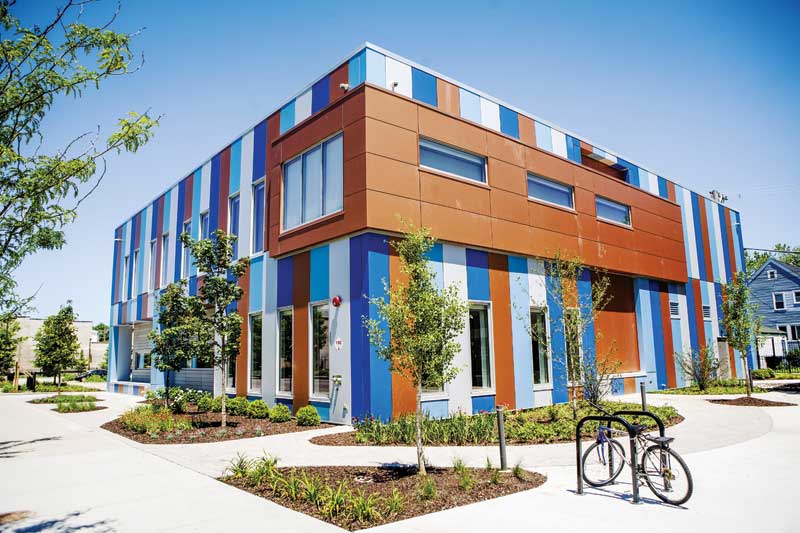
Photo © Kyle Flubaker Lenspeak Photography
The simplicity of using IMPs comes as the result of two main points:
- All the materials that make up IMPs are vapor-impermeable and therefore will not store water.
- The application details for IMPs have the air, water, and vapor barriers on the liner side inboard of the insulation. This arrangement of barriers has been dubbed the “works-everywhere wall” or the “perfect wall” by noted building consultants. (Lstiburek’s “Joseph Haydn Does the Perfect Wall,” was published in Insight from Building Science Corporation in December 2015.)
Airtightness up to 0.03 cfm/sf at 300 Pa (6.24 psf), and watertightness up to 718-Pa (15-psf) pressure difference can easily be attained. These are the performance characteristics of high-end architectural walls.
Many additional benefits are gained from the metal facers bonded to the insulated foam core of the IMPs. The panels:
- create an IMP structural composite able to span 2.4 to 3 m (8 to 10 ft);
- have formed side-joints that allow for easy engagement between panels and panels, and panels and windows—thus engaging the factory- and field-applied seals;
- possess the four critical barriers connected from the exterior as the product is installed (backside fastening is not typically required);
- enhance fire performance by protecting the foam core from direct fire impingement (IBC Chapter 26 requires compliance with National Fire Protection Association [NFPA] 285, Standard Fire Test Method for Evaluation of Fire Propagation Characteristics of Exterior Non-Load-Bearing Wall Assemblies Containing Combustible Components, and many other test protocols for wall assemblies that contain foam insulation);
- mitigate foam aging;
- enhance thermal efficiency through thermal breaks between the face and liner metal facers; and
- offer water management features in the side-joints, minimizing water buildup and entrapment within.
As mentioned, many manufacturers have pre-designed and tested integrated accessories like window systems that engage with the IMPs.
Insulated metal panels are available in a variety of shapes and sizes—50-, 75-, and 100-mm (2-, 3-, and 4-in.) thick insulated metal panels are available in widths from 254 and 1067 mm (10 and 42 in.), and lengths up to 9.1 m (30 ft). They can be used as a finished product or as a backup to alternate cladding types such as brick, metal, or terra cotta. Products have a prequalified performance for air, water, vapor, and thermal protection. Sealing is straightforward and can be installed from the exterior side in one pass. Quality control on all aspects of the application is important.
Quality assurance
To ensure properly detailed, manufactured, and installed products, numerous checks should be implemented along the way. Since many of the key components are factory-assembled, there is less chance for variation as compared to a traditional, multi-component wall. Nevertheless, there should be clear prescribed quality checks.
For example, mockup testing for air, water, and structural performance helps define standard details as well as product performance. As well, high-performance manufacturing equipment helps make the correct-shaped product, while trained installers increase the likelihood those panels are then installed to the proper tolerances.
In-place field tests using the AAMA hose method (i.e. 501.2, Quality Assurance and Diagnostic Water Leakage Field Check of Installed Storefronts, Curtain Walls, and Sloped Glazing Systems) helps identify any missing link in the design, manufacture, and installation process. This, and the other aforementioned checks, should be spelled out in the project specification in
an effort to ensure high performance levels.
Conclusion
The design of a building envelope with multiple components can be complex and dependent on many variables. Simpler solutions using insulated metal panels as the single component to establish high-performance levels for water, air vapor and thermal control layers or barriers are available.
In cases where the finish material needs to be another cladding system, the benefits gained from the exposed IMPs can still be realized using insulated composite backup panels, with the desired cladding applied over top. In addition to the factory and detail standards quality already in place, field testing should be specified and performed as a final check to ensure high performance.
Keith Boyer, PE, is the director of architectural wall technology for Centria. He is involved in long-term product development for architectural wall products, support of major projects, and training. Boyer has served on several ASTM committees for standing-seam metal roofs, and has recently been involved with an American Architectural Manufacturers Association (AAMA) task force to develop testing protocols for rainscreen wall systems. He has also been active with the Metal Construction Association (MCA) foam panel council. Boyer can be reached at kboyer@centria.com.