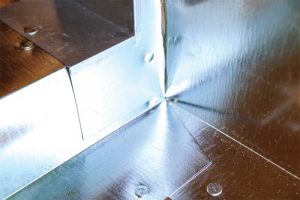
Further, drain mats should only be used in settings where slope is designed into the deck. Employing mats in a corridor without a slope only creates a subsurface ‘lake’ in which water can reside. This subsurface water causes efflorescence in the concrete and eventually results in premature failure of the waterproofing system.
Improperly placing railing mounts
The best way to protect a waterproofing system is to mount the railings on the face of the balcony below the T-bar. Many designers do not like the appearance of this method, and it still poses its own unique problems with water infiltration at the mounting holes. Surface mounting railings, especially the supporting members along the length of the railing, can be done safely and cost effectively. However, a few principles should be kept in mind when designing the balcony, including:
- stanchions embedded in the concrete should be placed at least 76 mm (3 in.) from the edge of the balcony;
- stanchions should be no closer than 203 mm (8 in.)from any wall or column; and
- every embedded railing stanchion is an opportunity for a leak, and therefore should be used as sparingly as possible.
Ignoring these guidelines creates difficulties during waterproofing as it becomes impractical (if not impossible) to properly lap and seal all the components (Figure 1). Apart from adding unnecessary cost, there are simply too many elements to fit into a small space while still guaranteeing proper installation and performance of the waterproofing system.
Incorrectly designed scuppers
While scuppers effectively drain water from the surface of the concrete, they should also capture and evacuate the water draining from beneath the concrete. The waterproofing system should terminate into the opening of the scuppers so water flowing down the surface of the waterproofing (below the wear surface if they are unique) has a path to escape.
Cricketing balconies with parapet walls
Balconies enclosed by a wall are a special amenity and enhance the visual appearance of a façade. Even with proper sloping of the deck, the water beneath the concrete will flow into an intersection with the wall before reaching the scuppers. Proper cricketing of the balcony deck and an adequate number of scuppers are crucial in this type of design.
Using lightweight concrete
Many specifications refer to balcony concrete as ‘lightweight.’ Normal pea gravel ‘hard rock’ concrete at 20,000 kPa (3000 psi) is adequate for most private balconies and breezeways. At a 50-mm (2-in.) thickness, this only adds 11 to 13.5 kg (25 to 30 lb) of dead load per square foot to the structure. Lightweight concretes rely on aggregate too large for most small concrete pumps used in the market, thereby driving up the cost of the concrete exponentially due to the expense of materials and pump rentals. Using lightweight concrete also increases the difficulty of achieving a good broom finish, resulting in a less attractive finished product.
Replacing galvanized metal flashing
In recent years, some manufacturers have introduced a 2.6-mm (105-mil) membrane that, in theory, can be used to eliminate the need for galvanized L-flashing to transition from vertical to horizontal surfaces. In practice, this transition is often complicated by the fact framing is not finish carpentry. There will always be gaps of 13 mm (½ in.), or more, at this critical change of plane, leaving a 2.6-mm membrane to bridge the gap for the life of the balcony (Figure 2).
Galvanized wall flashing provides a clean, strong substrate to bridge these framing gaps and eliminates the risk of membrane failure due to the presence of a large void. Finally, many are under the impression galvanized flashing is a waterproofing layer. It is not. It is merely a substrate to make the transition at changes of plane. When water reaches galvanized wall flashing behind the membrane, the war is already lost.
Creating natural wood columns
As waterproofing wraps natural wood columns when they are completed, they must be covered with a decorative finish at the base. The big challenge here is wood columns will almost certainly split and crack as they age, allowing water to permeate behind the waterproofing wrapped around their bases. Therefore, columns should always be clad with finishes to withstand weathering and limit penetration of the structural column of the elements.
Incorrect product specification
Multifamily projects often use a variety of products from multiple manufacturers to complete a waterproofing system. This creates its own set of difficulties as care must be taken to ensure every component is compatible with other specified products. If and when failures occur, the finger-pointing game will ensue among the various manufacturers. Reaching a final determination for the cause of the problem will be difficult as each party seeks to limit its exposure. This can be addressed by finding a manufacturer that can offer a complete turn-key system backed by a warranty, not just product warranties for the individual components used.