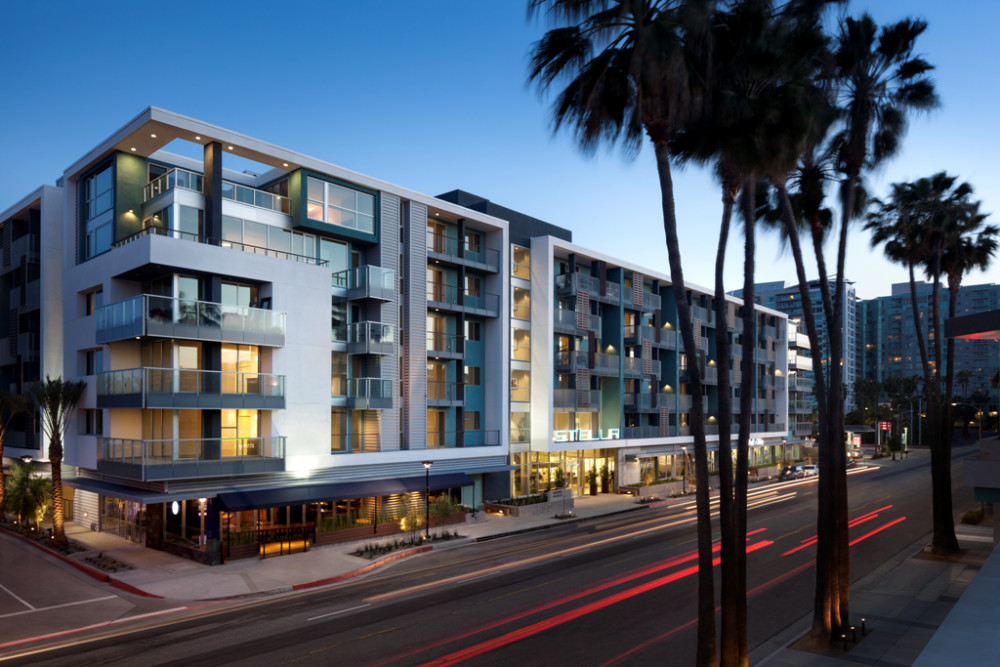
By Scott Breneman, PhD, PE, SE
As multi-family developers and design teams strive to increase urban density in a way that is affordable, wood framing continues to appear as a popular material choice. For the Stella luxury development in Marina del Rey, California, an innovative light wood-frame design allowed the team to stay within budget, while still meeting code requirements, and providing resort-style amenities in one of the highest seismic areas of the country.
The original design of the development maximized a saleable area of 244 condominium units in two four-story buildings. By increasing one of the buildings to five stories, the new team was able to keep the same unit count while reducing the overall footprint—making room for shared amenities such as a heated saltwater pool and a beach.
Multiple structures and mixed construction types
To make the most of the location, the team took a unique approach to developing the site. Two L-shaped buildings—one five-story Type III-A construction and the other four story of Type V-A—were combined on a shared single-story Type I-A podium. The L-shaped buildings each consist of two independent structural systems with a seismic joint at the intersection of the legs of the ‘L.’
After a quick cost analysis, it became clear a mixed-construction-type podium configuration offered better value than a single Type I building. This method allowed the design team to construct the 60430-m2 (650,466-sf) complex for approximately $2782 per net rentable square meter ($260/sf).
A major difference between Types III and V construction is the wood type. Type III requires use of non-combustible material or fire retardant-treated (FRT) wood for exterior wall framing, while Type V construction allows untreated wood building components throughout the structure. The combination of FRT wood on the exterior and untreated wood inside provides a cost-effective framing system to build up to the limits of Type III construction.
The design team specified FRT studs, rim boards, and plywood for the exterior walls of the five-story structure to adhere to requirements for passive fire resistance in Type III construction. Floor framing was typically 302-mm (11 7/8 in.) wood I-joists with parallel strand lumber (PSL) and laminated veneer lumber (LVL) beams. Exposed glued-laminated timber (glulam) beams were used in public spaces for their aesthetic appeal.

The project features balconies—many supported on two or three sides by exterior walls. The typical floor framing of the balconies employed dimension lumber running parallel to the primary direction of the exterior walls supported by perpendicular walls and/or columns, as opposed to the more common approach of cantilevering through the exterior walls. Under the International Building Code (IBC), FRT wood was unnecessary for the balconies because they are protected by National Fire Protection Association (NFPA) 13, Standard for the Installation of Sprinkler-compliant automated sprinklers.
The desire for a modern aesthetic with luxury-level amenities also added complexity. The team placed several residential units atop large amenity spaces that needed to be more open. In those situations, steel framing was used to transfer the bearing wall loads from units above the amenity spaces.
To provide lateral resistance on the exterior walls while avoiding relatively expensive moment frames, the team developed a design with 1.5-m (5-ft) shear wall segments at regular intervals along the exterior wall. For shear walls with windows, they also used a ‘force transfer around openings’ design to accommodate wall segments that do not meet the minimum shear wall aspect ratio requirements on their own. By blocking and strapping above and below the window openings, the engineers created shear piers the height of the windows, using the height of the opening for the aspect ratio.
As a manufacturer of glulam for over 50 years we are so excited to see wood being used to replace other building materials. Wood is one of the most predictable, sustainable and healthy building materials out and there. We are proud to be apart of the glulam manufacturing/construction industry and look forward to this exciting new chapter wood design and development.
If anyone has any questions about engineering, design, cost or anything else they can get in touch with us at http://www.unalam.com!
Go wood!