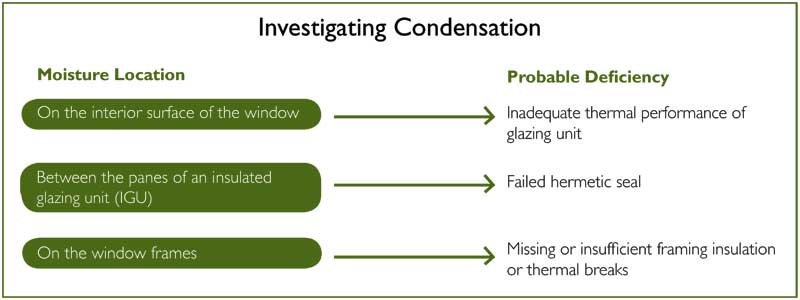
Thermal performance
With the advent of insulating glass units (IGUs), low emissivity (low-e) coatings, thermal breaks, and other heat-conserving developments, today’s window technology has become very advanced to the point where high-end, thermally-improved windows can rival the insulation value of a stud-cavity wall. But rising energy costs are not the only reason to address thermally-deficient windows; exposure to exterior temperature and humidity fluctuation through insufficiently insulating windows carries a risk of damage to interiors due to condensation. Moisture in the air will condense on any surface in a room colder than a specific temperature, or dew point, which is associated with the relative humidity (RH). Windows with poor thermal performance readily conduct cold ambient temperatures, leading to moisture condensation on windows and surrounding surfaces, and, eventually, water damage and possible fungal growth.
The occurrence of condensation may merely be a sign the interior is being maintained at high heat and humidity when it is cold outside. However, under normal conditions, frequently occurring condensation is a sign the windows are performing poorly with respect to thermal insulation. Check Figure 1 to determine the most likely explanation for recurring condensation in various locations on the window assembly.
Window exposure
One of the most important considerations for evaluating existing windows and scheduling repairs has nothing to do with the window itself. The location of a window on the façade and its exposure to exterior elements must be also considered when determining the unit’s risk for damage and deterioration, or when assessing any deficiencies in its performance.
In general, the many factors to consider for the exposure of a building include:
- the structure’s height relative to adjacent buildings;
- density of surrounding buildings;
- geography and topography of the area, such as the climate and proximity to the coast; and
- orientation/elevation on the building (sun exposure).
In addition to the general exposure characteristics of the structure as a whole, each individual window is subjected to a unique set of environmental forces, which impact its risk for deterioration.
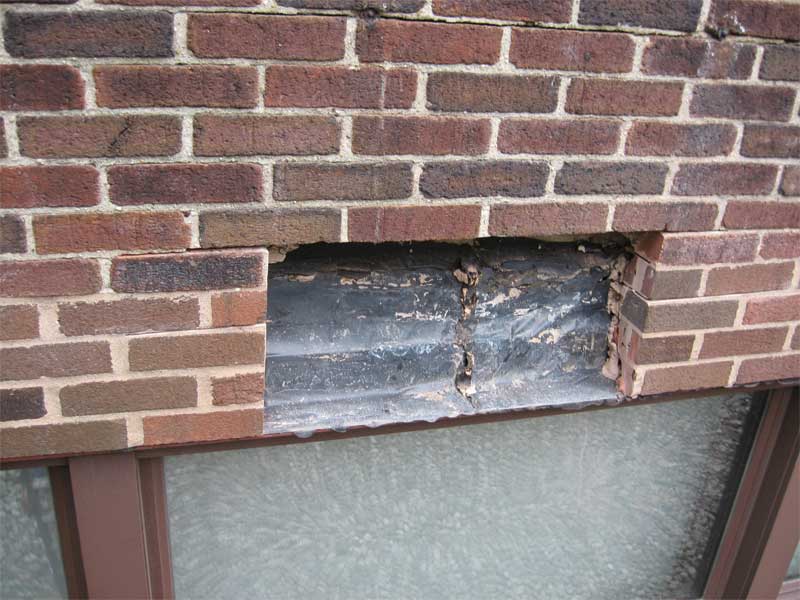
When reviewing windows for water infiltration, the design team must consider the prevailing direction for wind-driven rain, as windows in that orientation are at a greater risk for moisture ingress than leeward-facing windows. The orientation of a window is also important to thermal performance evaluation, as exposed windows on a south façade receive considerably more sunlight than windows on the north face.
Overhang protection for windows can be provided by various building components, such as exterior louvers/sunshades, roofs, awnings, cornices, decorative elements, or balconies. Even the degree to which a window is recessed into a wall cavity affects its exposure risk, because rain and snow drain clear of a recessed window. Architectural features such as sills, ledges, terraces, and other elements can contribute to moisture infiltration from standing water or snow drifts at the base of the window.
A window’s level of noise control, especially in dense urban areas or adjacent to noise-producing equipment, can be a critical performance criterion for occupant comfort. Additionally, the selection of glass should achieve a balance of visible light transmittance and avoidance of glare.
In some orientations and locations, wind pressure and suction forces can be severe enough to compromise a window’s structural integrity or capacity for air infiltration protection. Some warning signs include:
- cracked glass;
- misaligned frames;
- difficult operation;
- heavy drafts; and
- cloudy appearance between panes.
To ensure windows adequately protect against the spread of fire, building codes and zoning ordinances establish a fire separation distance, or space between buildings. Depending on this distance, building codes also dictate the allowable area of protected and unprotected wall openings, taking into account additional fire-resistance measures (e.g. sprinkler systems). Fire-tested window assemblies and materials are considered protected openings. The design team can establish how the building code and adjacent buildings affect the window sizes, number, and placement.