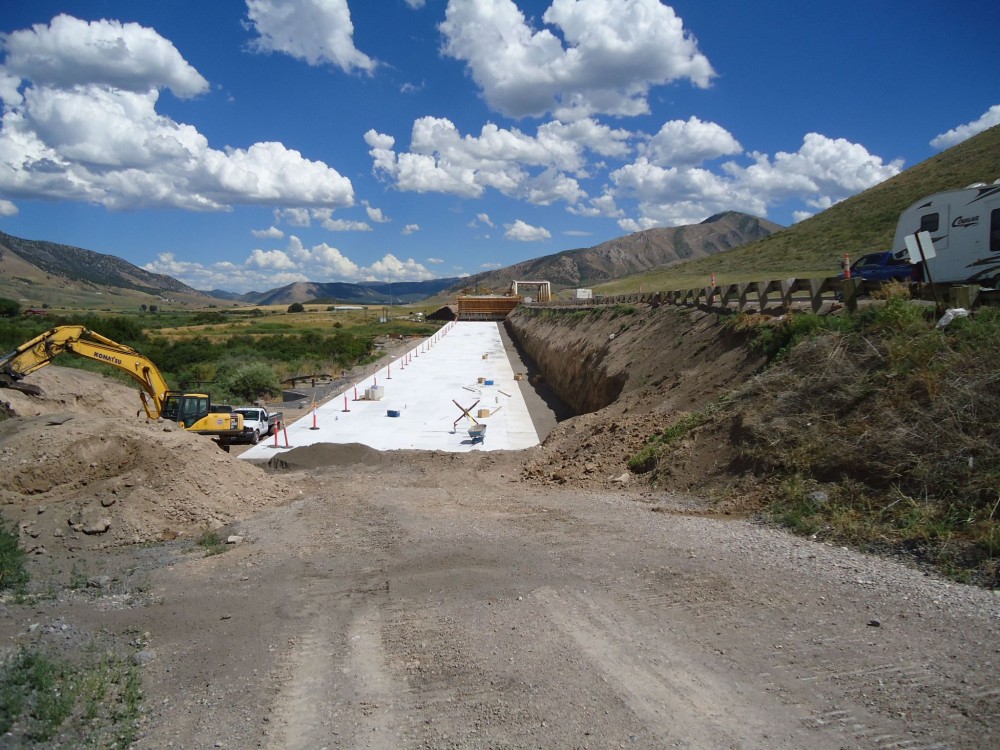
by Nico Sutmoller
On jobsites, it is increasingly common to see crews working with large, white blocks of expanded polystyrene (EPS) geofoam. From roads to new buildings, the geosynthetic material is a lightweight alternative to traditional fills that help solve multiple engineering challenges. Geofoam is specified for its soft soil remediation, slope stabilization, lateral load reduction on retaining structures, structural void fill, and buried utility protection.
Earthen fills, such as soil, crushed rock and sand, have dominated construction for centuries, as they are ubiquitous, familiar, and relatively inexpensive on a per-unit basis. As characteristics vary from one excavation source to another, and can change based on weather, traditional fills can be unpredictable. To address this limitation, project teams must conduct extensive testing—including compacting soil in phases to a percentage of dry density and then sending multiple samples to the lab to confirm results.
Geosynthetics, like EPS geofoam, are produced under controlled conditions and yield predictable and consistent engineered values, which can simplify design and construction and eliminate testing costs.
Physical properties and performance
Various physical properties play a part in geofoam performance.
oil typically weighs anywhere from 1749 to 1908 kg/m3 (110 to 120 lb/cy), depending on its composition and moisture content. Conversely, EPS geofoam weighs a small fraction of that—11.1 to 45.3 kg/m3 (0.7 to 2.85 lb/cy), depending on the density specified. Geofoam is also much lighter than other common fills, including those classified as “lightweight.” (See Figure 1).1
Geofoam’s ultra-low weight is a common deciding factor in specifying the material for soft soil remediation, as it imparts small dead loads on poor load bearing soils. Additionally, its lightness enables crews to place EPS geofoam blocks by hand, reducing the need for heavy equipment, and simplifying construction on tight jobsites and steep slopes.
One truck can carry approximately 92 m3 (120 cy) of geofoam—a volume equal to 12 dump trucks of earthen fill. This helps reduce construction traffic and transportation costs.
Compressive resistance
Despite its light weight, EPS geofoam is engineered for high strength. The material’s compressive resistance ranges from about 15,178 to 128,223 Pa (317 to 2,678 psf) at a one percent strain. Recently identified Westergaard modulus of subgrade reaction, “k” values confirm geofoam has better bearing capacity than most foundation soils. The Westergaard modulus estimates the support of layers below a rigid pavement surface. As long as combined dead/live loads do not exceed one percent strain, EPS geofoam will never creep or experience plastic yield. Geofoam has been successfully used as a sub-base material for pavement sections bearing the live loads of locomotives and jumbo jets.
