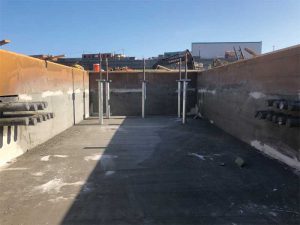
Lateral load transfer is accomplished by the socketed connection. The connection is therefore not directly reliant on concrete-to-concrete engagement between the horizontal top of the pile and the cap for lateral load transfer, which allows for a smooth, self-leveling epoxy grout to be placed between the connection (Figure 9). This epoxy grout has a compressive strength exceeding the concrete, which provides for vertical load transfer, and is also water-impermeable, providing a tie-in for the adjacent waterproofing. The designer should be aware this type of epoxy grout is not always provided by the waterproofing manufacturer and may need to be sourced separately. While not a single-source system, waterproofing warranty can remain intact with diligent coordination with the waterproofing manufacturer.
Additional waterproofing considerations must be verified in advance of excavation to properly set the pile head elevation. Mud and protection slabs will influence the pile head elevation and/or the excavation depth. Waterproofing upturns often require more than 76 mm. These items must be discussed with the project’s structural engineer.
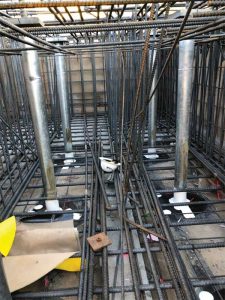
Crane foundations
A deep basement usually corresponds to a large superstructure, which is commonly constructed with the aid of a tower crane. The tower crane is temporarily supported for its construction service life, so its foundation pad is not always designed to be integrated with the primary structure. In this case, the waterproofing tie-in and dewatering must be coordinated with the crane pad installation. A sufficiently long waterproofing tail should extend beyond the edges of the crane pad within the mat foundation or slab-on-grade. This clearance must be coordinated with the crane operations, concrete placement plan, and must also allow access for the future waterproofing tie-in to the balance of the below-grade waterproofing system. The designer may specify additional protection measures for this exposed tail, such as plywood, with special attention paid to waterproofing systems reliant on water-activated materials, such as bentonite or modified polymers. From a waterproofing perspective, the most straightforward approach is to connect the crane and primary foundation and provide continuous waterproofing underneath.
Concrete wall placements
Traditional cast-in-place concrete is formed on all sides to confine it. Shotcrete is pneumatically applied at high velocity to the open face of the rebar cage against the shoring wall and waterproofing membrane. Shotcrete concrete is inherently more porous and has larger voids compared to cast-in-place concrete. Voids can be acceptable from a structural performance standpoint, although they create pathways for water travel in the event of a breach in the waterproofing membrane and will increase the rate of leakage. Water moving laterally within a wall through cracks and voids make it more difficult to locate a leakage source. This will prolong the iterative grout injection process used to repair leaks, causing a greater interruption to business operation once the building is occupied. Waterproofing products reliant on swelling and confinement, such as bentonite sheet membranes, are especially susceptible to these voids, as they prevent complete confinement and the waterproofing performance can be compromised. In addition to voids, numerous extra penetrations through the waterproofing membrane are required to stabilize the reinforcement cage to the shoring for shotcrete, which are not required in cast-in-place concrete. The waterproofing detailing at these stabilization anchors varies depending on the manufacturer. One system relies on hydrophilic sealant around each anchor. It is important to make any adjustments to the rebar prior to sealing these penetrations to prevent displacing the seal. Internal stabilization offers the apparent benefit of eliminating numerous penetrations through the waterproofing, although it is more expensive and can be very cumbersome for the contractor to work around. Thus, internal stabilization is seldom used.