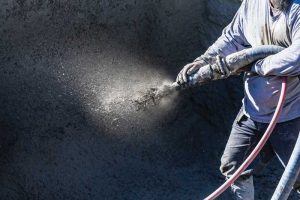
New in Section 4, timelines for the prequalification of aggregates were extended. Data on types, sizes, pit or quarry locations, producers’ names, aggregate supplier statement of compliance with ASTM C33, Standard Specification for Concrete Aggregates, and ASTM C1293, Standard Test Method for Determination of Length Change of Concrete Due to Alkali-silica Reaction, expansion data must be no more than 24 months old.
ACI 301-20 (and ACI 318-19) now permits the use of crushed hydraulic-cement concrete or recycled aggregate if documentation is provided as required by the A/E and its use is determined suitable for a particular project. Mineral fillers, conforming to ASTM C1797, Standard Specification for Ground Calcium Carbonate and Aggregate Mineral Fillers for use in Hydraulic Cement Concrete, are now permitted in 301-20, provided they are obtained from the same sources and consist of the same types as those used in concrete represented by submitted field test records or used in trial mixtures. Also, internal curing by using lightweight aggregate (limited to prewetted fine aggregate conforming to ASTM C1761, Standard Specification for Lightweight Aggregate for Internal Curing of Concrete) is now included in ACI 301.
Durability provisions in ACI 301-20 outline new requirements for sulfate exposure categories, and new guidelines for calculating the total chloride ion content of the concrete mixture (or water-soluble chloride ion content of a hardened sample), along with different limitations imposed on concrete mixtures to be qualified to reduce the potential of alkali-aggregate reactivity.
ACI 301-20 prohibits the use of aggregates determined to be susceptible to alkali-carbonate reactions in accordance with ASTM C1778, Standard Guide for Reducing the Risk of Deleterious Alkali-aggregate Reaction in Concrete. ACI 301-20 also revised the three options for qualifying concrete mixtures for resistance to alkali-silica reaction:
- Option (a) remained as previous—requiring expansion results of ASTM C1293 to not exceed 0.04 percent in one year;
- Option (b) kept the requirement for expansion results determined in accordance with ASTM C1567, Standard Test Method for Determining the Potential Alkali-silica Reactivity of Combinations of Cementitious Materials and Aggregate (Accelerated Mortar-bar Method), to not exceed 0.10 percent expansion at 16 days, and added an another requirement for submitting supporting data for each aggregate showing expansion in excess of 0.10 percent at 16 days when tested in accordance with ASTM C1260, Standard Test Method for Potential Alkali Reactivity of Aggregates (Mortar-bar Method); and
- Option (c) defines the expansion limits for moderately reactive (expansion greater than or equal to 0.04 percent and less than 0.12 percent) and highly reactive (expansion greater than or equal to 0.12 percent and less than 0.24 percent) aggregates when tested in accordance with ASTM C1293.
Alkali content in concrete, excluding that from supplementary cementitious materials (SCMs), is limited to 4 lb/cy for moderately reactive aggregates and 3 lb/cy for highly reactive aggregates. Option (c) restricts use with natural pozzolan or fly ash that has a CaO content greater than 18 percent, or for aggregate with expansion at one year greater than or equal to 0.24 percent when tested in accordance with ASTM C1293. Fly ash with alkali content greater than four percent must not be used in options (b) or (c). Specifiers are referred to ASTM C1778 for additional optional requirements for mitigating alkali-silica reactions.
Also new to Section 4 is a requirement for submitting test data for modulus of elasticity of proposed concrete mixtures. This parallels updates to ACI 318-19, in which the definition for modulus of elasticity was updated (using data from external documents and best practices) in order to address higher-strength concretes.
Section 5—Handling, Placing, and Constructing
Section 5 covers requirements for the construction of cast-in-place concrete. Included are procedures for handling, placing, finishing, curing, and repair of surface defects. The A/E is responsible for specifying the as-cast finish or type of surface finish, curing method, jointing requirements, and when required, repair materials.
ACI 301-20 updated the temperature requirements for placement in cold weather for massive metallic embedded items or bundled metallic embedded items in concrete and formwork contact surfaces to be above 10 F.
Wording was changed in reference to the placement of beams, girders, or slabs monolithically with columns or walls to clarify timing of placement. 301-20 says horizontal elements should be placed after the underlying concrete is consolidated and there is no bleed water on the surface of the vertical supporting member.
Specifiers are now required to indicate where higher-strength concrete for columns and walls is required to be integrated with floor systems. In this case, the high-strength concrete must be extended through the full floor system depth for at least 2 ft past each face of columns and walls to achieve a monolithic mass.
Surface finish SF-2 is now established as the default surface in ACI 301-20, except for metal lap pan deck formed surfaces and those surfaces that are to be buried or covered with subsequent installed surfaces, which require a surface finish of SF-1. The architect or engineer must designate portions of the structure that are to receive a special finish and include requirements such as color, texture, limited surface voids, or other features along with acceptance criteria. Field mockups may also be specified as an optional requirement. Specifiers should also review Section 6—Architectural Concrete, and determine if the selected members should be designated as architectural concrete.