Water absorption and buoyancy
As with EPS insulation, EPS geofoam has a closed-cell structure that limits water absorption; with proper drainage, weight gain is not expected. The material’s water-resistant nature is demonstrated by its frequent use in floating structures, such as piers.
As EPS geofoam is buoyant, it is important to consider uplift forces in applications where the material will be partially or fully submerged. Buoyancy can be minimized by installing geofoam above the water table and ensuring suitable drainage. Additionally, the surcharge from overlying soils or pavements is frequently sufficient to offset uplift forces. Where high water exposure cannot be avoided, supplemental restraints (e.g. screw anchors or restraining straps) might be required.
While buoyancy is a factor to be evaluated, it does not have to be a problem, as demonstrated by the use of geofoam in a number of levee projects in the country. In such applications, EPS geofoam is typically used as a lightweight fill within levee embankments constructed on poor load-bearing soils.
Damaging elements
Correctly specified and installed EPS geofoam is durable and stable, so it is considered permanent, lasting for decades throughout a project’s life. It neither decomposes nor is affected by freeze-thaw cycles or road salts, and does not leach toxic chemicals or heavy metals into soil or groundwater.
EPS is combustible, so it is important to check with the manufacturer to learn whether the geofoam includes a flame retardant. Flammability is typically only a concern if open-flame procedures are occurring during installation, as the material is usually isolated by membranes, soils, or pavement in the finished application.
Sizes
EPS geofoam blocks can be ordered in a range of sizes up to 1.2 x 1.2 x 7.3 m (4 x 4 x 24 ft). Standard blocks come as rectangles, but can be custom-cut in the factory to meet various job requirements, including sloped or curved pieces. Additionally, EPS geofoam is easy to trim in the field, as needed, using saws or a hot-wire cutting tool.
Geofoam applications
As a durable, lightweight material, geofoam helps solve many engineering challenges. Some common solutions are described in this section.
Soft soil remediation
Poor load-bearing soils can be a problem in wide geographic regions or even limited locales with certain adverse conditions. For example, glacial tills are present in large swathes of the Pacific Northwest and near the Great Lakes, while peat, soft clay, or sandy soils are often found in former lake beds.
Such soils must be remediated because they do not provide a stable, firm foundation for civil engineering projects or large buildings. Common remediation methods such as surcharging, pile-driving, or over-excavation and replacement with imported soils, are time-consuming and costly. EPS geofoam provides a simple and cost-effective alternative, as the material is about 100 times lighter than soil, yet can support high applied loads. Additionally, unlike other lightweight fills such as shredded tires or wood chips, EPS geofoam is homogenous and transfers loads uniformly, eliminating differential settlement.
In Renton, Washington, adjacent to glacially formed Lake Washington, renovation of city hall was undertaken on soft soils. The building refurbishment required new handicap ramps. To avoid post-construction settlement, the project team installed 3822 m3 (5000 cy) of EPS geofoam blocks to support the ramps.
Slope stabilization
Geofoam’s light weight also makes it an ideal solution to stabilize slopes prone to failure, without changing the final slope geometry. Geofoam reduces the weight of a slope’s driving block, lessening the risk of landslides. The material is also easy for crews to lift and place by hand on steep slopes or uneven terrain where earth-moving and compaction equipment is not feasible.
Examples of hillside road projects that used EPS geofoam for slope repair include:
- U.S. 101 near Willets, California;
- U.S. 50 near Montrose, Colorado;
- Window Rock Highway, Arizona; and
- State Highway 12 near White Pass, Washington.
Lateral load reduction
EPS geofoam has a low Poisson’s ratio (.05) and high coefficient of friction (.60), which helps enable block placement in a way that replaces the sliding soil wedge above the angle of repose, thereby reducing lateral loads on retaining structures and building foundations. Poisson’s ratio measures the degree to which a material gets thinner as it is stretched. For example, a .05 ratio indicates low ‘stretchiness,’ whereas a ‘stretchy’ material such as rubber has a high Poisson’s ratio of approximately .48.
