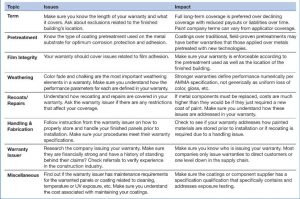
Image courtesy PPG
Corrosion resistance
The two main components to corrosion resistance are humidity and salt spray resistance. For this reason, metal coatings manufacturers do not offer warranty coverage in severe marine or coastal environments.
Although many coatings manufacturers test for cyclic corrosion according to ASTM G85, Standard Practice for Modified Salt Spray (Fog) Testing, Annex 5A, “Dilute Electrolyte Cyclic Fog/Dry Test,” procedures, it is a minimum standard that is not likely to accurately predict the long-term performance of a coating in a coastal environment. Many coatings manufacturers use accelerated weathering data to substantiate the corrosion resistance of their products. However, the tests may not provide confidence a costly failure of installed components will not occur. The only true indicator of corrosion resistance in humid salt-air environments is long-term exposure to them in the real world.
Additionally, coatings manufacturers may also limit warranties based on a project’s proximity to steel plants, power stations, oil refineries, chemical plants, paper mills, and other industrial settings where potential for exposure to environmental hazards is high.
Warranty coverage
Warranty documents address three major performance variables that are key indicators for long-term performance: film integrity, chalk, and color fade.
Film integrity
Film integrity addresses a coating’s interlayer adhesion strength as well as its ability to bond to pretreated metal substrates over their lifetimes to resist cracking and peeling. If a warranty covers adhesion, it is appropriate to ask about restrictions related to the type of pretreatment used as well as the performance environment of the finished project.
Chalk
Chalking results when the pigments in a paint film break down and turn to powder. Once that happens, rainfall can begin to wash the coating away and expose the surface of the underlying substrate to erosion and failure.
Color fade
Color fade change is measured on an exposed painted surface that has been cleaned of surface soils and chalk, and then compared to corresponding values measured on the original or unexposed coated surface.
Inferior coatings that fade and chalk must be repainted at the jobsite, a costly development that has negative environmental impacts.
Comparative testing and measurement standards for fade and chalk are published in AAMA 2605, 2604, and 2603 voluntary specifications. For more details on industry recognized weathering standards published by AAMA and Qualicoat, see Figure 1.
Warranty conditions
Warranties address specific conditions in detail or provide instructions to which various participants in the supply chain, including applicators, fabricators, and building owners, must adhere to ensure the finish quality and long-term performance of a coatings system.
For example, applicators must clean and pretreat metal substrates to AAMA specifications before they apply coatings to a metal substrate. They are also required to thoroughly document the application process for all paint runs on every project.
Fabricators and building owners must follow a different set of procedures to make sure coatings are not damaged while metal components are being installed and to ensure coatings perform as intended throughout the life of a building. These procedures detail how to properly store and care for coated metal components before they are assembled and installed, and how to clean and maintain them once construction is complete.
The following are some of the limitations and conditions coatings manufacturers commonly include in warranty documents.
Limitations: Non-uniform weathering
Coatings warranties usually protect against claims related to unequal sun exposure, which may cause coatings to weather at different rates.