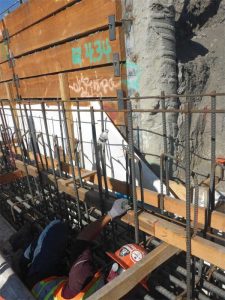
Waterproofing systems require more than this; the substrate should be dry, or at least free of liquid water on the surface during installation and often until concrete placement is completed. Waterproofing systems reliant on confinement and water-activated swelling are especially sensitive to substrate dryness. It is difficult and time-consuming to retroactively create a dry substrate condition suitable for the waterproofing system when the dewatering configuration has only accounted for structure stability. Additional costs can be surprising. The best time to define and coordinate waterproofing-related requirements for dewatering is when the excavation plan is being developed during the shoring scope. This provides an early understanding of costs and allows for coordination with waterproofing requirements.
Project conditions justifying permanent dewatering via pumping are rare, especially in new construction. In this case, sub-slab foundation waterproofing is likely not needed, although the sub-slab area may still require a vapor barrier. Permanent dewatering is expensive. The volume of water can be substantial, and is subject to treatment depending on the jurisdiction. Dewatering pump(s) should be redundant in the case of pump failure and backup emergency power must be provided for each pump. Slab pressure relief “blowouts” may also be required to relieve hydrostatic pressure, should the dewatering system fail.
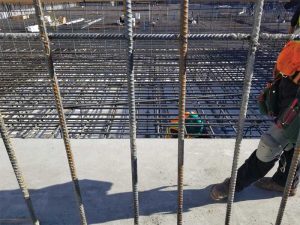
Mat foundations
Mat foundations are a common choice for below-grade foundations in the water table. Frequently, the soil at the basement level is strong in bearing and a deep foundation is not needed. Within water tables, a foundation of significant thickness is required to resist bending due to water pressure. Occasionally, deep piles are paired with mat foundations. This article focuses on mat foundations.
Protection slabs
Protection slabs can offer immediate protection and peace of mind for recently completed membranes. The contractor can focus on completing rebar placement and move around the excavation with less worry about backtracking waterproofing repairs during the critical period of completing rebar and concrete placement. The primary concern during steel placement is damage to waterproofing that becomes difficult or infeasible to access due to congested reinforcing (Figure 2). While not as reliable from a waterproofing standpoint as a protection slab, a waterproofing membrane below a large mat foundation may lend itself to post-rebar-placement repairs if the contractor can provide the waterproofing installer access the waterproofing through the reinforcement (Figure 3). It is important to note that even these large mat foundations may have localized rebar congestion (Figure 4) near elevator core depressions, or at the base of columns and shear walls. The contractor should be aware of code requirements for this confined access.
In consideration of settlement, the geotechnical engineer should also determine whether the protection slab needs to be attached to the underside of the structural slab in any case. The primary argument against a protection slab is the cold joint introduced between the protection and foundation slabs creates a path for water migration. A swelling sheet membrane (such as bentonite) or a network of post-construction, grout-injected water stops should be used to limit leakage. Protection slabs are not inexpensive. Significant expenses include the cost of deepening the excavation by the thickness of the protection slab and the price of the slab and waterproofing measures highlighted above.