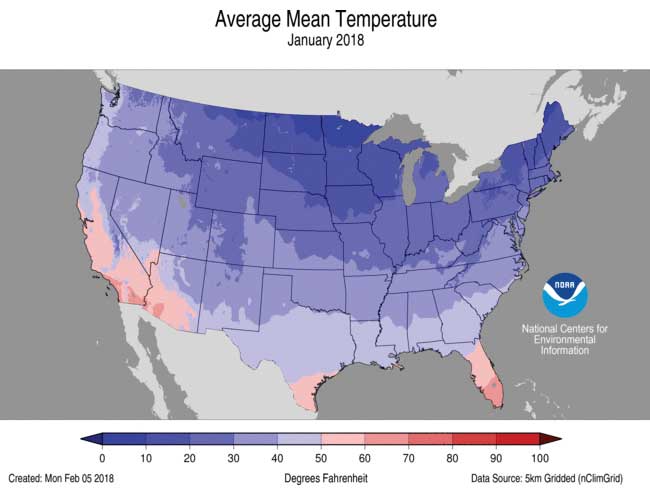
Image courtesy NOAA National Centers for Environmental Information (NCEI)
First steps
Following the established Cx guidelines, the first step in the commissioning of a building is to develop a thorough understanding of how the building will
be used and how the owner expects the building to perform. These understandings and expectations are compiled into the OPR document. With regard to building enclosures, the OPR would include (but would not be limited to): the location of the building; the anticipated interior operating conditions; and the sensitivity to water intrusion, temperature control, and air infiltration. The OPR establishes how quality and success will be measured for the project. To put it another way, the OPR establishes the goals for the building before the design process begins. It is easy to see how the expectations of the owner of an indoor swimming pool in Montana will be very different from the expectations of the owner of a data center in Florida. Therefore, it is important everyone has a clear understanding of the OPR at the outset of a project.
Once the OPR is established, the design team can develop the materials and systems that will become the basis of the design (BOD) for the project. At a minimum, the building enclosure BOD will include material and system descriptions for:
- the foundation drainage;
- below-grade waterproofing;
- water vapor control (above and
below grade); - air infiltration;
- insulation;
- fenestrations (doors, windows,
louvers, etc.); - exterior finish materials; and
- roofing systems.
Then, the construction documents (the project drawings and specifications) are developed based on the OPR and the BOD. The design must integrate the OPR with the requirements of the applicable building codes, the effects of the environment where the building will be located (temperature, humidity, rainfall, etc.), the effects of the owner’s use of the building, the requirements of the manufacturers of the BOD products, and the applicable industry standards of care. This can be a significant challenge. For most routine building uses in familiar geographic locations (hygrothermal regions such as hot-humid, hot-dry, or severe cold), well-established design and construction practices are relied upon during the design of the building. For sensitive projects, buildings in difficult locations, and situations with complex uses, dynamic hygrothermal modeling of the various assemblies may be required to ensure the building is going to perform as desired and designed.3 It is the responsibility of the project design team to decide whether established materials and methods are appropriate or whether hygrothermal modeling is necessary.
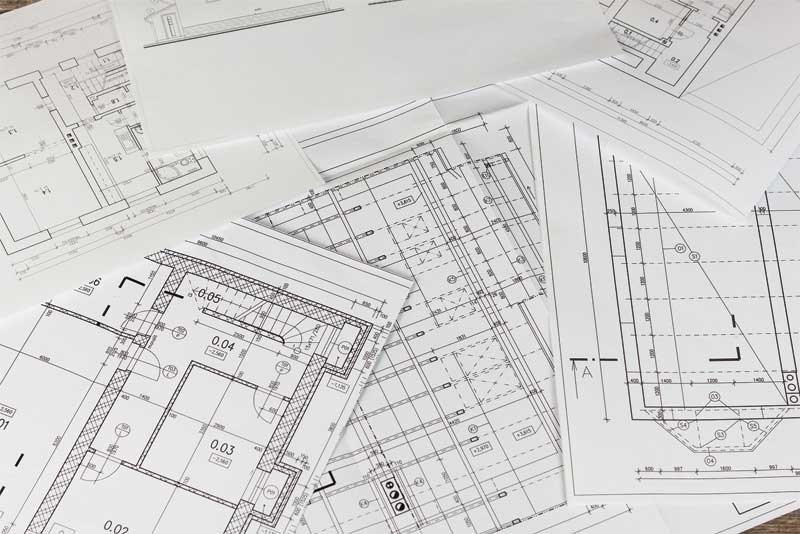
Photo © BigStockPhoto.com
Review design documents
The next step in the BECx process is a review of the design documents. As indicated above, it is preferable for the BECx team to be a part of the development of the design from the very outset of the project. This early involvement can potentially avoid having to substantially change a design at a time when such changes would lead to project delays and/or unanticipated expenses. During the design review or collaboration, the BECx team is not replacing the designer of record (DOR). Rather, the reviewers are comparing each phase of the design with the OPR, the BOD, manufacturer’s requirements, common constructability concerns, and the industry standards of care. Further, experienced reviewers will be drawing on lessons learned from past projects. A good review includes not only comments on potential problems, but also areas where the DOR could consider an alternate approach for the benefit of the building. The design review is an attempt to identify as many potential construction problems as possible before the work begins. This step in the BECx process is critical because identifying a design error later, during construction, will typically lead to project delays and unanticipated costs (change orders), and it is in everyone’s best interest to address those potential issues as early as possible.
The BECx plan should include a review of the product submittals and shop drawings before construction begins. Skipping this step typically results in materials being installed on the building that are not consistent with the design intent, materials added that were not a part of the design, material incompatibility, or materials being omitted, preventing the satisfactory performance of the building enclosure.