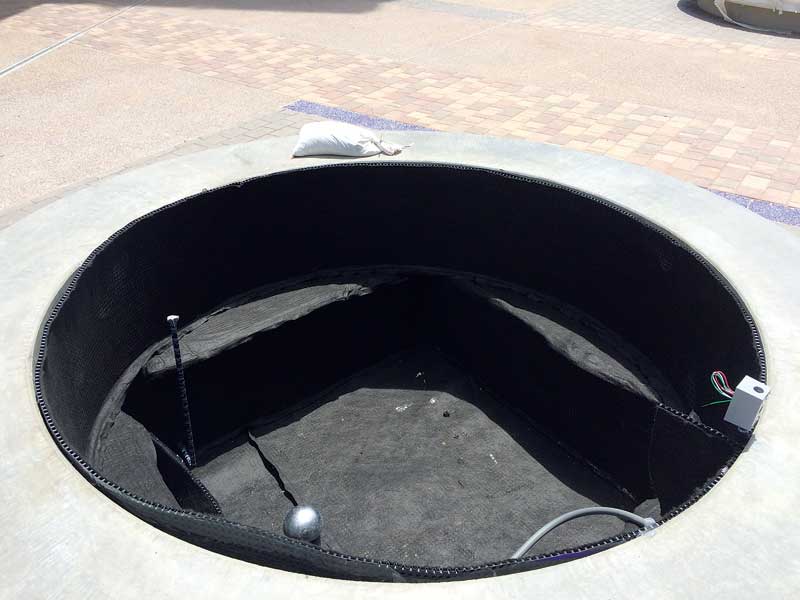
More layers and more details
After the membrane and flashing is installed and inspected, there must be flood-testing in accordance with ASTM D5957, Standard Guide for Flood-testing Horizontal Waterproofing Installations. All drainage locations have to be sealed before the test. After, sources of leaks are repaired, with the tests repeated until everything is sealed.
Protection of the membrane is mandatory. The protection course must resist crushing and transfer of concentrated point/impact loads to the membrane. This layer may also serve as a relief plane so expansion and contraction of the wear surface does not pull the membrane along and cause stress points and tears.
Sometimes the drainage mat alone will suffice for protection. It should be installed fabric-side-up, and must be continuous to prevent clogging. In other cases, the insulation may double as a protection course, which is not ideal. A purpose-designed protection course, often an asphaltic or cementitious board, is always the best idea.
In some parts of the country where rainfall is minimal, the drainage mat is located only in critical areas or skipped altogether. In these instances, the protection course alone sufficed, while in other cases, a protection course and a drainage mat are used in tandem. This aspect of the deck is left to the discretion of the designers.
When it comes to insulation—a very good idea to protect the assembly from thermal extremes and to insulate occupied spaces below—extruded polystyrene (XPS) is often the material of choice. It offers high compressive strength to protect the membrane and drainage layer. It should not be a substitute for a protection course, though it is often used as one in particularly mild climates. Further, seams in insulation layers should be staggered. The insulation layer is likely to be saturated if it is not drained from above and below.
The selection, specification, and design of traffic-bearing surfaces are the purview of the designer. Typical choices include concrete pavers, paving stones, rubber play tiles, cast-in-place concrete pavement, and artificial turf. However, the wear membrane, which may be colorful or convey a sense of nature or even direct traffic, is important to the deck’s function.
These systems are categorized as accessible or inaccessible. In the former, the wearing course is removable—pavers that rest on pedestals, for example. Inaccessible systems include a concrete or asphalt slab, or mortared pavers. Fountains fall into this category. The problem with inaccessible systems is they are expensive to repair, often requiring demolition.
The wear surface can aid or impede drainage. Accessible systems allow water to percolate through, but may also block flow. For example, sand and small stones can release from around larger stones, flowing into drains.
Concrete wear layers present another problem—rebar, wire mesh, and other elements can come into contact with the waterproofing membrane and damage it. Careful, supervised installation is the solution, ensuring the membrane is preserved for at each step.
Critical details
How the ‘layer cake’ of materials is detailed—at the expansion joints, flashings, and where they meet different materials or vertical elements—determines the deck’s long-term performance.
The waterproofing is flashed against walls, as well as other termination points such as planters, fountains, and other vertical elements. Leaks occur most often at the flashing, not within the field of the membrane. The membrane must adhere tightly to all drains and flashings. Flashing must extend above the height of the final wear layer. If the overburden is above the top edge of the flashing, water can back up into the wall system. Ideally, flashing should be accessible for maintenance and repair wherever possible. Drains also need to be accessible for cleaning, maintenance, and repair.
Similarly, control and movement joints require careful planning ahead of the installation. Ideally, joints are located on raised curbs above the level of the waterproofing membrane. Better still, those joints should be in accessible locations, so they can be fixed.
Accessory items (e.g. electrical conduits, irrigation lines, and piping) should not be attached to a waterproofing system. It is best if these are also shielded from the membrane and accessible for repair.
Planters should be isolated from the membrane system and the sides of the building, if they abut. Many manufacturers require a root barrier—a good idea over any material, though many new cold-applied liquids do not require them. (For best practices, refer to the National Roofing Contractors Association’s [NRCA’s] Vegetative Roof Systems Manual.)
Railings, bike racks, planters, bollards, light poles, and other items are installed over the membrane system, and not integrated with it. This is easiest when the wear surface can support them, as in the case of a cast-in-place concrete slab.
Designers can find more information by consulting ASTM E2266, Standard Guide for Design and Construction of Low-rise Frame Building Wall Systems to Resist Water Intrusion. Further guidance is available through many other resources, including the aforementioned NRCA and NIBS’ Whole Building Design Guide.