The importance of transparent assemblies
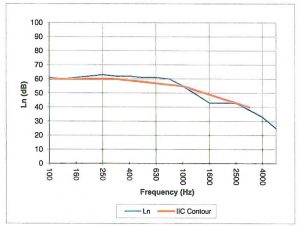
It is recommended to be cautious when a manufacturer does not explicitly list each element of the assembly. As mentioned, there may be additional insulating elements in the test assembly influencing the published IIC/STC ratings. If a manufacturer offers a generalized sound data sheet, but does not list every component of the assembly, they may be hiding additional insulation or uncommonly used construction methodologies. While the lack of mechanical fasteners in the testing assembly may produce fantastic results, real-world construction practices (especially those in the multifamily and hospitality industry) include nails and screws. Performance achieved by installing the same product will most likely produce a different result. When comparing products, it is essential to compare the details of the assembly used during testing. Was the cavity filled with insulation? Are the resilient channels spaced similarly? Was an additional underlayment or membrane used on top of the gypsum? As a best practice, specifiers should always request full testing details from a manufacturer.
When reading the acoustical testing results of any product, it is beneficial to note not only the assembly used, but also the finished flooring type. Many hard-surface floors now also have an underlayment pre-attached to the planks or tiles. These pre-attached underlayments can affect the tested ratings of a floor, making an underlayment to appear as if it offers a clear advantage after installation. This advantage only exists if the same flooring is specified in the project.
Understanding the thickness and composition of the floorcovering is also critical. All ‘luxury vinyl tiles’ (LVTs) are not alike—although most projects use 2 to 3 mm (79 to 118 mils) glue-down LVT, several manufacturers still test with 5 mm (197 mils) or even thicker products because they boost performance.
Real-world performance of acoustical mats
Lab and real-world performances are, of course, two separate conditions entirely. The authors feel a few issues need to be addressed when selecting and installing sound isolation on multifamily projects. The first factor would be the effects of load on monofilament technologies over time.
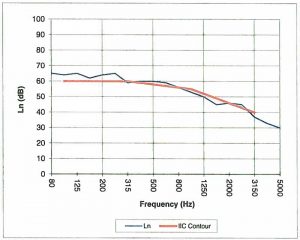
Monofilament underlayments offer mechanical resistance, which is a good thing as their sound rating is dependent on the ability to maintain the ‘spring.’ If the compression on the floor increases beyond the specification, then the amount of deflection increases, thereby reducing the acoustical properties of the mat. Every mat compresses as weight increases, and this happens over time. This mechanism is known as ‘creep,’ and is common among closed-cell, low-density foams, thick fabrics, and sparsely applied monofilament mats improperly engineered to withstand loads as small as 4.8 kPa (100 psf). Creep occurs over a period of months, although it is most rapid within the first few days of a floor being loaded. As the sound mat compresses, its density and the degree of acoustical isolation are slowly compromised.
Initial compression also takes the load of the underlayment into account. The most common mats require an underlayment pour depth of 25 mm (1 in.), resulting in a load of approximately 6 kg (13 lb). While this is well below the loads measured in the manufacturer’s specifications, this assessment does not include the finished weight of loaded kitchen cabinets, heavy appliances, and furniture. However, that is not the most significant concern.
When this mass-spring vibration technology was developed and released into the market, tile was the standard choice for finished hard-floor surfaces in multifamily and hospitality sectors. By its design, rigid tile has the added benefit of dispersing any loaded weight over its surface area, thereby increasing the area of the underlayment under compression and reducing the effective load at any given point.
Recently, the market moved to LVT and luxury vinyl plank (LVP), as these materials offer significant advantages in terms of cost, ease of installation, and selection when compared to traditional hard-surface finishes like tile and wood. These materials are flexible and do nothing to disperse point loads to a broader footprint. If the specified mat has only been tested with a rigid vinyl tile or plank, the building professional and property owner may be displeased with the acoustical performance of the actual installation.
The longevity of gypsum underlayment may also become an issue as tenants move in and out of the multifamily developments. While correctly installed, cured gypsum has high compressive strength, it may compress in a localized area if the acoustical mat below it cannot properly handle the point load of a heavy object, and thereby resulting in cracking, as the material is inadequately supported. Large wood-framed buildings inevitably settle and move, even during the construction process, and cracks in the gypsum are almost always occurring to some degree. The question is, are these cracks moving beneath a compressible sound mat? The authors believe they do. The competitive nature of the construction industry has pushed pours over 10-mm (3/8-in.) thick sound mats from what used to be 38 mm 10 years ago to as little as 25 mm in recent years. It is crucial the gypsum topping is of adequate thickness when specifying compressible sound mats.
Prior to specifying, it is important to carefully review manufacturer specifications and data sheets so that all pertinent information is considered. One may be surprised to find the acoustical products used for years have made necessary changes or innovations to accommodate the same from floorcovering manufacturers.
So considering all of this, do you recommend a specific type of underlay and or brand for a wood subfloor assembly with in floor radiant heat with LVP flooring?
There is an extra thick cork backing available that will reduce the noice to 55 using a high level LVT our HOA has been trying to find something better but there isn’t anything yet.
There is an extra thick cork backing available that will reduce the noice to 55 using a high level LVT our HOA has been trying to find something better but there isn’t anything yet.