design intent.
“We feel that what is up there now best represents the old version,” she said.