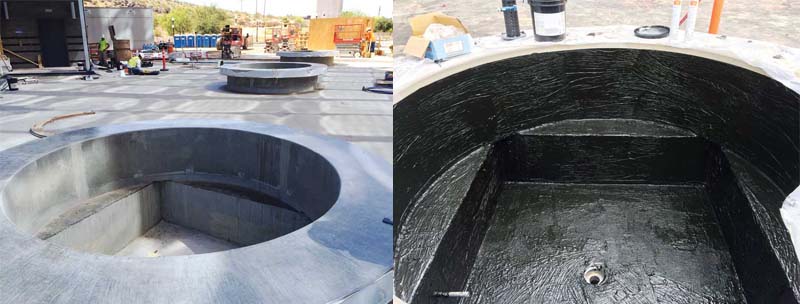
Waterproofing materials
Perhaps the most important layer in the ‘cake’ is the waterproofing system itself. The system may be constantly wet, so it must resist leakage, hydrostatic pressure (often in the form of ponded water), and fungal growth. It must also be long-lasting, as repair costs are high. Resistance to chemicals is an important consideration. If there are plantings on the deck, chances are there will be fertilizers. Certainly, there will be cleaning products—and there is always the possibility someone walking over the deck will spill a soda.
Typically, the waterproofing membrane is adhered directly to the plaza deck. The deck surface provides a stable substrate and helps prevent leaks from migrating laterally. There are instances when the membrane can and should be loose-laid—for example, if there is no solid surface to adhere to, or if there will be exceptional deflection or movement in the deck. This technique is also very fast, making it ideal for transportation projects.
Some companies manufacture grid systems that simplify maintenance and repairs by allowing removal of certain sections of the assembly. These are ideal for some types of projects, but there are disadvantages, such as the cost of installation and the complications of sealing the edges of the grid.
The waterproofing should be highly vapor-resistant. A deck with occupied space beneath needs to control vapor drive from below as well as water from above, so the membrane is also the air/vapor barrier. In a wall assembly, permeable versus impermeable is worth debating, but in this case, the longevity of the plaza deck hinges on keeping moisture out.
Typical waterproofing systems include hot rubberized asphalt, modified bitumen, and cold liquid-applied membranes. Single-ply thermoset (e.g. ethylene propylene diene monomer [EPDM]) and thermoplastic (e.g. polyvinyl chloride [PVC] and thermoplastic polyolefin [TPO]) waterproofing membranes are also popular due to their low vapor permeance and water absorption. Each system has its own advantages and disadvantages, all beyond the scope of this article.
Cold-applied liquids
One group of membranes worth a look is cold-applied liquids. Introduced about 40 years ago, these materials are fairly new to the market, at least compared to old reliables like hot rubberized asphalt and modified bitumen. Made variously of polymer-based combinations, such as polymethacrylate (PMA), polymethyl methacrylate (PMMA), polyester, polyether, or polyurethane, they may go on alone, but most often they are paired with a reinforcing fabric like fiberglass or polyester for extra strength.
Some variations have had problems. There are specifiers who prefer the sheet variety because they are assured they will go on at the proper thickness; liquid variations require perhaps greater trust in the skills of the applicators. Additionally, the formulas are not particularly UV-resistant.
Liquids still offer some advantages, including the fact there are neither seams nor opportunities for fishmouths and wrinkles. These products go on quickly and easily; they can often be applied over green concrete, saving time and doubling as a curing agent. They may also cover asphalt, metal, and wood surfaces, as long as they are clean and free of coatings and sealers. One should check with manufacturers on how to apply liquids in cold temperatures. (Most require the surface be frost-free.)
Some formulations are low in, or free of, volatile organic compounds (VOCs,) solvents, and odors. All of these are an issue with plaza decks—they are often close to occupied space and HVAC systems. A worst-case scenario is an HVAC system picking up VOCs from a membrane and transmits them through the building.
Liquids often double as flashing materials. Working well in planters, they are highly adhesive and stick well to drains and joints. The joints in the substrate need to be pre-detailed with the material, sometimes with a reinforcing mesh, prior to the full membrane application. Most of all, it is convenient to use one material for so many different purposes on one jobsite.
These durable liquids do not melt in hot weather or crack in extreme cold. They may be double- or single-component, with advantages and disadvantages to either option. The two-component variety tends to have a longer shelf life, and some professionals consider them more durable. However, single-component liquids are easier to apply, and avoid problems with incorrect mixing.
Regardless of which membrane is used, all the components that follow—from flashing materials to caulks—should be compatible with the membrane and not cause delamination or debonding.