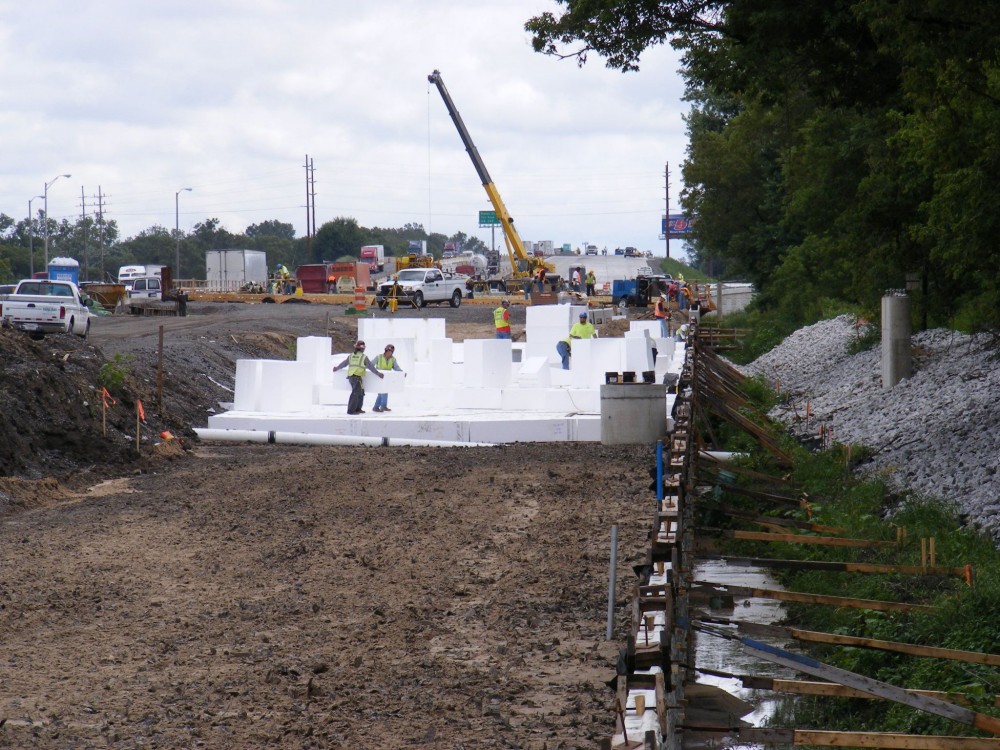
The need for geogrids or mechanical tiebacks is reduced, or sometimes eliminated, and project teams can construct a wall that acts more like a fence than a retaining wall. The benefit is a reduction in labor and material costs by requiring less:
- over-excavation;
- robust forming;
- structural steel;
- concrete wall thickness; and
- footings.
The material also allows for higher walls in narrow rights-of-way, which can lower property acquisition costs.
The project team widening the Pacific Street Bridge over I-680 in Omaha, Nebraska, used geofoam to simplify construction. For such projects, crews typically would have removed and replaced the existing abutment walls, which were not designed to withstand increased lateral loads induced by fill for additional lanes. Instead, the contractor excavated the soil between the existing abutment wall and the soldier piles, then formed and extended the wall. Approximately 1529 m3 (2000 cy) of EPS geofoam was installed as a lightweight back-fill for the bridge approach.
Buried utility protection
Another way geofoam’s light weight can benefit civil construction is by reducing loads on buried utilities. This is a typical challenge in urban construction, where dense utility runs underlie many road jobs. In Seattle, contractors used EPS geofoam to build a tightly spiraled ramp on Royal Brougham Way that crossed over large stormwater and sewer mains. One of those was a century-old, brick-lined concrete pipe with timber piles that would have been at risk for failure under heavy soil fills.
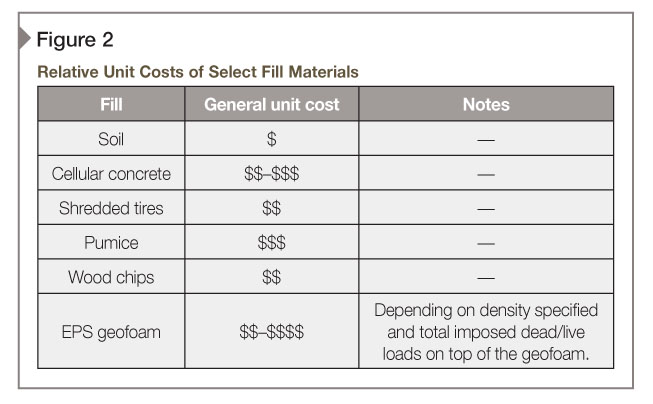
Civil engineering professors at the University of Utah found using EPS geofoam as a soil-replacing cover for buried pipelines reduces vertical and lateral stresses on pipes, and decreases axial strain and large bending stresses on pipes during seismic events, which helps protect them from damage.2
Structural void fill
EPS geofoam can be used as a structural void fill in concrete forming operations, such as:
- bridge column formwork;
- block-outs in wall-forming;
- behind retaining structures;
- reverse slopes or added elevations between structural and topping slabs;
- stairs and stadium seating; and
- rooftop pool or plaza decks with pavers or cast-in-place slabs.
