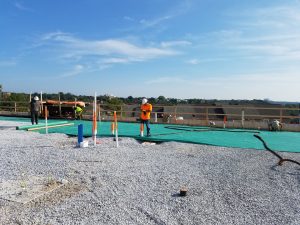
Photo courtesy Vapor Mitigation Strategies
by Wesley Robb
As is the case with many buildings, a national chain of early childhood education centers chose the location of its Washington D.C. project on a site known to have soil and groundwater contamination as a result of the property’s former uses.
Previous activities on the site—conducted by a governmental agency—required the installation of underground storage tanks (USTs) containing diesel fuel. The existence of these tanks was suspected due to the conclusions of an environmental site assessment (ESA), also known as a Phase I Site Assessment, which is routinely done as part of the due diligence process in property transfers. A subsequent sub-surface soil investigation, known as a Phase II Site Assessment, indicated the ground and groundwater at the site was contaminated.
This type of contamination, better known as vapor intrusion, can have serious consequences on a building’s indoor air quality (IAQ) if left unaddressed. Vapor intrusion is the hazardous, potentially harmful migration of chemical vapors into a building from soil and groundwater contaminated by petroleum products or volatile chemicals. The negative health effects (e.g. lung cancer, decreased kidney function, damage, and cancer, heart failure, and ischemia) caused by these chemical vapors can be experienced by both the building’s occupants and their offspring. Unfortunately, vapor intrusion cannot be detected by sight or smell, so being conscious of the issue is very important. Additionally, future litigation where building owners are held responsible is a cause for concern.
Luckily, awareness about vapor intrusion has grown in recent years. Recently the Environmental Protection Agency (EPA) specified vapor intrusion as a potential pathway in its Superfund Program, designed to fund the clean-up of uncontrolled hazardous waste sites. The program resulted from the passage of the Comprehensive Environmental Resource Conservation and Recovery Act (CERCLA) in the early 1980s. Placing vapor intrusion on the list of pathways eligible for monetary assistance underscores EPA’s conviction sites with vapor intrusion potential should be addressed to protect human health and the environment.
At the Washington D.C. site, the USTs and diesel-contaminated soil were removed. However, since this location was to be a child care and early childhood education center for the neighborhood, the specifier included a vapor intrusion mitigation system in the project’s design plans to ensure the safety of the buildings’ occupants.
The vapor intrusion mitigation system was a combination of two elements—an active pump sub-slab depressurization system (SSDS) and a spray-applied asphaltic vapor barrier (AVB). The SSDS consists of two square subterranean concrete vault “pits” with slotted openings at the top, and piping running from the pits to risers penetrating the sub-floor. The risers that are connected to an on-the-roof service pumps soil gas accumulated below the building’s sub-slab, out and away from the structures.
Both vapor pits were installed as part of the general contractor’s pre-vapor intrusion mitigation installation commitment to provide for large-scale construction items prior to the finishing of the SSDS and AVB by vapor intrusion mitigation installation specialists.
The contractor accomplished pre-installation work including construction of the vapor pits, all plumbing and electrical penetrating uprights, and concrete collars around clustered penetrating uprights, as well as smooth-grinding of rough surfaces for attachment of AVB to the foundation, and compacting the sub-slab gravel bed.
The installers of the vapor intrusion mitigation system completed the piping from the vapor pits to the risers for the SSDS and installed the AVB and four vapor monitoring wells for regular monitoring of the slabs under the buildings for contaminants.
The AVB was installed using a three-layer approach. First, a polypropylene tarp was rolled out, tailored to fit around the vertical uprights, and sealed to either the foundation or uprights with a chemically-resistant asphaltic core material at the center of the three-layer AVB.
Then the asphaltic core material was sprayed over the remaining tarped area. Finally, a layer of tarp was installed to provide protection to the vapor barrier itself since metal rebar and concrete were arranged on top.
The installation was observed and inspected by a trained and certified personnel. The inspection included a coupon thickness test to verify the specified thickness of the vapor barrier, and a smoke test to ensure the integrity of the finished system. The installers documented these tests and provided the materials to the manufacturer to enforce the warranty accompanied by these products.
The project required approximately 1765 m2 (19,000 sf) of vapor barrier. From start to finish, the process took approximately five days to complete.
Wesley Robb is the director of technical strategies and applications at Vapor Mitigation Strategies, a Wellington Environmental Company. He has 29 years of environmental field and laboratory experience, including several years of soil vapor sampling and analyses. Since joining Wellington in 2004, Robb has managed onsite activities of various kinds, including underground storage tank removals, soil remediation, Phase I investigations, and vapor/soil/groundwater sampling. He can be reached at wes@vapormitigationstrategies.com.