Sequencing mistakes
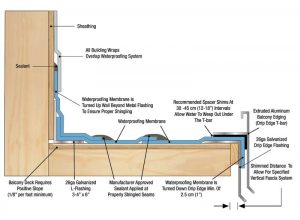
A perfect design on paper still needs to be implemented correctly in the field to ensure the system performs properly. Through experience, this author has found the following are the most common causes of failures. Thankfully, all of them can be corrected with consistent field training and attention to detail.
Pre-flashing doors
Multifamily builders and subcontractors have long employed the practice of installing a partial waterproofing system in patio doors and along walls for a few very good reasons. It allows them to set the doors more quickly and allows the siding and cornice work to commence in a timely manner. However, this practice is the single most detrimental waterproofing element on the market and must stop.
The foundation of any good waterproofing system is eliminating reverse laps in the membrane. One must make gravity do the work or it will work against the project goals. ‘Pre-flashing’ prohibits the membrane on the deck from being turned up the walls so it properly creates a double barrier along the balcony perimeter. If the deck membrane wraps up the walls and the wall membrane laps down properly over it, even a wrinkle in the wall membrane will not result in a failure because the water simply cannot climb the wall behind it (Figure 3).
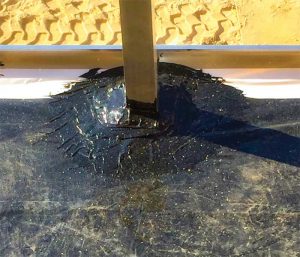
The absolute best practice is to develop a turnkey strategy to balcony waterproofing and concrete placement. Balconies should be fully waterproofed, flood tested overnight, and receive concrete the next day. This is a winning formula this author has followed for several years, and it has paid immeasurable dividends. Failure rates have plummeted to almost zero in this author’s experience.
Excessive use of sealant
Most of the time, thick gobs of sealant are hiding a problem. Used properly, mastics and sealants add a ‘belt and suspenders’ to good waterproofing. When contractors bury an area with a thick bed of these materials, they are indicating they are uncomfortable with how the area was designed, specified, or framed, so they decided to cover it with sealant for good measure (Figure 4).
The problem is adding more mastics and sealants will not address poor design or installation skill. Many such materials employed in waterproofing rely on the evaporation of a solvent to fully cure. Thick beds of sealant will skin over and trap the solvent, creating an airtight pocket as if it were still in the original package. This prevents a full cure of the material and allows displacement when pressure is placed on it by the installation of the wear surface. Sealants applied in a thin layer cure fully, will not hide any issues, and perform as intended.
Allowing extended exposure of the membrane
Most product manufacturers limit the amount of time the membrane can be exposed to ultraviolet (UV) light, with some products having an exposure recommendation as short as 14 days. It is important to be aware of these limitations and ensure precautions are taken to reduce the exposure to match this window. UV is not the only hazard one must guard against. Balconies on any jobsite receive traffic and often become a staging area for construction waste. This exposes the membrane to repeated foot traffic, nail-embedded lumber scraps, and sheet metal and pipes. This is also another reason for not pre-flashing balconies, as the practice jeopardizes the integrity of even the best products on the market (Figure 5).