Honoring proprietary methods
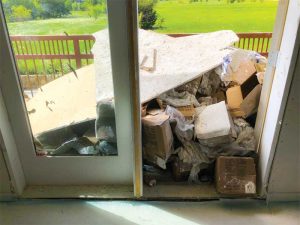
Frequently, value engineering happens on a project to meet budgetary demands. In waterproofing, some materials and methods are proprietary and substitutions for equivalents can be a challenge. Copycat products must be designed to work around the intellectual property of the original specification, thus running the risk of not offering the same level of performance. They also have the potential of opening up the project in question to patent-infringement litigation. While it is easy to target the waterproofing system to reduce costs, it is pertinent to note the high cost of cutting corners on an element is worth less than half a percent of the total cost of the project.
Flood testing every balcony
Even the best installers have bad days. Flood testing is not optional or difficult. It is the cheapest insurance one can buy. The cost of added time and effort to flood test 100 percent of the balconies on every job is offset by the claims that are prevented by this testing.
The November 2013 article, “Ensuring Balcony Durability: Waterproofing details that stand the test of time,” in The Construction Specifier cited a study in which 40 percent of 200 balconies inspected had undetected water damage. Flood testing is the only way to ensure the system is working as intended.
Maintenance mistakes
Well-built systems are still subject to damage over time from the elements and ill-informed maintenance efforts. Educating property maintenance teams on how to properly care for wear surfaces and be mindful of possible exposure points to waterproofing systems will help to ensure a long service life.
Frequent power washing
A common practice in property management is to use power washing to clean stains off of the concrete in corridors. Power washing allows water to ignore the effects of gravity as external pressure pushes it into any available opening. If power washing is necessary, the number of times it is done should be limited and design/construction professionals should be aware water will infiltrate the building envelope if the corridor is not fully waterproofed. Excessive power washing can also damage waterproofing when the water jet hits the membrane beneath the base trim or through cracks existing in expansion joints. Instead of frequent power washing, it is advisable to apply a sealer to the concrete so stains cannot penetrate.
Maintaining caulk and sealants
Door trims, joints in siding, electrical outlets, and light fixtures are sealed with caulk to keep water from getting behind the cladding. They should be inspected and maintained regularly. Often, a sealant failure at one of these points is mistaken for a balcony leak.
Conclusion
The design, installation, and maintenance mistakes identified in this article do not need to remain common. The frequency of leaks and failures experienced today are needless. It is possible to design and build functional, aesthetically pleasing, and leakproof balconies. The key is to pay attention to the details at every step of the process and not allow anyone to improvise a detail not shown in the drawings. Framing, railings, sealants, waterproofing materials, building wrap, doors, and drains work together to create a successful balcony project.
If the entire team, including architects and subcontractors, is not instructed on the proper means and methods, one will risk continued failures. General contractors (GCs) and subcontractors can be very inventive, and this well-intentioned problem solving can result in a repeated error in the waterproofing throughout a project. Good drawings and sequencing instructions alleviate the responsibility of design from GCs and subcontractors and drastically reduce the risk of systematic errors. The battle against water can be won, but it requires close attention to the details in the design process and a hypervigilant quality control (QC) program in the field.
John Igo is president of Formulated Materials, a company that both develops and markets multifamily waterproofing and floor underlayment systems and construction equipment through its corporate affiliates and a network of licensed and trained installers. Igo has been a product developer for the multifamily construction industry since 2004 and has developed a passion for leakproof balconies and floors that do not fail. He can be reached at info@formulatedmaterials.com.