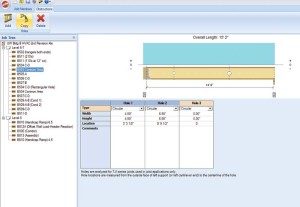
Images courtesy Weyerhaeuser
Coordinating efforts
Along with their strength and consistency, I-joists are extremely adaptable to accommodate HVAC ducts, pipe runs, low-voltage wiring, and other elements requiring pathways through the floor system. Large, numerous holes can be cut into I-joist webs in the field, or prior to jobsite delivery, without effectively compromising their structural performance, provided certain guidelines for hole number, size, and placement are followed. This is in sharp contrast to solid-sawn lumber, which is much more limited in the size and number of holes it can accommodate.
Even with these capabilities, the increasing complexity of numerous elements can lead to problems if the task is not pre-planned and properly communicated among the subcontractors. Mistakes in hole-cutting—such as cutting too close to the end, too close together, or into the flange—can affect the joist’s structural performance and lead to expensive and time-consuming red flags, joist repair, or replacement. Additionally, poor planning can lead to inefficient ductwork, with longer runs and unnecessary bends, and can complicate plumbing installation.
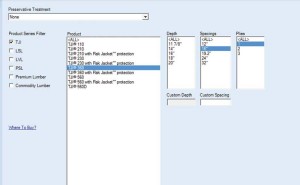
Problems are amplified because trades rarely communicate, or change from project to project; they are infrequently brought into the planning stages. Often, the HVAC installer is hired long after the planning process is complete and has little, if any, involvement in engineering ductwork into the layout.
One of the best ways to manage these problems and space constraints is with advanced planning. Involving all participating trades up front allows mechanical layouts to be chosen based on the most ideal and practical locations, and the ability of the I-joists to accommodate the required holes. Structural frame design programs can help by laying out each joist and beam to scale and identifying framing conflicts with mechanical systems before construction even begins. Layouts can then be modified to accommodate non-structural requirements, such as plumbing drops, and holes in I-joists can be laid out ahead of time.
All this information can be included in a floor layout plan, giving framing crews a precise picture of what needs to be done. This greatly simplifies work for framers and mechanical installers in the field. Technology can take the concept even further as joist holes can be pre-cut to help reduce the risk of crews compromising the structure by cutting holes outside of a joist’s design parameters (e.g. holes too large or close to the joist ends).
Solutions and software
Design software at the dealer level allows the supplier to turn floor plans into step-by-step framing guides and precise framing packages. Working with the builder and subcontractors, the lumber and building material dealer designs the structure using 3-D modeling tools to determine where to route components, overlaying each mechanical element onto each other to view the entire structure as a system. From there, the dealer can provide installers with detailed instructions or use computer-controlled fabrication equipment to produce floor framing packages that install faster, safer, and with less material waste than conventional methods.
Pre-cut I-joist holes can be included in the package, eliminating the need to cut them onsite and helping to avoid potential complications. The software can also mark attachment points for intersecting framing members such as the juncture of rim board and I-joists—this ensures framing contractors do not alter the layout and potentially impede the pre-cut joist openings.
Such technology was a vital tool for a recent residence hall building at a university in Seattle. The I-joist manufacturer met with HVAC and plumbing subcontractors for the five-building project in advance, walking them through the software program and educating them on how to plan for holes in the joists.