A new wastewater treatment plant built by the Fairfield-Suisun Sewer District in Solano County, California, provides a good example of wall-forming using geofoam. The plant’s ultraviolet (UV) disinfection facility included three concrete water channels sized 2.1 x 2.1 x 15.2 m (7 x 7 x 50 ft).
A common method for constructing such channels and similar structures is to:
- set forms for two parallel stem walls;
- pour and cure the concrete walls;
- place and compact fill between the walls; and
- conduct a second pour for the topping slab.
As an alternative to this time-consuming process, Kaweah Construction Co., used EPS geofoam blocks to constitute half of the form, which simultaneously displaced the void and easily bore the concrete topping slab’s weight. The contractor was thus able to do a monolithic pour of the top and walls at the same time. They saved time and money by reducing formwork and the concrete pouring schedules.
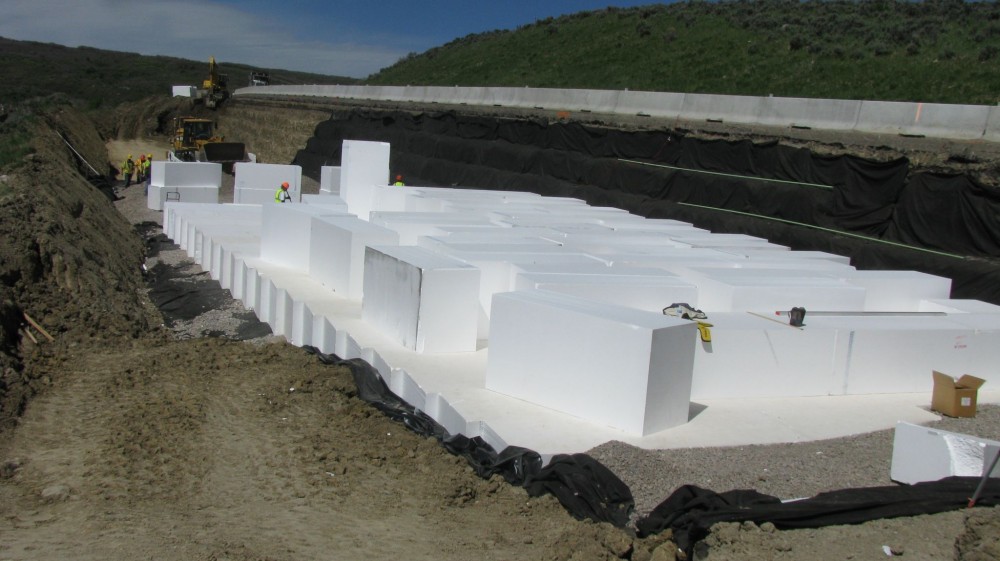
Conclusion
As with other lightweight fills, the unit cost of EPS geofoam is typically higher than traditional materials (Figure 2 ). However, as a report prepared for the Transportation Research Board notes, this is “usually more than offset by savings when overall project costs are considered.”3 As discussed, savings accrue from reduced forming, less excavation, reduced transportation, and faster construction.
EPS geofoam is widely available throughout North America from numerous manufacturers. To ensure a quality product, it is important to ensure the specified geofoam is manufactured to ASTM D6817, Standard Specification for Rigid Cellular Polystyrene Geofoam. A select few manufacturers maintain a third-party certification program through Underwriters Laboratories (UL) to ensure physical property compliance with this standard.4
Notes
1 For more, see Guideline and Recommended Standard for Geofoam Applications of Highway Embankments, by Timothy D. Stark, David Arellano et al., prepared for Transportation Research Board, July 2004. Additionally, see Applications of EPS Geofoam in Design and Construction of Earthquake Resilient Infrastructure, by Steven Bartlett, PhD, et al., prepared for 2011 EPS Geofoam Conference held in Oslo, Norway. See also, “Insulfoam GF Capabilities” at www.insulfoam.com. (back to top)
2 For more information, see Protection of Steel Pipelines from Permanent Ground Deformation Using EPS Geofoam, by Stephen F. Bartlett et al. This can be accessed at www.civil.utah.edu. (back to top)
3 See Geofoam Applications in the Design and Construction of Highway Embankments, by Timothy D. Stark et al., and prepared for National Cooperative Highway Research Program of the Transportation Research Board in July 2004. (back to top)
4 For more information on attributes and applications for EPS geofoam, one should contact a manufacturer or visit the EPS Industry Alliance at epsindustry.org/other-applications/geofoam. (back to top)
Nico Sutmoller is the geofoam specialist for Insulfoam, a division of Carlisle Construction Materials. He has advised project teams throughout the United States and internationally on geofoam installations since 1999. Sutmoller can be reached at geofoam@insulfoam.com.